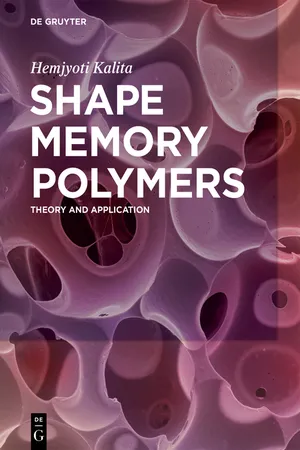
This is a test
- 150 pages
- English
- ePUB (mobile friendly)
- Available on iOS & Android
eBook - ePub
Shape Memory Polymers
Book details
Book preview
Table of contents
Citations
About This Book
The basic principles and mechanism of shape memory polymers, classification of shape memory polymers, and related characterization techniques are illustrated. Furthermore, an overview of the broad spectrum of applications in various fields for shape memory polymer is presented. Special focus will be given to hyperbranched, blended, interpenetrating and bio-based shape memory polymers, as well as shape memory polymer nanocomposites.
Frequently asked questions
At the moment all of our mobile-responsive ePub books are available to download via the app. Most of our PDFs are also available to download and we're working on making the final remaining ones downloadable now. Learn more here.
Both plans give you full access to the library and all of Perlego’s features. The only differences are the price and subscription period: With the annual plan you’ll save around 30% compared to 12 months on the monthly plan.
We are an online textbook subscription service, where you can get access to an entire online library for less than the price of a single book per month. With over 1 million books across 1000+ topics, we’ve got you covered! Learn more here.
Look out for the read-aloud symbol on your next book to see if you can listen to it. The read-aloud tool reads text aloud for you, highlighting the text as it is being read. You can pause it, speed it up and slow it down. Learn more here.
Yes, you can access Shape Memory Polymers by Hemjyoti Kalita in PDF and/or ePUB format, as well as other popular books in Physical Sciences & Chemistry. We have over one million books available in our catalogue for you to explore.
Information
1Shape memory polymers
1.1Introduction
Shape memory polymers (SMPs) are stimuli-responsive smart materials that can respond dynamically to the environmental stimuli [1–4]. Nature shows numerous examples of stimuli-responsive phenomenon. For example, sunflowers bend toward the sun to maximize light exposure, the leaves of Mimosa pudica fold inward quickly when they are touched, and chameleons change color according to the environmental situation [1, 5]. Thus, to mimic nature, huge efforts have been emphasized to design stimuli-responsive polymers. The first SMP, a poly-(norbornene)-based polymer (Tg = 35–40 °C), was invented in 1984 by CDF Chimie Company, France [6, 7]. Two more SMPs were also invented soon after it; one was poly(trans-isoprene) (Tg = −68 °C), which was invented in 1987 by Kurare Corporation, Japan, and another one was poly(styrene-butadiene) (Tg = 60–90 °C) by Asahi Company, Japan [8]. However, all these SMPs suffered the same problem with limited processability. Along this time frame, thermoplastic polyurethane (TPU) SMP was invented by Mitsubishi Heavy Industries Ltd., Japan [9]. It stimulated the significant interest in SMP, presumably due to the versatility of urethane chemistry with wide range of Tg and easy processability. Currently, Cornerstone Research Group, USA, has developed and commercialized polystyrene-based SMP (Veriflex®, VerilyteTM and VeritexTM); SMP Technologies Inc., Japan, thermoplastic and thermoset polyurethane-based SMP (DiAPLEXTM); Composite Technology Development, Inc., USA, epoxy-based SMP (TEMBO®); Lubrizol Advanced Materials, USA, aliphatic TPU-based SMP (Tecoflex®); MedShape, Inc., USA, polyether ether ketone-based SMP (Morphix®, ExoShape®); and Norland Products Inc., USA, UV-curable polyurethane-based SMP (NOA-63).
SMPs have taken paramount interest in recent times because of their potential application in numerous fields, for example, smart actuators, aerospace engineering, automotive engineering, textile engineering and most prominently as smart biomedical devices [10–17]. Ni–Ti alloy (Nitinol) is the most extensively used shape memory material because of its good shape memory performance, excellent mechanical properties, good biocompatibility and so on [18]. However, the shape memory alloys (SMAs) have some disadvantages such as low deformation rate, high stiffness, high weight, high cost and nonbiodegradability. SMPs have some advantages such as easy processing, lower density, larger recoverable strain, tunable transition temperatures, multiple shape recovery ability, lower cost and lower toxicity when compared to the SMA (Table 1.1). SMPs are smart materials that can transform their shapes in a controlled manner when exposed to a suitable external stimulus such as heat, light, solvent, pH, magnetic field and electric field [19–24]. SMPs have the ability to memorize specific macroscopic and permanent shape. They have the ability to fix a temporary shape under specific temperature and stress, and can revert back to their original shape on application of appropriate external stimulus. The recovery of original shape from the deliberated fixed temporary shape is known as shape memory effect (SME). SME is quantified by the shape fixity and shape recovery function. The shape memory functions, i.e., the shape fixity and shape recovery of polymer network, are the freezing and activation of the macromolecular chains below and above a transition temperature (Ttrans), respectively. The extent to which the switching segment is able to fix the temporary shape is called the shape fixity. The extent to which it recovers the original shape from the temporary shape on exposure of stimulus is called the shape recovery. The shape recovery time is a shape memory property which refers to the time that SMP used to take recovers the permanent shape from its fixed temporary shape. The Ttrans can be either a glass transition temperature (Tg) or a melting temperature (Tm) [25, 26]. For amorphous polymers, Tg is considered as Ttrans, whereas for crystalline polymers, Tm is considered as Ttrans. Moreover, for semicrystalline polymers, either Tg or Tm can be used as Ttrans. However, Tm is being considered as the preferred Ttrans because it is sharper than the Tg [27]. Shape memory behaviors observed through shape memory cycle consist of three successive steps. The shape memory cycle is referred to the evolution of stress (or force), strain and temperature during thermomechanical cycling of an SMP.
Table 1.1: Comparison of the properties of SMP and SMA.
Physical properties | SMP | SMA |
Density (g/cm3) | 0.9–1.1 | 6–8 |
Extent of deformation (%) | 250–800 | <8 |
Force required for deformation (MPa) | 1–3 | 50–200 |
Recovery temperature (°C) | 25–90 | −10–100 |
Recovery stress (MPa) | 1–3 | 150–400 |
Recovery speed (s) | >1 | <1 |
Processing conditions | <200 °C, low pressure | >1,000 °C, high pressure |
- Deformation: The SMP is first deformed to a predetermined stress or strain at the deformation temperature (Td, Td > Ttrans), at which the material becomes soften (modulus drop).
- Fixing: The deformed sample is cooled under constant stress or strain below Ttrans. This causes the material to attain a more rigid state, in this case the semicrystalline state, therein immobilizing the constituent polymer chains and allowing fixing or freezing of the deformation as latent strain energy.
- Recovery: The temporarily deformed sample, i.e., fixed shape is reheated above Ttrans without any stress (unconstrained). The stored strain energy is then released owing to the regained chain mobility and it returns to its original shape. The elastic strain generated during deformation is the driving force for the shape recovery.
1.2Molecular mechanism of SME
Most of the polymers perform SME because polymer chains have tendency to form network structures. However, limited numbers of SMP are used in practical applications, due to their structural drawbacks (too low or too high Ttrans or poor mechanical properties). The molecular mechanism of thermally induced SMP through which SME observes is shown in Figure 1.1. Cross-links and switching segments are the key components at molecular level to exhibit the SME. The cross-links or netpoints determine the permanent shape of SMP which inhibits slippage of the macromolecular chains under large deformations, whereas switching segment absorbs the external stress and maintains the temporary shape [6, 28]. The netpoints may be either chemical (covalent bonds) or physical (secondary interactions or entanglements) in nature. Physical cross-linking is obtained in a polymer whose morphology consists of at least two segregated domains. In such morphology, the domain related to the highest thermal transition temperature acts as physical netpoints which is called a hard segment. The domain associating with the second highest thermal transition acts as molecular switches, which is called a switching domain. The molecular switches must be able to fix the deformed shape temporarily under environmental conditions by forming additional reversible cross-links. These additional temporary cross-links can be formed by physical interactions or by chemical bonds which prevent the recoiling of the deformed chains. Physical cross-links are obtained through a solidification of switching segments by vitrification or crystallization that enables the storage of entropic energy in the system [18]. After reheating, the crystallites will melt or the glassy domains will soften, resulting in the release of entropic energy by recoiling the chains that drive the material to return to its original shape. Chemical cross-links are obtained by reaction of two functional groups under formation of a chemical bond that is able to cleave by external stimulus can be used as molecular switches.

The aforementioned discussion implies that the polymer SME is an entropic phenomenon. From the molecular point of view, it is an activation and freezing of molecular chains by a temperature change. In the permanent shape, the macromolecular chains within the SMP network structure are at the lowest energy (highest entropy) state, which is thermodynamically favorable. The conformation of the chains would change and raise the energy state of the material, when macroscopic deformation takes place in the permanent shape. At the deformation stage, when it is cooling, freeze the molecular chains mobility, which led to the kinetic trap to maintain the system in the high energy state. The entropic energy is released, once the kinetic trap is removed by reactivating the chains mobility (e.g., by heating) and as a consequence recover the original shape by driving the molecular chains to return to their lowest energy (highest entropy) state. The storage and release of entropic energy is responsible for the shape fixing and recovery of the SMP. To satisfy the entropic phenomenon, the system should not have slippage of entire polymer chains that result in macroscopic deformation but no entropic change. An illustration of shape recovery of shape memory polyurethane in hot water at 60 °C is shown in Figure 1.2.
The modulus (E)–temperature (T) behavior of the materials is of basic importance with regard to understanding the shape fixity and shape recovery effect. A high glassy state modulus (Eg) of material exhibits high shape fixity during cooling and unloading, whereas high rubbery state modulus (Er) leads to high elastic recovery at high temperature. The large modulus ratio (Eg/Er) of the material provides the high shape recovery effect. Further, a sharp transition from glassy to rubbery state leads to the material sensitive to temperature variation.

1.3Hyperbranched SMPs
Recently, hyperbranched SMPs have taken wonderful interest because of their unique c...
Table of contents
- Cover
- Title Page
- Copyright
- Contents
- 1 Shape memory polymers
- 2 Classification of shape memory polymers
- 3 Characterization techniques for shape memory polymers
- 4 Shape memory polyurethanes: From materials to synthesis
- 5 Applications of shape memory polymers
- 6 Future directions
- Index