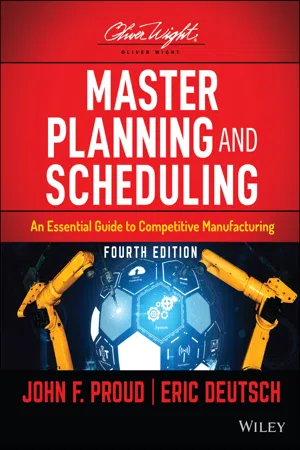
Master Planning and Scheduling
An Essential Guide to Competitive Manufacturing
John F. Proud,Eric Deutsch
- English
- ePUB (apto para móviles)
- Disponible en iOS y Android
Master Planning and Scheduling
An Essential Guide to Competitive Manufacturing
John F. Proud,Eric Deutsch
Información del libro
Discover the practical, real-world advantages of the Oliver Wight master planning and scheduling methodology.
The newly revised Fourth Edition of Master Planning and Scheduling: An Essential Guide to Competitive Manufacturing delivers a masterful exploration of today's master planning and scheduling techniques, as well as an insightful discussion of the future of the master planning and scheduling processes and profession.
Written in the context of an ever-evolving digital environment and augmented with new and critical information required to implement best practices, the book is a guide for practitioners and leaders on the principles of master planning and scheduling and its application in modern and future work environments.
In this book, readers will learn:
- Insights regarding top-down, bottom-up, and side-to-side integration of business practices in support of a company's strategic direction and tactical deployment
- The critical link between time-phased integrated business planning, master planning, master scheduling, capacity planning, and material planning
- "How-to" details and examples to support master planning and scheduling implementation and enhancements within the company's demand and supply organizations
Master Planning and Scheduling is an indispensable guide for supply chain professionals, planners and schedulers in all functional domains of a business. It also belongs on the bookshelves of any executive or manager who seeks to improve their understanding of best practice planning and scheduling processes and how those processes enable a business to outperform the competition through alignment, integration and synchronization across all functions in an organization.
Preguntas frecuentes
Información
1
Chaos in Manufacturing
A TYPICAL SITUATION IN TODAY'S MANUFACTURING WORLD
- The Place: A typical world‐wide manufacturing company
- The Time: 10:00 a.m.
- The Date: Friday, the last day of the month
- Admitting that problems, some serious, exist, and that the current situation is not healthy for the company or the people who work in it;
- Identifying the specific problems—not just the symptoms;
- Determining the cause of the problems;
- Creating and acting on efficient and effective solutions.
Problems in Manufacturing
Symptoms of Master Planning and Scheduling Problems | |
---|---|
Uncontrollable costs | Hot lists |
Disruptions on the shop floor | Frequent schedule changes |
Late deliveries to customers | Many full‐time expediters |
Late deliveries from suppliers | Customer complaints |
Unplanned overtime/off‐loading | Many “past due” orders and plans |
High work‐in‐process | Long queues |
Mismatched inventories | End‐of‐month crunch |
Over/underutilized resources | Finger pointing/low morale |
THE INACCURATE FORECAST
Índice
- Cover
- Table of Contents
- Praise for Master Planning and Scheduling — the Book, the Process, the Results!
- Title Page
- Copyright
- Dedication
- Oliver Wight Supply Chain Management Book Series
- Acknowledgments
- Foreword
- Introduction: The Master of All Detailed Supply Plans and Schedules (Below-the-Line)
- Initial Thoughts: People and Process and Profession
- 1 Chaos in Manufacturing
- 2 Why Master Planning and Scheduling
- 3 The Mechanics of Master Planning and Scheduling
- 4 Managing the Supply Chain with Master Planning and Scheduling
- 5 Using the Master Planning and Scheduling Output for Make‐to‐Stock Products
- 6 Where and What to Master Plan and Master Schedule
- 7 Scheduling in a Flow Environment
- 8 Planning Bills
- 9 Two‐Level Master Planningand Scheduling Coupled with Other Advanced Techniques
- 10 Using Master Planning and Scheduling Output for Make‐to‐Order Products
- 11 Master Planning and Scheduling in Custom‐Product Environments
- 12 Finishing or Final Assembly Scheduling
- 13 Data Integrity Requirements to Support Master Planning and Scheduling
- 14 Integrated Business Planning
- 15 Resource Requirements Planning and Rough Cut Capacity Planning
- 16 Supply Management and Aggregate Master Planning
- 17 Demand Management and Aggregate Master Planning
- 18 The Proven Path to a Successful Master Planning and Scheduling Implementation (Phase 1)
- 19 The Proven Path to a Successful Master Planning and Scheduling Implementation (Phase 2)
- 20 The Proven Path to a Successful Master Planning and Scheduling Implementation (Phase 3)
- Epilogue: Order from Chaos
- Final Thoughts: People and Process and Profession
- Appendix A: Master Planning and Scheduling Process and Performance Standards
- Appendix B: Master Planning and Scheduling Improvement Initiative Task Listing
- Appendix C: Master Planning and Scheduling Policy, Procedure, and Flow Diagram
- Appendix D: Master Planning and Scheduling
- Appendix E: Supply Chain Management Overall Process Flow Diagram (An Example)
- Appendix F: Master Planning and Scheduling Process Flow Diagram Examples
- Appendix G: Master Planning and Scheduling RACI Examples
- Appendix H: Master Planning and Scheduling Spinoff Task Team Charter
- Appendix I: Master Planning and Scheduling Oliver Wight International OfferingsFounders’ and Co‐Authors’ Biographies
- Glossary
- Index
- End User License Agreement