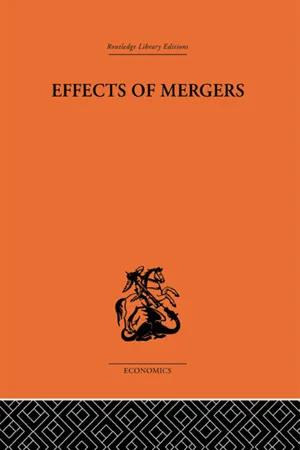
eBook - ePub
Effects of Mergers
Ruth Cohen,P. Lesley Cook
This is a test
- 460 Seiten
- English
- ePUB (handyfreundlich)
- Ăber iOS und Android verfĂŒgbar
eBook - ePub
Effects of Mergers
Ruth Cohen,P. Lesley Cook
Angaben zum Buch
Buchvorschau
Inhaltsverzeichnis
Quellenangaben
Ăber dieses Buch
Effects of Mergers charts the history of six industries with a view to examining the effects of mergers. It deals both with the short and long-term effects of changes in the structure of industry and looks at issues such as whether mergers are in the public interest.The industries covered are: Cement, Textile Printing, Soap, Glass, Motor and Brewing.Some comparative material with industries in the USA is included.
HĂ€ufig gestellte Fragen
Wie kann ich mein Abo kĂŒndigen?
Gehe einfach zum Kontobereich in den Einstellungen und klicke auf âAbo kĂŒndigenâ â ganz einfach. Nachdem du gekĂŒndigt hast, bleibt deine Mitgliedschaft fĂŒr den verbleibenden Abozeitraum, den du bereits bezahlt hast, aktiv. Mehr Informationen hier.
(Wie) Kann ich BĂŒcher herunterladen?
Derzeit stehen all unsere auf MobilgerĂ€te reagierenden ePub-BĂŒcher zum Download ĂŒber die App zur VerfĂŒgung. Die meisten unserer PDFs stehen ebenfalls zum Download bereit; wir arbeiten daran, auch die ĂŒbrigen PDFs zum Download anzubieten, bei denen dies aktuell noch nicht möglich ist. Weitere Informationen hier.
Welcher Unterschied besteht bei den Preisen zwischen den AboplÀnen?
Mit beiden AboplÀnen erhÀltst du vollen Zugang zur Bibliothek und allen Funktionen von Perlego. Die einzigen Unterschiede bestehen im Preis und dem Abozeitraum: Mit dem Jahresabo sparst du auf 12 Monate gerechnet im Vergleich zum Monatsabo rund 30 %.
Was ist Perlego?
Wir sind ein Online-Abodienst fĂŒr LehrbĂŒcher, bei dem du fĂŒr weniger als den Preis eines einzelnen Buches pro Monat Zugang zu einer ganzen Online-Bibliothek erhĂ€ltst. Mit ĂŒber 1 Million BĂŒchern zu ĂŒber 1.000 verschiedenen Themen haben wir bestimmt alles, was du brauchst! Weitere Informationen hier.
UnterstĂŒtzt Perlego Text-zu-Sprache?
Achte auf das Symbol zum Vorlesen in deinem nÀchsten Buch, um zu sehen, ob du es dir auch anhören kannst. Bei diesem Tool wird dir Text laut vorgelesen, wobei der Text beim Vorlesen auch grafisch hervorgehoben wird. Du kannst das Vorlesen jederzeit anhalten, beschleunigen und verlangsamen. Weitere Informationen hier.
Ist Effects of Mergers als Online-PDF/ePub verfĂŒgbar?
Ja, du hast Zugang zu Effects of Mergers von Ruth Cohen,P. Lesley Cook im PDF- und/oder ePub-Format sowie zu anderen beliebten BĂŒchern aus Business & Business generale. Aus unserem Katalog stehen dir ĂŒber 1Â Million BĂŒcher zur VerfĂŒgung.
Information
CHAPTER 1
Introduction
THE Cement industry is particularly suitable for the study of the relationships between the characteristics of an industry and its structure and organization. The product, if it has not always been homogeneous, can be closely defined, and it is sufficiently homogeneous for measurement by weight to be reliable. The number of firms in the industry has never been very great and relatively few have many outside interests; thus they can both be discussed individually, and grouped meaningfully in ways which make it possible to substantiate generalizations.
Mergers have played a very large part in determining the structure of the industry and the types of competition in it. Unlike the brewing industry, mergers in the cement industry have been rather few in number, but the majority have been of major importance. The four great amalgamations divide the industry into covenient periods for study.
There is first the period up to the formation of Associated Portland Cement Manufacturers Ltd in 1900, this followed by the period between 1900 and 1911 when British Portland Cement Manufacturers Ltd was formed. The third period, 1919â34, covers the time during which the Red Triangle group was formed and then amalgamated with the Associated Portland Cement Manufacturers Ltd; this is followed by the formation of the Alpha group and its amalgamation with APCM and Tunnel in 1938.
The structural development of the industry took place against a background of relatively rapid technical change. This, together with the repercussions due to the changing structure of the industry, which was itself partly due to the technical change, has meant that during the last hundred years the cement industry has rarely been even approximately stable. Change has been more or less continuous and any study of the industry must take full account of the dynamic characteristics; this inevitably complicates the problem of reaching conclusions because it substantially reduces the value of comparisons between situations before and after particular mergers.
EARLY HISTORY OF PORTLAND CEMENT
Joseph Aspdin patented Portland Cement in 1824, but claimed to have been making it since 1811. This new product was an improvement upon the Roman Cement and Medina Cement, both of which were in general use. Aspdinâs specifications on the Patent were, however, insufficiently detailed to enable others to use his methods. Further, it is far from clear that he knew exactly what was required. He made no mention of the need to burn the raw materials to the point of incipient fusion, yet it was this feature which was only rediscovered with difficulty by I. C. Johnson in 1847. Aspdin and his son had continued to manufacture Portland cement, but having little chemical or scientific knowledge, they used rule of thumb rather than scientific methods and did not know what were the really important aspects of their process. Further, their methods of manufacture were a very well-guarded secret.
Portland Cement really came to public notice in the late 1840âs, and there was public rivalry between Frostâs3 and Aspdinâs (William Aspdin and the son of Joseph Aspdin the patentee). There were repeated failures of the Roman Cement which was being extensively used at that time, and tests showed the superiority of Portland Cement. âIn 1850, there were still only four factories where Portland Cement was produced.â4 Its development was being hindered by the irregularity (in quality) of the output and the competition from Roman Cement.
âAfter 1851 the number of works on the Medway and Thames increased rapidly and met with more or less success although Whiteâs Brandâmade by J. Bazley White & Co. at Frostâs works at Swanscombe by I. C. Johnson continued to occupy a prominent position.â5
âSome measure of the stage of development in the methods of making hydraulic lime and cement can be seen from the fact that in 1852 Portland Cement did not even reach the strength which is obtainable from the ground hydraulic lime of todayâ (1924).6
THE MANUFACTURE OF PORTLAND CEMENT
As in most industries, events in the Portland Cement industry have been to a large extent determined by its technical characteristics and the rate of change in methods of manufacture. A very brief outline of the manufacture of Portland Cement and the changes which took place prior to 1914 is thus necessary. The processes can be considered under four heads:
1. Selection of raw materials and quarrying;
2. Mixing and grinding of raw materials;
3. Burning;
4. Grinding of the âclinkerâ which is the product of the kiln in which the burning is done.
In the early years there was little knowledge of the scientific reasons for procedures, rule of thumb methods prevailed, and the production of good reliable cement was more important than cost. The chief difficulties lay in the selection of the raw material and in the methods of burning.
The availability of raw material has always been of prime importance to a cement works and the location of the industry and heavy transport costs play a large part in determining the nature of competition. Before 1900 the industry was highly localized on the Thames and Medway, although there were works in Sussex, Cambridgeshire and South Wales and others, mainly fairly small ones, wherever the raw material was available.
Increased scientific knowledge of the exact mixture of raw materials required, combined with improved techniques for grinding the raw material, made manufacture away from the London area more possible; in particular, limestone as well as chalk could be used. Some of these raw materials gave rise to high manufacturing costs but these were offset by the reduced transport cost to the local market.
As quality improved, costs, which had varied considerably between works, became more important. In the mixing and grinding and in the burning there was very great scope for economy; improved methods resulted in substantial saving in labour and fuel. The radical change in the methods of mixing the raw materials was the introduction of wet grinding, which was patented in 1870 by Goreham. Refinements and improvements in layout continued, but there was no further basic change. The drying of slurry7 became, after that, more closely related to the problem of the type of kiln, for in most cases the slurry came to be dried with heat from the kiln.
The kiln has always been regarded as the central feature of a cement works. This is due partly to the fact that it is the largest single item of capital equipment, but also to the fact that kiln capacity has a definite upper limit whereas in other sections there is normally some spare capacity. Further, if maximum output is maintained, there has always been some fuel economy, although of course this has only been of extreme importance since the introduction of the large rotary kiln.
In 1878 an article on the manufacture of cement accepts the bottle kiln as normal equipment.8 Davis says, however, that in retrospect the last quarter of the nineteenth century is regarded as the âchamberâ kiln era.9
The chamber kiln was a more or less natural development of the bottle or dome kiln. The obvious weakness of the latter was that it required to be fed with a dry or nearly dry raw material; the drying required special plant and involved additional manhandling, which caused extra expense. It was, therefore, early realized that a kiln which could combine both drying and calcining (burning) would be a distinct advance on the bottle kiln. âJohnsonâs chamber kiln was patented in 1872 and comprised a long horizontal chamber set at right angles to the vertical axis of a bottle kiln, the open dome of the latter being closed in so that the product of combustion and waste heat from the kiln had to pass through a chamber before they could reach the chimney which was attached.â10 In the chambers the slurry (wet mixture of clay and chalk) was dried. The Batchelor kiln was an improved chamber kiln providing two or even three chambers, one above the other, thus avoiding very long chambers.
The chamber kiln was developed to a high standard of efficiency and such kilns were still being installed as late as 1903. New types were, however, making them obsolete. The first rotary kiln patent was taken out in 1877 by Crampton, but the credit usually goes to Ransome and Stokes who took out patents in 1885 and 1888 respectively.11
The first rotary was put in at Arlesley in 1887 and then two others were installed, one at Grays on the Thames and the other at Penarth in South Wales. All were commercial failures. The reasons for the failure were first, the difficulty of obtaining a satisfactory lining; second, the difficulty of maintaining the requisite temperature inside the kiln; third, the frequent formation of large masses of fused or semi-fused clinker in the interior of the burning cylinder which prevented the passage of further supplies of raw material; fourth, the inefficient use of fuel due to the shortness of the cylinder; fifth, the unduly high lime content which was due to the fact that the absence of ash in the fuel employed (producer gas) was not allowed for in the preparation of the raw material; and lastly, the inconvenient quick setting nature of the cement produced.
The list of reasons for failure is helpful. It shows rather clearly that the industry was undeveloped in engineering and scientific knowledge and still lacked real knowledge of the chemistry of cement. Although it is fully recognized that the industry had in general an empirical approach, the failure of the rotary kiln at this date shows that this extended to the most progressive. This industry was among the many, which includes the glass industry, which were hampered by lack of satisfactory refractory materials; any development of refractory materials appears to be an innovation of very wide application.
âThe credit for that practical development of the rotary kiln must unreservedly be given to the United States.â Hurry and Seaman took out their major patent in 1896 and others in the years immediately after. âThe practical development of the rotary kiln in Great Britain dates from the year 1900 when the recently-formed company The Associated Portland Cement Manufacturers purchased certain rights from Messrs. Hurry and Seaman and proceeded to build a number of rotary kilns on the Thames.â12 Other competitive cement manufacturers outside this Company also obtained information from the United States without the purchase of any rights and the year 1900 saw one or two other rotary kilns in course of construction at various places in the country.
A third type of kilnâthe shaft kilnâmust also be mentioned as it has played a considerable part in determining the nature of competition in the industry, since it was relatively cheap to install. The shaft kiln, of which the Schneider was the most important type in this country, was mainly developed on the continent. The Schneider type does not appear to have been introduced into this country until about 1898.13 The shaft kiln is a vertical kiln which is fed with raw material and fuel at the top and the clinker when burned is drawn off or taken out by a mechanical grate at the bottom. Thus, like the rotary kiln, it operated continuously and this gave, according to Davis,14 a saving of some 50 per cent in fuel. The disadvantage of the shaft kiln in this country is due to the fact that the raw material must be dry or nearly dry in the form of bricks or lumps, and thus it is necessary either to use a âdryâ process for mixing or to have some means of drying the wet slurry. âDryâ mixing processes depend upon a supply of suitable raw material and upon heavy grinding machinery and even so the mixing is frequently less efficient than that obtained by the wet method.
The early shaft kilns were fed by hand and the clinker removed by hand; this, together with the drying of the slurry, involved high labour costs. However, many improvements to the kiln were made and Davis reported that âThis kiln (the Schneider) has attracted some attention and is installed at three or four factories.â15 Around 1907 great further improvements were made. Output was increased by the use of forced draughts; mechanical feeds and grates were introduced, and the Schneider kiln became more common. The really important point is that this kiln was very considerably cheaper than the rotary kiln. Its production was about ninety tons a week. The relatively small capital outlay meant that a satisfactory continuous kiln was available to small producers and thus undoubtedly had a great effect in increasing competition in the industry during this period of rapid technical development. Although the kiln was âsatisfactoryâ some idea of the state of development of the industry in 1907 may be obtained from the following quotation from Davisâ Portland Cement (1907).
âIn whatever class of fixed kiln (as opposed to rotary) it is produced, the clinker is, however, somewhat irregular in quality and contains a good deal of imperfectly-burnt material and unless this is picked out with great care, sufficient underburnt material remains to impair the quality of the finished cement to a serious degree.â16
In the grinding of clinker, which is an important factor in determining quality, the chief development was the replacement of the mill stones by ball mills and tube or âGriffinâ mills.17
Writing in 1924 in Portland Cement 1824â1924, Davis describes the economy in labour which was being achieved.
âTo one familiar with the older type works nothing is more striking than the appearance of a modern works in which full advantage has been taken of mechanical means of transport. Throughout the works there are signs of great activity and yet an almost complete absence of men. At the crushers for raw materials there will be a few; about the fine-grinding plant one or two hands sauntering about with oilcans; on the platform in front of the rotary kiln a burner, perhaps one to each pair of kilns . . . The whole process of manufacture has been brought very nearly to that ideal state of industry where man is put in his proper place as supervisor and is not used as a sentient machine.â18
Thus, during the thirty years 1895 to 1925 the cement industry had changed radically. Almost all the capital equipment had changed fundamentally at least once, and in addition, whereas âthe manufacture of cement was carried on as as an empirical trade, at the present time (1924) it is organized as one of the largest chemical industries and, as all chemical industries must be, is directed by the chemist and the engineerâ.19
The great changes resulted in substantial cost reductions. The cost at the works by the pre-1900 methods was about 18s. per ton under ordinarily favourable conditions. By the modern method, and under similar conditions, the cost up to the World War I was about 13s. per ton. These figures are taken as representing fairly enough the difference in cost of the two processes. The reductions in cost were accompanied by increases in the average size of works. Davis speaks of a typical works of fair size pre-1900 as producing about 500 tons a week (i.e. 25,000 tons a year). By 1924 a typical works of fair size produced between 50,000 to 100,000 tons a year.
It is ag...
Inhaltsverzeichnis
- Cover
- Title page
- Copyright page
- Contents
- PREFACE
- GENERAL INTRODUCTION
- I THE CEMENT INDUSTRY: P. Lesley Cook
- 1. Introduction
- 2. The Period Before 1900, and the Formation of the Associated Portland Cement Manufacturers Ltd
- 3. The Immediate Effects of the Formation of the APCM, 1900â7
- 4. Price Agreements, 1900â10
- 5. The Second Combine, 1911
- 6. 1918â29
- 7. 1929â34
- 8. Price Stability, 1934â9
- 9. 1939â55
- 10. Conclusions
- APPENDIX
- II THE CALICO PRINTING INDUSTRY: P. Lesley Cook
- 1. Introduction
- 2. Before the Merger, 1850â1900
- 3. The Formation of the Calico Printersâ Association Ltd
- 4. The Early Years of the Association, 1900â2
- 5. 1902â14
- 6. The Declining Industry, 1918â39
- 7 .1945â54
- 8. The Role of the Combine,
- APPENDIX Fixed and variable costs
- IIITHE SOAP INDUSTRY: Ruth Cohen
- 1. Introduction
- 2. Expansion Without Acquisitions, 1885â1906
- 3. The Abortive Combine, 1906
- 4. The Period of Acquisitions, 1906â21
- 5. The Period of Consolidation and Rationalization 1921onwards
- 6. Conclusions
- APPENDIX Number of Soap Producers in Great Britain at Selected Dates
- IV THE FLAT-GLASS INDUSTRY: P. Lesley Cook
- 1. Introduction
- 2. The Establishment of the Modern Industry
- 3. 1910â14
- 4. The Industry Since 1918
- 5. The Subsidiary Activities of Pilkington Brothers
- 6. Conclusions
- V THE MOTOR INDUSTRY: George Maxcy
- 1. Introduction
- 2. The Early Experimental Years, 1896â1901
- 3. The Period of Small-scale Competition, 1902â22
- 4. The Beginning of Mass Production, 1923â9
- 5. Price and Model Competition, 1930â9
- 6. Post-war Expansion, 1945â55
- 7. A Comparison with the USA
- 8. Conclusions
- VI THE BREWING INDUSTRY: John Vaizey
- 1. Introduction
- 2. The First Period of Mergers, 1886â1901
- 3. Mergers in a Depressed Period, 1900â14
- 4. Continuous Concentration
- 5. Conclusions
- GENERAL CONCLUSIONS
- INDEX
Zitierstile fĂŒr Effects of Mergers
APA 6 Citation
Cohen, R., & Cook, L. (2013). Effects of Mergers (1st ed.). Taylor and Francis. Retrieved from https://www.perlego.com/book/1679803/effects-of-mergers-pdf (Original work published 2013)
Chicago Citation
Cohen, Ruth, and Lesley Cook. (2013) 2013. Effects of Mergers. 1st ed. Taylor and Francis. https://www.perlego.com/book/1679803/effects-of-mergers-pdf.
Harvard Citation
Cohen, R. and Cook, L. (2013) Effects of Mergers. 1st edn. Taylor and Francis. Available at: https://www.perlego.com/book/1679803/effects-of-mergers-pdf (Accessed: 14 October 2022).
MLA 7 Citation
Cohen, Ruth, and Lesley Cook. Effects of Mergers. 1st ed. Taylor and Francis, 2013. Web. 14 Oct. 2022.