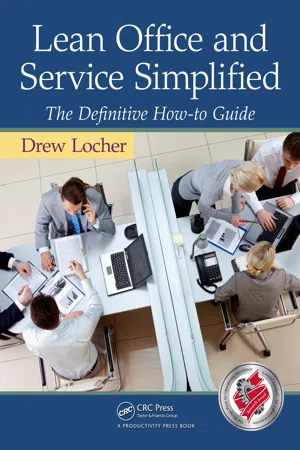
eBook - ePub
Lean Office and Service Simplified
The Definitive How-To Guide
Drew Locher
This is a test
- 194 páginas
- English
- ePUB (apto para móviles)
- Disponible en iOS y Android
eBook - ePub
Lean Office and Service Simplified
The Definitive How-To Guide
Drew Locher
Detalles del libro
Vista previa del libro
Índice
Citas
Información del libro
Winner of a 2012 Shingo Research and Professional Publication AwardDemystifying the application of Lean methods, Lean Office and Service Simplified: The Definitive How-To Guide goes beyond the basic tools to detail the key concepts of Lean as they apply to office and service environments. It begins by discussing value stream management, followed by
Preguntas frecuentes
¿Cómo cancelo mi suscripción?
¿Cómo descargo los libros?
Por el momento, todos nuestros libros ePub adaptables a dispositivos móviles se pueden descargar a través de la aplicación. La mayor parte de nuestros PDF también se puede descargar y ya estamos trabajando para que el resto también sea descargable. Obtén más información aquí.
¿En qué se diferencian los planes de precios?
Ambos planes te permiten acceder por completo a la biblioteca y a todas las funciones de Perlego. Las únicas diferencias son el precio y el período de suscripción: con el plan anual ahorrarás en torno a un 30 % en comparación con 12 meses de un plan mensual.
¿Qué es Perlego?
Somos un servicio de suscripción de libros de texto en línea que te permite acceder a toda una biblioteca en línea por menos de lo que cuesta un libro al mes. Con más de un millón de libros sobre más de 1000 categorías, ¡tenemos todo lo que necesitas! Obtén más información aquí.
¿Perlego ofrece la función de texto a voz?
Busca el símbolo de lectura en voz alta en tu próximo libro para ver si puedes escucharlo. La herramienta de lectura en voz alta lee el texto en voz alta por ti, resaltando el texto a medida que se lee. Puedes pausarla, acelerarla y ralentizarla. Obtén más información aquí.
¿Es Lean Office and Service Simplified un PDF/ePUB en línea?
Sí, puedes acceder a Lean Office and Service Simplified de Drew Locher en formato PDF o ePUB, así como a otros libros populares de Negocios y empresa y Operaciones. Tenemos más de un millón de libros disponibles en nuestro catálogo para que explores.
Información
Chapter 1
Organizing by Value Stream
In this chapter, we will look at three alternatives for organizing by value stream:



The approach you will need to use will depend on the complexity of the overall process, the number of people involved, and the level of knowledge and skill required to perform these necessary activities, among other considerations. But first, some background.
The Lean Lexicon (Lean Enterprise Institute, Fourth Edition, March 2008) defines a value stream as “the set of all actions, both value-creating and nonvalue creating, required to bring a product (or service) from concept to launch (also known as the development value stream), and from order to delivery (also know as the operational value stream). These include actions to process information from the customer and actions to transform the product (or service) on its way to the customer.”
There are also a number of information processes that businesses perform to support these two primary value streams. These “secondary” information processes often do not create value for the external customer, but are necessary to run the business. For example, accounting activities in a manufacturing company are performed in support of the primary operational value stream (and purpose) of the business: to make and deliver product. However, for an accounting firm that is providing accounting services to another company, it is its primary operational value stream.
One of the most formidable obstacles to applying Lean Thinking to office and service processes is the existing organizational structure. Most companies are organized by functions or departments that have little relationship to the information actually being processed or the service being delivered. In most cases, these functional structures impede the flow of information. They can result in parochialism, where managers may be responsible for portions of the information or service flow, but where nobody is responsible for the management and continuous improvement of the overall process. More specifically, they tend to add to the number of hand-offs and often give rise to conflicts of priorities between departments. Budgetary practices can further increase the likelihood and effects of these conflicts, as “turf battles” occur between departments as they compete for limited resources and funds.
We have seen this in manufacturing for years, where functional organizations existed with separate machining, assembly, quality assurance, packaging, and shipping departments. This approach was thought to optimize individual functions’ performance, though this often came at the expense of overall process or system performance. Although many manufacturing organizations have realized that they must change the fundamental ways in which they are organized to realize breakthrough results in improved material and product flow, office and service environments are just starting to come to the same conclusion.
In either environment, your objective is the same: to optimize the performance of the overall value stream. In an office or service environment, this means optimizing the performance of each information or service process. You will also need to ensure the ongoing continuous improvement of your business’s primary value streams and secondary processes. You will do this by organizing and managing by value streams, or what some have called “end-to-end” process management. Ideally, instead of having different managers responsible for particular processes within the same value stream, a single person—a Value Stream Manager will have the overall responsibility for a specific value stream’s performance. The point is not to have a Customer Service manager focused on the Order Entry activity and an Accounting manager focusing on the Invoicing activity, and so on. The real objective is to ensure that all the activities in the value stream are being performed in ways that optimize the performance of the overall “end-to-end” process. Consider an organizational structure based on actual information flows: “order-to-cash,” “requisition-to-pay,” “product and process development,” etc. What advantages will your organization realize by having order processing, planning, invoicing, and collection personnel—an “order-to-cash” team—working together as a team rather than as separate departments? What if this team reports to a single value stream manager, with performance metrics based on the overall process? What are the disadvantages of this organizational structure?
What I have just described can be considered an ideal. But organizations do not really need to change their structure and reporting relationships in order to improve the performance of processes or value streams that involve multiple departments. There are other alternatives that can provide meaningful results. In the following sections, we will review the three ways to organize by value stream and the advantages and disadvantages of each. For each method, existing reporting relationships can remain the same and can remain effective. First, let us look at cross-functional teams based on value stream.
Cross-Functional Teams Based on Value Stream
More and more organizations have set up office “cells” or “pods”—cross-functional teams of people, colocated to process information in fractions of time. Office cells can reduce lead time, including queue time, by as much as 90%, and process time, or “touch time,” by as much as 40%. Office “cells” can improve the effectiveness and efficiency of communication and decision making, while reducing quality “defect” or “correction” waste. The number of hand-offs can be reduced, and a greater awareness of the needs of “internal” customers can be achieved. The result is the reduction of non-value-added waste throughout the value stream. In Chapter 3, I will show you how to implement cross-functional teams. For now, a general discussion of the nature of the team structure (which will depend on the information being processed or the services being delivered) and the obstacles to establishing it will suffice.
How about secondary processes that are only performed periodically, such as payroll, month-end closing (closing the financial “books” at the end of each month), generating proposals, and similar processes? Can cross-functional, colocated teams be set up to perform these processes and achieve similar results? Definitely. Consider what most companies do when they are working in a compressed timeframe: they typically identify a cross-functional team to meet the challenge. And often, the team will take on the challenge while physically occupying the same space, a conference or meeting room.

Figure 1.1 Functional versus cell approaches.
If it makes sense to organize ourselves in this way when we are in a hurry, why not organize ourselves this way whenever the opportunity arises? A typical objection is that it is disruptive. But it is only disruptive because we do not typically plan for it. If you organize your work structures to support this approach from the outset, it need not be as disruptive as you might expect. Further, if the task at hand is completed in significantly shorter timeframes and with less, not more effort (remember the typical results in shorter lead and process times), then people can return to their “normal” duties sooner and have more time for them as a result. Sound like a win-win? Take a look at Figure 1.1 to see how you might organize your cell approach. The figure on the left side depicts a traditional approach with separate departments located in different areas of an office or building. The figure on the right side shows a cross-functional team physically located in the same area.
Defining Roles by Value Stream within a Department
We can apply the same concept of organizing by information process at the department level. One breakthrough exercise that can help people begin to see how to apply Lean is to identify “service families.” When you identify service families, you begin to identify the key services delivered by a department or function. You will begin to see the “processes” that are being regularly performed, and realize that they are not adequately organized by service or process.
Let us take a look at Customer Service. Customer service personnel are often involved in multiple activities that fall under the umbrella function of “customer service.” Personnel are expected to determine the best way to organize themselves; in other words, to work in a way that works best for the individual. The result is a very unpredictable, highly variable work environment with little or no standard work throughout.
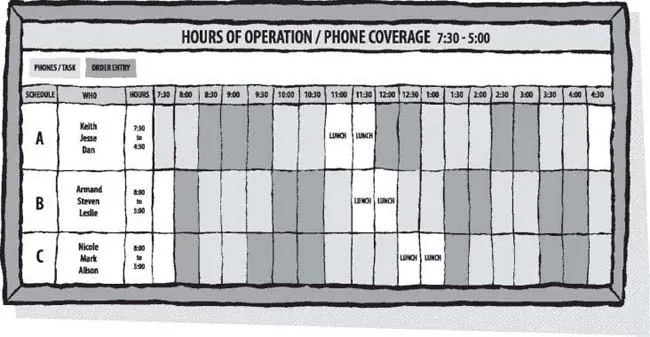
Figure 1.2 Organizing activities for a department by value stream.
An alternative is to organize by service family. There are typically three key services delivered by customer service personnel: order processing, problem solving (e.g., providing technical support, order status, or order maintenance), and value creation (e.g., proactively generating sales). Unfortunately, so much time is spent on the first two that little time is left to create more value for the business. But what if the personnel within the Customer Service department were organized by these three service families? How would this lend itself to greater organization of the activities? How would that impact the effectiveness and efficiency of these activities? Would it reduce variability and help achieve standard work?
When you require that particular people within the customer service department perform particular activities and have separate roles and responsibilities that does not mean that it is all that these people will do forever. Maintaining an enriching work environment is important in a Lean enterprise, and rotation will prevent people from falling into the trap of performing mind-numbing repetitive work over time. I encourage you to rotate people between roles in a way that will minimize disruption in the operation. Let us take a look at how this might work in a Customer Service department (see Figure 1.2).
In this case, two different categories of activities were identified: “Order Management” and “Task Management.” Task Management involved highly variable and unpredictable activities, such as answering inbound phone calls, logging interactions, responding to e-mail, and similar tasks. Order Management activities included entering orders, processing return material authorizations, and the like. These two categories were identified to separate the highly variable activities from the more standard activities. There is no reason to allow standard activities to be negatively impacted by the highly variable ones. Of course, maintaining telephone coverage was vital, so management performed a study of inbound calls and established a schedule for the department accordingly. Customer Service associates were assigned to one of three schedules, each with designated times for Order Management activities and separate times for Task Management activities. This schedule ensured that sufficient capacity existed to answer inbound calls in a timely manner throughout the day. As a result, the department was able to reduce order entry errors and increase throughput. Equally important, the associates felt that the work environment was much more productive and satisfying.
Organizing Activities for Individuals by Value Stream
Even if the same resources are expected to perform multiple tasks, how can we better organize the completion of these tasks? Too often, office personnel are left on their own to decide how and when to perform the multiple tasks expected of them. Unfortunately, what that means is that each person in the office usually organizes him- or herself in different ways. Why is that a problem? First, the timing of the completion of work may not be appropriate. Two, the prioritization of work is likely inconsistent through the value stream. Once again, this contributes to a standard office problem: the unpredictability of the movement of work from one step to the next.
What if a “plan for every process” was developed for all of the key information processes in the office? With a plan for every process, each task will be assigned to specific days of the week and times of the day. Further, the plans for different people (i.e., roles) in the office will be “synchronized” to each other to maximize the flow of information and service. This way, we can guarantee tremendous predictability in the multitasking work environment. Each person will know what to do and when. We can avoid simultaneous processing of different information by the same person, another way to provide significant productivity improvements. It is typically easier for someone to perform one task at a time than attempting to do three things at once. In our Customer Service example, trying to answer the phone while entering an order can give rise to possible errors, as well as increase process time. Can the number of disruptions and interruptions be minimized by developing a “plan for every process”? This is analogous to the “plan for every part” concept applied in manufacturing, in which delivery times and quantities are set for every part used in the manufacturing process. Let us take a look at what a plan for every process might look like (see Figure 1.3).
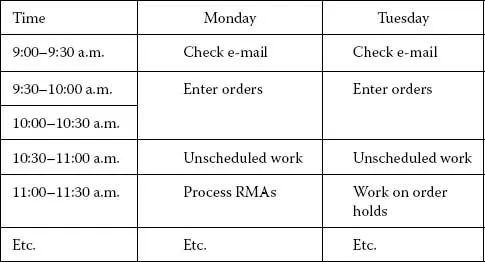
Figure 1.3 An example of a “plan for every process.”
Even time for “unscheduled work” has been put aside. This time can be used for unplanned or “drop-in” work. The details of how this might work will depend on the nature of the individual’s position, among other factors such as the urgency of the unplanned work, and the true response ti...
Índice
- Cover
- Title Page
- Copyright
- Dedication
- Contents
- Introduction
- Endorsements
- Chapter 1 Organizing by Value Stream
- Chapter 2 Creating Standard Work for Office and Service
- Chapter 3 Creating Flow in Office and Services
- Chapter 4 Creating Level Pull in the Office
- Chapter 5 Establishing Visual Management in Office and Services
- Chapter 6 Lean Tools for Office and Services
- Chapter 7 Functional Applications of Lean
- Chapter 8 Leading the Lean Organization
- The Quality Toolbox
- Forms
- Index
Estilos de citas para Lean Office and Service Simplified
APA 6 Citation
Locher, D. (2017). Lean Office and Service Simplified (1st ed.). Taylor and Francis. Retrieved from https://www.perlego.com/book/1517732/lean-office-and-service-simplified-the-definitive-howto-guide-pdf (Original work published 2017)
Chicago Citation
Locher, Drew. (2017) 2017. Lean Office and Service Simplified. 1st ed. Taylor and Francis. https://www.perlego.com/book/1517732/lean-office-and-service-simplified-the-definitive-howto-guide-pdf.
Harvard Citation
Locher, D. (2017) Lean Office and Service Simplified. 1st edn. Taylor and Francis. Available at: https://www.perlego.com/book/1517732/lean-office-and-service-simplified-the-definitive-howto-guide-pdf (Accessed: 14 October 2022).
MLA 7 Citation
Locher, Drew. Lean Office and Service Simplified. 1st ed. Taylor and Francis, 2017. Web. 14 Oct. 2022.