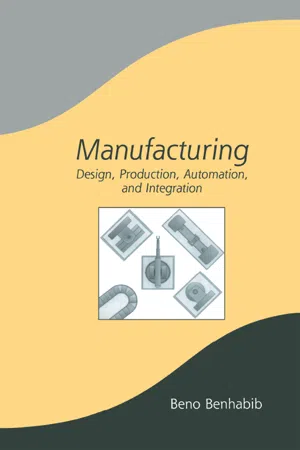
eBook - ePub
Manufacturing
Design, Production, Automation, and Integration
Beno Benhabib
This is a test
- 608 páginas
- English
- ePUB (apto para móviles)
- Disponible en iOS y Android
eBook - ePub
Manufacturing
Design, Production, Automation, and Integration
Beno Benhabib
Detalles del libro
Vista previa del libro
Índice
Citas
Información del libro
From concept development to final production, this comprehensive text thoroughly examines the design, prototyping, and fabrication of engineering products and emphasizes modern developments in system modeling, analysis, and automatic control. This reference details various management strategies, design methodologies, traditional production techniqu
Preguntas frecuentes
¿Cómo cancelo mi suscripción?
¿Cómo descargo los libros?
Por el momento, todos nuestros libros ePub adaptables a dispositivos móviles se pueden descargar a través de la aplicación. La mayor parte de nuestros PDF también se puede descargar y ya estamos trabajando para que el resto también sea descargable. Obtén más información aquí.
¿En qué se diferencian los planes de precios?
Ambos planes te permiten acceder por completo a la biblioteca y a todas las funciones de Perlego. Las únicas diferencias son el precio y el período de suscripción: con el plan anual ahorrarás en torno a un 30 % en comparación con 12 meses de un plan mensual.
¿Qué es Perlego?
Somos un servicio de suscripción de libros de texto en línea que te permite acceder a toda una biblioteca en línea por menos de lo que cuesta un libro al mes. Con más de un millón de libros sobre más de 1000 categorías, ¡tenemos todo lo que necesitas! Obtén más información aquí.
¿Perlego ofrece la función de texto a voz?
Busca el símbolo de lectura en voz alta en tu próximo libro para ver si puedes escucharlo. La herramienta de lectura en voz alta lee el texto en voz alta por ti, resaltando el texto a medida que se lee. Puedes pausarla, acelerarla y ralentizarla. Obtén más información aquí.
¿Es Manufacturing un PDF/ePUB en línea?
Sí, puedes acceder a Manufacturing de Beno Benhabib en formato PDF o ePUB, así como a otros libros populares de Technik & Maschinenbau y Maschinen- und Anlagebau. Tenemos más de un millón de libros disponibles en nuestro catálogo para que explores.
Información
1
Competitive Manufacturing
1.1 MANUFACTURING MATTERS
In the earlier part of the 20th century, manufacturing became a capital-intensive activity. A rigid mode of mass production replaced mostly small-batch and make-to-order fabrication of products. A turning point was the 1920s. With increased household incomes in North America and Europe came large-scale production of household appliances and motor vehicles. These products steadily increased in complexity, thus requiring design standardization on the one hand and labor specialization on the other. Product complexity combined with manufacturing inflexibility led to long product life cycles (up to 5 to 7 years, as opposed to as low as 6 months to 1 year in today’s communication and computation industries), thus slowing down the introduction of innovative products.
In the post-World War II (WWII) era we saw a second boom in the manufacturing industries in Western Europe, the U.S.A., and Japan, with many domestic companies competing for their respective market shares. In the early 1950s, most of these countries imposed heavy tariffs on imports in order to protect local companies. Some national governments went a step further by either acquiring large equities in numerous strategic companies or providing them with substantial subsidies. Today, however, we witness the fall of many of these domestic barriers and the emergence of multinational companies attempting to gain international competitive advantage via distributed design and manufacturing across a number of countries (sometimes several continents), though it is important to note that most such successful companies are normally those that encountered and survived intense domestic competition, such as Toyota, General Motors, Northern Telecom (Nortel), Sony, and Siemens. Rapid expansion of foreign investment opportunities continue to require these companies to be innovative and maintain a competitive edge via a highly productive manufacturing base. In the absence of continuous improvement, any company can experience a rapid drop in investor confidence that may lead to severe market share loss.
Another important current trend is conglomeration via mergers or acquisitions of companies who need to be financially strong and productive in order to be internationally competitive. This trend is in total contrast to the 1970s and 1980s, when large companies (sometimes having a monopoly in a domestic market) broke into smaller companies voluntarily or via government intervention in the name of increased productivity, consumer protection, etc. A similar trend in political and economic conglomeration is the creation of free-trade commercial zones such as NAFTA (the North American Free Trade Agreement), EEC (the European Economic Community), and APEC (the Asia-Pacific Economic Cooperation).
One can thus conclude that the manufacturing company of the future will be multinational, capital as well as knowledge intensive, with a high level of production automation, whose competitiveness will heavily depend on the effective utilization of information technology (IT). This company will design products in virtual space, manufacture them in a number of countries with the minimum possible (hands-on) labor force, and compete by offering customers as much flexibility as possible in choices. Furthermore, such a company will specialize in a minimal number of products with low life cycles and high variety; mass customization will be the order of the day.
In the above context, computer integrated manufacturing (CIM) must be seen as the utilization of computing and automation technologies across the enterprise (from marketing to design to production) for achieving the most effective and highest quality service of customer needs. CIM is no longer simply a business strategy; it is a required utilization of state-of-the-art technology (software and hardware) for maintaining a competitive edge.
In this chapter, our focus will be on major historical developments in the manufacturing industry in the past two centuries. In Sec. 1.2, the beginnings of machine tools and industrial robots will be briefly discussed as a prelude to a more in-depth review of the automotive manufacturing industry. Advancements made in this industry (technological, or even marketing) have benefited significantly other manufacturing industries over the past century. In Sec. 1.3, we review the historical developments in computing technologies. In Secs. 1.4 and 1.5, we review a variety of “manufacturing strategies” adopted in different countries as a prelude to a discussion on the expected future of the manufacturing industry, namely, “information-technology-based manufacturing,” Sec. 1.6.
1.2 POST-INDUSTRIAL-REVOLUTION HISTORY OF MANUFACTURING TECHNOLOGIES
The industrial revolution (1770–1830) was marked by the introduction of steam power to replace waterpower (for industrial purposes) as well as animal-muscle power. The first successful uses for such power in the U.K. and U.S.A. were for river and rail transport. Subsequently, steam power began to be widely used in mechanization for manufacturing (textile, metal forming, woodworking, etc.). The use of steam power in factories peaked around the 1900s with the start of the wide adoption of electric power. Factory electrification was a primary contributor to significant productivity improvements in 1920s and 1930s.
Due to factory mechanization and social changes over the past century, yearly hours worked per person has declined from almost 3000 hours to 1500 hours across Europe and to 1600 hours in North America. However, these decreases have been accompanied by significant increases in labor productivity. Notable advances occurred in the standard of living of the population in these continents. Gross Domestic Product (GDP) per worker increased seven fold in the U.S., 10-fold in Germany, and more than 20-fold in Japan between 1870s and the 1980s.
1.2.1 Machine Tools
Material-removal machines are commonly referred to as “machine tools.” Such machines are utilized extensively in the manufacturing industry for a variety of material-removal tasks, ranging from simple hole making (e.g., via drilling and boring) to producing complex contoured surfaces on rotational or prismatic parts (e.g., via turning and milling).
J.Wilkinson’s (U.K.) boring machine in 1774 is considered to be the first real machine tool. D.Wilkinson’s (U.S.A.) (not related to J.Wilkinson) screw-cutting machine patented in 1798 is the first lathe. There exists some disagreement as to who the credit should go to for the first milling machine. R.Johnson (U.S.A.) reported in 1818 about a milling machine, but probably this machine was invented by S.North well before then. Further developments on the milling machine were reported by E.Whitney and J. Hall (U.S.A.) around 1823 to 1826. F.W.Howe (U.K.) is credited with the design of the first universal milling machine in 1852, manufactured in the U.S.A. in large numbers by 1855. The first company to produce machine tools, 1851, Gage, Warner and Whitney, produced lathes, boring machines, and drills, though it went out of business in the 1870s.
As one would expect, metal cutting and forming has been a major manufacturing challenge since the late 1700s. Although modern machine tools and presses tend to be similar to their early versions, current machines are more powerful and effective. A primary reason for up to 100-fold improvements is the advancement in materials used in cutting tools and dies. Tougher titanium carbide tools followed by the ceramic and boronnitride (artificial diamond) tools of today provide many orders of magnitude improvement in cutting speeds. Naturally, with the introduction of automatic-control technologies in 1950s, these machines became easier to utilize in the production of complex-geometry workpieces, while providing excellent repeatability.
Due to the worldwide extensive utilization of machine tools by small, medium, and large manufacturing enterprises and the longevity of these machines, it is impossible to tell with certainty their current numbers (which may be as high as 3 to 4 million worldwide). Some recent statistics, however, quote sales of machine tools in the U.S.A. to be in the range of 3 to 5 billion dollars annually during the period of 1995 to 2000 (in contrast to $300-500 million annually for metal-forming machines). It has also been stated that up to 30% of existing machine tools in Europe, Japan, and the U.S. are of the numerical control (NC) type. This percentage of NC machines has been steadily growing since the mid-1980s, when the percentage was below 10%, due to rapid advancements in computing technologies. In Sec. 1.3 we will further address the history of automation in machine-tool control during the 1950s and 1960s.
1.2.2 Industrial Robots
A manipulating industrial robot is defined by the International Organization for Standardization (ISO) as “An automatically controlled, re-programmable, multi-purpose, manipulative machine with several degrees of freedom, which may be either fixed in place or mobile for use in industrial application” (ISO/TR 8373). This definition excludes automated guided vehicles, AGVs, and dedicated automatic assembly machines.
The 1960s were marked by the introduction of industrial robots (in addition to automatic machine tools). Their initial utilization on factory floors were for simple repetitive tasks in either handling bulky and heavy workpieces or heavy welding guns in point-to-point motion. With significant improvements in computing technologies, their application spectrum was later widened to include arc welding and spray painting in continuous-path motion. Although the commercial use of robots in the manufacturing industry can be traced back to the early 1960s, their widespread use only started in the 1970s and peaked in the 1980s. The 1990s saw a marked decline in the use of industrial robots due to the lack of technological support these robots needed in terms of coping with uncertainties in their environments. The high expectations of industries to replace the human labor force with a robotic one did not materialize. The robots lacked artificial perception ability and could not operate in autonomous environments without external decision-making support to deal with diagnosis and error recovery issues. In many instances, robots replaced human operators for manipulative tasks only to be monitored by the same operators in order to cope with uncertainties.
In late 1980s, Japan clearly led in the number of industrial robots. However, most of these were manipulators with reduced degrees of freedom (2 to 4); they were pneumatic and utilized in a playback mode. Actually, only about 10% of the (over 200,000) robot population could be classified as “intelligent” robots complying with the ISO/TR 8373 definition. The percentage would be as high as 80%, though, if one were to count the playback manipulators mostly used in the automotive industry. Table 1 shows that the primary user of industrial robots has been indeed the automotive industry worldwide (approximately 25–30%) with the electronics industry being a distant second (approximately 10–15%).
Today, industrial robots can be found in many high-precision and high-speed applications. They come in various geometries: serial (anthropomorphic, cylindrical, and gantry) as well as parallel (Stewart platform and hexapod). However, still, due to the lack of effective sensors, industrial robots cannot be utilized to their full capacity in an integrated sense with other production machines. They are mostly restricted to repetitive tasks, whose pick and place locations or trajectories are a priori known; they are not robust to positional deviations of workpiece locations (Figure 1).
TABLE 1 Industrial Robot Population in 1989
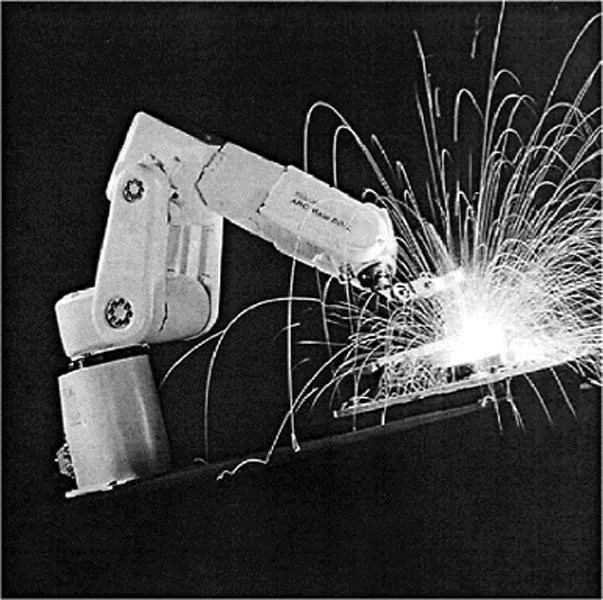
FIGURE 1 A FANUC Mate 50:L welding robot welding a part.
1.2.3 Automotive Manufacturing Industry
The automotive industry still plays a major economic role in many countries where it directly and indirectly employs 5 to 15% of the workforce (Tables 2 to 4). Based on its history of successful mass production that spans a century, many valuable lessons learned in this industry can be extrapolated to other manufacturing industries. The Ford Motor Co., in this respect, has been the most studied and documented car manufacturing enterprise.
Prior to the introduction of its world-famous 1909 Model T car, Ford produced and marketed eight earlier models (A, C, B, F, K, N, R, and S). However, the price of this easy-to-operate and easy-to-maintain car (sold for under $600) was indeed what revolutionized the industry, leading to great demand and thus the introduction of the moving assembly line in 1913. By 1920, Ford was building half the cars in the world (more than 500,000 per year) at a cost of less than $300 each. A total of 15 million Model T cars were made before the end of the product line in 1927 (Figure 2).
TABLE 2 Motor Vehiclea Production Numbers per Year per Country (1000s)
The first automobile, however, is attributed to N.J.Cugnot, a French artillery officer, who made a steam-powered three-wheeled vehicle in 1769. The first internal-combustionbased vehicle is credited to two inventors: the Belgian E.Lenoir (1860) and the Austrian S.Marcus (1864). The first ancestors of modern cars, however, were the separate designs of C.Benz (1885) and G.Daimler (1886). The first American car was built by J.W. Lambert in 1890–1891.
Since the beginnings of the industry, productivity has been primarily achieved via product standardization and mass production at the expense of competitiveness via innovation. Competitors have mostly provided customers with a price advantage over an innovative advantage. Almost 70 automotive companies early on provided customers with substantial innovative differences in their products, but today there remain only three major U.S. car companies that provide technologically very similar products.
TABLE 3 Motor Vehicle Registration by Country by Year (1000s)
TABLE 4 Employment in U.S. Automobile Industry Plants (1000s)
From 1909 to 1926, Ford’s policy of making a single, but best-priced, car allowed its competitors slowly to gain market share, as mentioned above, via technologically similar but broader product lines. By 1925, General Motors (GM) held approximately 40% of the market versus 25% of Ford and 22% of Chrysler. In 1927, although Ford discontinued its production of the Model T, its strategy remained unchanged. It introduced a second generation of its Model A with an even a lower price. (Ford discontinued production for 9 months in order to switch from Model T to Model A). However, once again, the competitiveness-via-price strategy of Ford did not survive long. It was completely abandoned in the early 1930s (primarily owing to the introduction of the V-8 engine), finally leading to some variability in Ford’s product line.
In 1923–1924, industrial design became a mainstream issue in the automobile industry. The focus was on internal design as well as external styling and color choices. In contrast to Ford’s strategy, GM, under the general management of A.P.Sloan (an MIT graduate), decided to develop a line of cars in multiple pricing categories, from the lowest to the highest. Sloan insisted on making GM cars different from the competition’s, different from each other, and different from year to year, naturally at the expense of technological innovation. The objective was not a radical innovation but an offer of variety in frequent intervals, namely incremental changes in design as well as in production processes. Sloan rationalized product variety by introducing several platforms as well as frequent model changes within each platform. His approach to increased productivity was however very similar to Ford’s in that each platform was manufactured in a different plant and yearly model changes were only minor owing to prohibitive costs in radically changing tooling and fixturing more than once every 4 to 6 years. The approach of manufacturing multiple platforms in the same plant in a mixed manufacturing environment was only introduced in the late 1970s by Toyota (Table 5). The question at hand is, naturally, How many platforms does a company need today to be competitive in the decades to come?
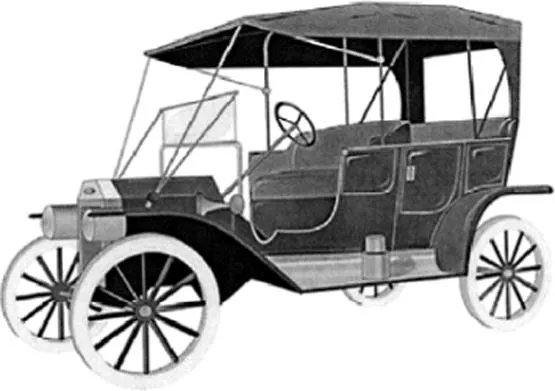
FIGURE 2 The Ford Model T car.
Chrysler followed GM’s lead and offered four basic car lines in 1929; Chrysler, DeSoto, Dodge, and Plymouth. Unlike GM and Ford, however, Chrysler was less vertically integrated and thus more open to innovation introduced by its past suppliers. (This policy allowed Chrysler to gain market share through design flexibility in the pre WWII era).
The automobile’s widespread introduction in the 1920s as a non luxury consumer good benefited other industries, first through the spin-off of manufacturing technologies (e.g., sheet-metal rolling used in home appliances) and second through stimulation of purchases by credit. Annual production of washing machines doubled between 1919 and 1929, while annual refrigerator production rose from 5000 to 890,000 during the same period. Concurrently, the spillover effect of utilization of styling and color as a marketing tool became very apparent. The market was flooded with purple bathroom fixtures, red cookware, and enamelled furniture. One can draw parallels to the period of 1997–2000, when numerous companies, including Apple and Epson, adopted marketing strategies that led to the production of colorful personal computers, printers, disk drives, and so forth.
1.3 RECENT HISTORY OF COMPUTING TECHNOLOGIES
The first electronic computer was built by a team led by P.Eckert and J. Mauchley, University of Pennsylvania, from 1944 to 1947 under the auspices of the U.S. Defense Department. The result was the Electronic
TABLE 5 Platforms/Models for Some Automotive Manufacturers During the Period 1964–1993
Numerical Integrator and Computer (ENIAC); the subsequent commercial version, UNIVAC I, became available in 1950.
The first breakthrough toward the development of modern computers came, however, with the fabrication of semiconductor switching elements (transistors) in 1948. What followed was the rapid miniaturization of the transistors and their combination with capacitors, resistors, etc. in multilayered silicon-based integrated circuits (ICs). Today, millions of such elements are configured within extremely small areas to produce processor, memory, and other types of ICs commonly found in our personal computers and other devices (such as c...
Índice
- Cover Page
- Title Page
- Copyright Page
- Preface
- Acknowledgments
- 1: Competitive Manufacturing
- Part I: Engineering Design
- Part II: Discrete-Parts Manufacturing
- Part III: Automatic Control in Manufacturing
Estilos de citas para Manufacturing
APA 6 Citation
Benhabib, B. (2003). Manufacturing (1st ed.). CRC Press. Retrieved from https://www.perlego.com/book/1599163/manufacturing-design-production-automation-and-integration-pdf (Original work published 2003)
Chicago Citation
Benhabib, Beno. (2003) 2003. Manufacturing. 1st ed. CRC Press. https://www.perlego.com/book/1599163/manufacturing-design-production-automation-and-integration-pdf.
Harvard Citation
Benhabib, B. (2003) Manufacturing. 1st edn. CRC Press. Available at: https://www.perlego.com/book/1599163/manufacturing-design-production-automation-and-integration-pdf (Accessed: 14 October 2022).
MLA 7 Citation
Benhabib, Beno. Manufacturing. 1st ed. CRC Press, 2003. Web. 14 Oct. 2022.