
This is a test
- German
- ePUB (handyfreundlich)
- Über iOS und Android verfügbar
eBook - ePub
Stahltragwerke im Industriebau
Angaben zum Buch
Buchvorschau
Inhaltsverzeichnis
Quellenangaben
Über dieses Buch
The book deals with a significant area of steel construction? industrial building. The eight chapters describe all the important aspects of this field. A reference book for daily tasks and for rapid introduction into new fields of work.
Häufig gestellte Fragen
Gehe einfach zum Kontobereich in den Einstellungen und klicke auf „Abo kündigen“ – ganz einfach. Nachdem du gekündigt hast, bleibt deine Mitgliedschaft für den verbleibenden Abozeitraum, den du bereits bezahlt hast, aktiv. Mehr Informationen hier.
Derzeit stehen all unsere auf Mobilgeräte reagierenden ePub-Bücher zum Download über die App zur Verfügung. Die meisten unserer PDFs stehen ebenfalls zum Download bereit; wir arbeiten daran, auch die übrigen PDFs zum Download anzubieten, bei denen dies aktuell noch nicht möglich ist. Weitere Informationen hier.
Mit beiden Aboplänen erhältst du vollen Zugang zur Bibliothek und allen Funktionen von Perlego. Die einzigen Unterschiede bestehen im Preis und dem Abozeitraum: Mit dem Jahresabo sparst du auf 12 Monate gerechnet im Vergleich zum Monatsabo rund 30 %.
Wir sind ein Online-Abodienst für Lehrbücher, bei dem du für weniger als den Preis eines einzelnen Buches pro Monat Zugang zu einer ganzen Online-Bibliothek erhältst. Mit über 1 Million Büchern zu über 1.000 verschiedenen Themen haben wir bestimmt alles, was du brauchst! Weitere Informationen hier.
Achte auf das Symbol zum Vorlesen in deinem nächsten Buch, um zu sehen, ob du es dir auch anhören kannst. Bei diesem Tool wird dir Text laut vorgelesen, wobei der Text beim Vorlesen auch grafisch hervorgehoben wird. Du kannst das Vorlesen jederzeit anhalten, beschleunigen und verlangsamen. Weitere Informationen hier.
Ja, du hast Zugang zu Stahltragwerke im Industriebau von Hartmut Pasternak, Hans-Ullrich Hoch, Dieter Füg im PDF- und/oder ePub-Format sowie zu anderen beliebten Büchern aus Technology & Engineering & Civil Engineering. Aus unserem Katalog stehen dir über 1 Million Bücher zur Verfügung.
Information
1
Entwicklung der Eisen- und Stahlbauweise
1.1 Eisen-und Stahlbauweise – ein historischer Abriss
Stein und Holz waren in der Antike und im Mittelalter die bevorzugten Baumaterialien. Die industrielle Revolution wirkte hauptsächlich ab Mitte des 19. Jahrhunderts als Triebkraft für die Anwendung von Eisen bzw. Stahl im Bauwesen. Eisen war der Menschheit in Form des Meteoriteneisens seit etwa 6000 Jahren bekannt. Eisen kommt in der Natur nicht in reiner Form vor, sondern nur in Verbindung mit anderen Elementen, insbesondere mit Sauerstoff als Eisenoxid. Die Eisengewinnung aus Eisenerzen und damit die Anwendung dieses Materials erfolgt seit etwa 3000 Jahren und ist durch Funde aus jener Zeit belegt (Lanzenspitzen, Beile u. Ä.).
Eisenerze sind mit Gestein vermischte Eisen-Sauerstoff-Verbindungen und kommen hauptsächlich als Brauneisenstein, Magneteisenstein, Roteisenstein und Spateisenstein vor. Die Eisenerze werden zunächst gebrochen, gemahlen bzw. gesiebt und vom Gestein getrennt (Erzaufbereitung). Durch Schmelzen wird dann Roheisen gewonnen.
Ursprünglich wurde das Eisen in Gruben oder niedrigen Schachtöfen aus Lehm und Bruchstein bzw. Findlingen aus dem Eisenerz mit Holzkohle und bei Naturluftzug erschmolzen. Im späten Mittelalter entstand daraus der Stückofen für die Eisenverhüttung, der bereits mit einem Blasebalg (später mit Wasserkraft) betrieben wurde. Das Produkt war ein schlackendurchsetzter teigiger Klumpen schmiedbaren Eisens (Luppe). Es stand aber nur in kleinen Mengen für Werkzeuge und Waffen zur Verfügung, spielte im Bauwesen also noch keine Rolle.
Ein bedeutender Schritt gelang um das Jahr 1400. Das Roheisen wurde im Hochofen gewonnen, durch die bessere Ausnutzung der Wärme erstmals nicht als teigiger Klumpen (Luppe), sondern im flüssigen Zustand. Seit jener Zeit erlangte der Eisenguss in Europa große Bedeutung (Kugelguss, Röhren, Glocken, Öfen- und Kaminplatten, Roste, Gewichte). Bereits im Mittelalter erkannte man die Vorzüge dieses neuen Baustoffs auch im Bauwesen.
Für Dachtragwerke waren gemauerte Bogenkonstruktionen typisch. Zur Aufnahme der Horizontalkräfte dienten häufig eiserne Zugbänder. Ein typisches Beispiel aus dieser Zeit sind die um das Jahr 1218 erstmals fertiggestellten und in der heutigen Form seit dem Jahr 1420 erhaltenen Markthallen im Palazzo della Ragione in Padua (Bild 1.1). Michelangelo umspannte die im Jahr 1590 fertiggestellte Kuppel des Petersdoms in Rom mit zwei geschmiedeten Eisenringen. 150 Jahre später hatte die Kuppel große Risse und drohte auseinanderzubrechen. Zur Aufnahme der Zugkräfte wurden fünf weitere Eisenketten (Zugringe) um die Kuppel gelegt, siehe dazu [1.2] und [1.19].
Bild 1.1 Eiserne Zugbänder in der Markthalle von Padua
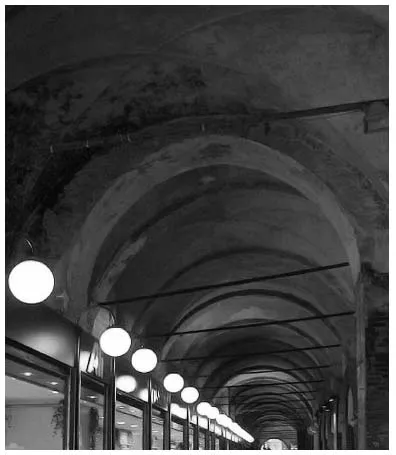
Das flüssige Roheisen hat einen Kohlenstoffgehalt von ca. 2 bis 5%, schmilzt bei relativ niedriger Temperatur, ist jedoch nicht schmied- und schweißbar und kommt in zwei Sorten vor: als weißes Roheisen (Kohlenstoff chemisch gebunden) und als graues Roheisen (Kohlenstoff teilweise frei). Graues Roheisen wird durch mehrmaliges Umschmelzen gereinigt und ergibt Gusseisen. Bestens geeignet war das Gusseisen für die Herstellung von Druckgliedern. Gussstützen konnten wesentlich schlanker sein als herkömmlich gemauerte Pfeiler (Bild 1.2). Wegen der leichteren Formbarkeit ließen sich vielfältige Querschnittsformen und Oberflächen gestalten. Durch das Angießen von Kapitellen im oberen und von Füßen im unteren Bereich erfolgte eine gute Lastein- und -weiterleitung. Gusseisen kann bei Stößen und Erschütterungen leicht brechen (spröde), und die Gestaltung von Trägeranschlüssen war schwierig.
Die Verwendung von Gusseisen für Stützen war am Ende des 19. Jahrhunderts allerdings nur noch dann zu rechtfertigen, wenn Querschnitte und Formen gefordert waren, die mit Schmiedeeisen nicht realisiert werden konnten. Man ging häufig dazu über, schmiedeeiserne Stützen einzusetzen, bei denen nur noch Kopf und Fuß aus Gusseisen hergestellt wurden.
Die Möglichkeiten der industriellen Fertigung von Glas im 19. Jahrhundert führte zu einer Kombination mit dem Baustoff Eisen. Das imposanteste Bauwerk dieser Zeit war der Kristallpalast von London (Bild 1.3), gebaut von Joseph Paxton für die Weltausstellung im Jahr 1851. Dieses riesige Gebäude bestand aus einer 563 m langen und 124 m breiten abgestuften rechteckigen Haupthalle, die von einem hohen gewölbten Querschiff (Tonnengewölbe) zweigeteilt war. Die vertikalen Tragwerkselemente waren hohle, runde Gusseisenstützen mit einer Länge von 14,5 Fuß (4,4 m) bis 20 Fuß (6 m), der Außendurchmesser betrug bei allen Stützen 8 Zoll (20 cm), je nach Belastung variierte die Wandstärke. Die horizontalen Tragwerkselemente waren in Gusseisen bzw. in Schmiedeeisen ausgeführte Fachwerkträger. Die Gebäudehülle bestand vollständig aus Glas. Insgesamt wurden 83.200 m2 Glas für die Außenwände und die Dacheindeckung, 3.500 t Gusseisen und 530 t Schmiedeeisen verbaut. Nähere Angaben zum Bauwerk sind in [1.14] und [1.15] zusammengestellt. Nach der Weltausstellung erfolgte die Demontage des Gebäudes und ein Wiederaufbau an anderer Stelle. Das Bauwerk wurde im Jahr 1936 durch einen Brand vollkommen zerstört.
Die Umwandlung des weißen Roheisens in Stahl besteht im Wesentlichen darin, dass der hohe Kohlenstoffgehalt des flüssigen Roheisens durch Bindung an Sauerstoff gesenkt wird, gleichzeitig werden dabei unerwünschte Gehalte der Eisenbegleiter (Phosphor, Schwefel, Stickstoff, Mangan, Silizium) vermindert. Dieser Vorgang wird als Frischen bezeichnet und war im Mittelalter und bis in das 18. Jahrhunderts hinein technisch nicht durchführbar. Der erste Koksofen in Deutschland – man verwendete Steinkohle und Koks als Brennstoff – wurde im Jahr 1796 in Gleiwitz angeblasen. Größere Mengen an Roheisen konnten jetzt zwar gewonnen, aber noch nicht in gleichem Maße durch Frischen in Stahl umgewandelt werden. Es sollte noch fast weitere 50 Jahre dauern, bis dies umfassend gelang. Eine der Schwierigkeiten bei der Stahlerzeugung lag nämlich darin, dass der Stahl nicht mit Steinkohle oder Koks in Berührung kommen durfte, da er dann Schwefel aufnahm und warmbrüchig wurde.
Mit der Einführung des Puddelverfahrens im Jahr 1784 durch Henry Cort (1824 in Deutschland erstmals angewandt) ließen sich diese Nachteile vermeiden. Bei diesem Verfahren wird der Kohlenstoff des flüssigen Roheisens bei ständigem Durchrühren (Puddeln) durch die Flammgase einer Ofenfeuerung oxidiert. Die erreichte Temperatur reichte nicht aus, das Roheisen flüssig zu halten. Die entstehende teigige Masse teilte man in einzelne Luppen, die der weiteren Oxidation ausgesetzt wurden. Durch Ausschmieden ließ sich die Luppe von Schlacke befreien. Letztendlich wurden die Luppen unter dem Hammer noch in teigigem Zustand zum sogenannten Puddelstahl „zusammengeschweißt“. Das auf diese Weise hergestellte Eisen gab es in Abhängigkeit vom Kohlenstoffgehalt als Schweißeisen bzw. Schweißstahl [1.5]. Dieser Stahl ist nicht schweißbar, aber schmied- und walzbar. Die Anwendung des Puddelverfahrens konnte den steigenden Bedarf an Stahl jedoch nicht befriedigen (Leistung 4,5 Tonnen pro Tag). Im Jahr 1855 gelang es dem Engländer Henry Bessemer auf einfachere Weise Stahl herzustellen (Bessemer-Verfahren). Die Umwandlung des Roheisens in Stahl erfolgte in einem mit kieselsäurehaltigen feuerfesten Steinen ausgekleideten kippbaren Gefäß (Konverter oder Bessemer-Birne), in welches das Roheisen flüssig eingefüllt wurde. Der auf diese Weise erzeugte Stahl erhielt deshalb die Bezeichnung Flusseisen bzw. Flussstahl. Das Bessemer-Verfahren wurde im Jahr 1862 von Alfred Krupp in Deutschland eingeführt. Komprimierte Luft wird unter Aufrichten des Konverters durch den Siebboden von unten durch das Roheisenbad hindurchgeblasen, was eine schnelle Oxidation des Kohlenstoffs und der Eisenbegleiter (Si, Mn) bewirkt.
Wegen des sauren Futters im Konverter konnte nur phosphorarmes Roheisen (0,1 % P) verarbeitet werden, da Phosphorsäure nicht vom sauren Futter gebunden werden kann. Diesen Nachteil löste Sidney Thomas im Jahr 1879 durch Ausfütterung des Konverters mit Kalk (Konverter mit basischem Futter werden nach ihm Thomas-Birne genannt), so dass auch phosphorreiches Roheisen (1,9 bis 2,7% Phosphor) verarbeitet werden konnte. Beide Konverter-Verfahren (Bessemer- und Thomas-Verfahren) erzeugen Stahl in schmelzflüssigem Zustand – eben Flussstahl. Im Jahr 1895 wurde der erste Flussstahl in Deutschland nach dem Thomas-Verfahren erzeugt. In [1.3] ist eine Übersicht der chemischen Zusammensetzung von historischen Stählen angegeben (siehe Tabelle 1.1).
Beim Thomas-Verfahren verbrennt von allen Nebenbestandteilen Phosphor zuletzt, man erhält ein fast entkohltes Eisen, welches aber durch Zugabe von Spiegeleisen „zurückzuholen“ ist. Sowohl beim Bessemer-Verfahren als auch beim Thomas-Verfahren wirkte das Hindurchblasen von komprimierter Luft ungünstig. Der Luftstickstoff steigerte die Sprödbruch- und Alterungsempfindlichkeit dieser Stähle.
Bild 1.2 Beispiele für gusseiserne und schmiedeeiserne Stützen nach [1.4]
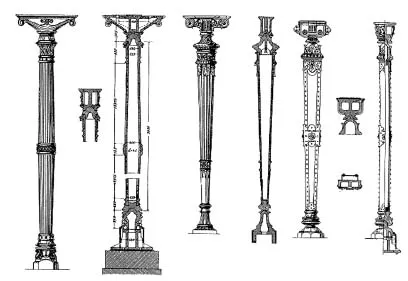
Bild 1.3 Kristallpalast in London, erbaut 1851
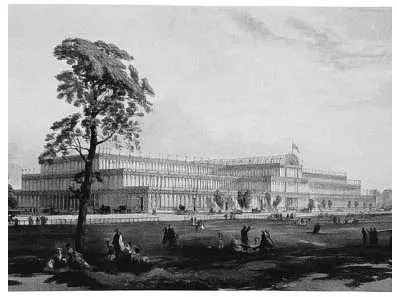
Tabelle 1.1 Übersicht der chemischen Zusammensetzung von Altstahl [1.3]
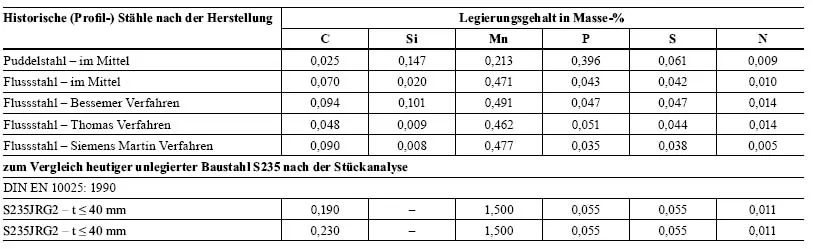
Ein weiteres Verfahren zur Stahlerzeugung war das Flammofenfrischen (Herdfrischen). Diese Ära begann 1864 und wurde nach den Entwicklern Siemens-Martin-Verfahren genannt. Das Verfahren beruhte auf dem Zusammenschmelzen von etwa 15 bis 30 % Roheisen und 85 bis 70 % Schrott in einem Flammofen mit muldenförmigem Herd. Die Oxidation der Eisenbegleiter erfolgte dabei einerseits durch die Frischewirkung der heißen Flamme, die durch die Siemenssche Regenerationsfeuerung erreicht wurde, und andererseits durch den am Schrott anhaftenden Rost bzw. sauerstoffabgebende Zuschläge (z.B. Erz). Die hohen Temperaturen (1.600 °C bis 1.700 °C) wurden durch eine Gasfeuerung erzielt. Dieses Verfahren eignete sich für Roheisen mit wenig oder mäßigem Phosphorgehalt. In Deutschland gingen die ersten Siemens-Martin-Öfen 1868/69 in Essen bei Alfred Krupp und in Berlin in Betrieb.
Ein weiteres Flammofenverfahren ist das Tiegelschmelzverfahren, es besaß allerdings nur eine untergeordnete Bedeutung.
Gegen Ende des 19. Jahrhunderts konnte man also Stahl in brauchbaren Qualitäten und in großen Mengen herstellen. Nach dem Frischeverfahren (Stahlherstellungsverfahren) erhalten die Stähle auch ihre Bezeichnung: Puddelstahl, Thomasstahl, Siemens-Martin-Stahl (früher) bzw. Elektrostahl und Oxygenstahl (heute). Eine umfassende Zusammenstellung zur Entwicklung alter Stähle und Bauweisen mit vielen weiterführenden Literaturhinweisen ist in [1.24] angegeben.
Bei den Eisenkonstruktionen des Hochbaus kamen als Verbindungsmittel nur Niete, Schrauben und Bolzen in Betracht. Insbesondere etablierte sich die Niettechnik. Das Zusammenschweißen von tragenden Bauteilen war aufgrund unzureichender bzw. unzuverlässiger Festigkeit der Schweißstelle verboten. Der Eiffelturm stellt ohne Zweifel einen Höhepunkt des Stahlfachwerkbaus und der Nietkonstruktionen dar. Dieses Stahltragwerk, heute das Wahrzeichen der französischen Hauptstadt, wurde 1889 anlässlich der Pariser Weltausstellung aus über 7.000 Tonnen Eisen (im Puddelverfahren hergestellt) errichtet und war mit seinen 300 m Höhe lange das höchste Bauwerk der Welt. Der mit Hilfe eines Kletterkrans gebaute Turm wurde in nur zwei Jahren errichtet. 15.000 Stahlteile wurden mit ca. 2,5 Millionen Nieten verbunden. Die Bilder 1.4 a) bis c) zeigen das Bauwerk heute und während der Bauphase.
Bild 1.4 Der Eiffelturm heute, am 27. April 1888 und im Juli 1888

Gleichzeitig gab es bereits eine gewisse Produktvielfalt an Walzstählen (Bleche und Flacheisen, Quadrat- und Rundeisen, Profileisen). Vom Verband Deutscher Architekten- und Ingenieurvereine, dem Verein Deutscher Ingenieure und dem Technischen Verein für Eisenhüttenwesen wurden seit dem Jahr 1880 die ,,Deutschen Normalprofile“ aufgestellt [1.1]. Daraus ergaben sich ungeahnte Möglichkeiten im Hoch- und Brückenbau. Heute sprechen wir vom Stahlbau bzw. von Stahltragwerken, bis 1928 hieß es Eisenbau bzw. Eisenkonstruktionen.
1906 hatte der Deutsche Verband für Materialprüfung in der amtlichen Kennzeichnung Flussstahl für Eisenwerkstoffe mit mindestens 420 N/mm2 Zugfestigkeit und Fluss- und Schweißeisen mit geringeren Festigkeiten festgelegt.
1925 fällte die Obmännerversammlung des Werkstoffausschusses einen Beschluss, nach dem „alles ohne Nachbehandlung schmiedbare Eisen als Stahl bezeichnet werden soll, dass aber gleichzeitig die handelsüblichen Bezeichnungen Formeisen, Stabeisen usw. beibehalten werden“ [1.16].
Mit den „Bestimmungen des preußischen Ministers für Volkswohlfahrt für den Eisenhochbau vom 25.02.1925“ wurde der hochwertige Baustahl St 48 eingeführt. Zwischen den Jahren 1926 und 1937 entwickelten die Stahlerzeuger insbesondere auf Wunsch de...
Inhaltsverzeichnis
- Cover
- Title Page
- Copyright
- Vorwort
- 1: Entwicklung der Eisen- und Stahlbauweise
- 2: Bauteile des Stahlhochbaus
- 3: Hallen und Überdachungen
- 4: Kranbahnen
- 5: Mehrgeschossige Bauwerke
- 6: Tragwerke von Industriebrücken (Rohrleitungs- und Bandbrücken)
- 7: Industrieschornsteine, Maste, Windenergieanlagen
- 8: Behälter, Bunker, Silos