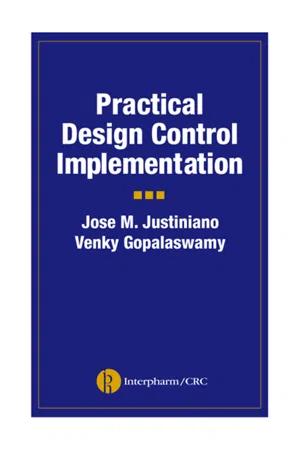
eBook - ePub
Practical Design Control Implementation for Medical Devices
Jose Justiniano, Venky Gopalaswamy
This is a test
- 232 pagine
- English
- ePUB (disponibile sull'app)
- Disponibile su iOS e Android
eBook - ePub
Practical Design Control Implementation for Medical Devices
Jose Justiniano, Venky Gopalaswamy
Dettagli del libro
Anteprima del libro
Indice dei contenuti
Citazioni
Informazioni sul libro
Bringing together the concepts of design control and reliability engineering, this book is a must for medical device manufacturers. It helps them meet the challenge of designing and developing products that meet or exceed customer expectations and also meet regulatory requirements. Part One covers motivation for design control and validation, desig
Domande frequenti
Come faccio ad annullare l'abbonamento?
È semplicissimo: basta accedere alla sezione Account nelle Impostazioni e cliccare su "Annulla abbonamento". Dopo la cancellazione, l'abbonamento rimarrà attivo per il periodo rimanente già pagato. Per maggiori informazioni, clicca qui
È possibile scaricare libri? Se sì, come?
Al momento è possibile scaricare tramite l'app tutti i nostri libri ePub mobile-friendly. Anche la maggior parte dei nostri PDF è scaricabile e stiamo lavorando per rendere disponibile quanto prima il download di tutti gli altri file. Per maggiori informazioni, clicca qui
Che differenza c'è tra i piani?
Entrambi i piani ti danno accesso illimitato alla libreria e a tutte le funzionalità di Perlego. Le uniche differenze sono il prezzo e il periodo di abbonamento: con il piano annuale risparmierai circa il 30% rispetto a 12 rate con quello mensile.
Cos'è Perlego?
Perlego è un servizio di abbonamento a testi accademici, che ti permette di accedere a un'intera libreria online a un prezzo inferiore rispetto a quello che pagheresti per acquistare un singolo libro al mese. Con oltre 1 milione di testi suddivisi in più di 1.000 categorie, troverai sicuramente ciò che fa per te! Per maggiori informazioni, clicca qui.
Perlego supporta la sintesi vocale?
Cerca l'icona Sintesi vocale nel prossimo libro che leggerai per verificare se è possibile riprodurre l'audio. Questo strumento permette di leggere il testo a voce alta, evidenziandolo man mano che la lettura procede. Puoi aumentare o diminuire la velocità della sintesi vocale, oppure sospendere la riproduzione. Per maggiori informazioni, clicca qui.
Practical Design Control Implementation for Medical Devices è disponibile online in formato PDF/ePub?
Sì, puoi accedere a Practical Design Control Implementation for Medical Devices di Jose Justiniano, Venky Gopalaswamy in formato PDF e/o ePub, così come ad altri libri molto apprezzati nelle sezioni relative a Medizin e Pharmakologie. Scopri oltre 1 milione di libri disponibili nel nostro catalogo.
Informazioni
PART ONE
Practical Design Control Implementation
INTRODUCTION
The complexity of applications and technologies in the medical device industry is enormous. Medical devices range from simple handheld tools to complex computercontrolled surgical machines, from implantable screws to artificial organs, from bloodglucose test strips to diagnostic imaging systems and laboratory test equipment. Given this complexity, it is no surprise that these devices are designed and manufactured by companies that not only vary in size and structure, but use different methods of design and development as well as management.
Technological advances allow the planning, design, manufacture, operation, and maintenance of a variety of medical device components and systems to be performed every day with great efficiency. When these products and systems fail, however, the result could range from inconvenience and irritation to a critical impact on society. One of the major concerns of users of products and systems is their reliability and availability. Needless to say, because high reliability and availability will result in better customer satisfaction, the current trend in product and system design is toward attaining these goals. Advances in technology have resulted in better manufacturing processes, production control, product design, and so on, and have enabled engineers to design, manufacture, and build reliable components and systems.
Until few years ago, a newly hired professional in the medical device or pharmaceutical industry was typically told that Good Manufacturing Practice (GMP) merely involved meeting specifications and following written procedures. The job of the quality professional was to be a “watchdog” of all documentation that support the manufacturing of the product (it still is, especially in the pharmaceutical arena). If manufacturing operations had to change a specification, no information was available to connect the specification to customer requirements or to address the consequences of such proposed changes in the field. It was simply not acceptable practice to review or challenge the design engineering group’s decision to set the specification in a certain way.
Through our combined experience in the automotive, telecommunications, electronics, and medical device industries, we know that such connections and their formal documentation is just “commonsense engineering design work.” The medical device industry—especially those medical device companies that are ISO 9001 certified— is fast learning what the automotive and aerospace industries already knew:
- The key to effective design and development of a product is to utilize an effective design control process.
- Using design control process and supporting systems will consistently result in products that are most likely to meet customer and regulatory requirements.
For all medical device manufacturers interested in marketing their products in the United States, the time to adopt better product design and development practices is now, especially because the grace period for implementing the Food and Drug Admininstration (FDA) design control guidelines ended on June 1, 1998. This means that a medical device manufacturer can now be cited via 483s, warning letters, or other FDA enforcement actions for failing to comply with the design control requirements of the Quality System Regulation. The encouraging news is that of the 582 design control inspections conducted by the FDA between June 1, 1997, and June 1, 1998, 355 (60 percent) of the devices covered were subject to design controls, and 530 (91 percent) of the firms had established design control procedures.
Despite this encouraging news, some firms might be in compliance by investing heavily in consultants as well as internal resources without obtaining the expected level of understanding required to implement design control guidance. Our strong belief is that canned software programs and even “quality systems” can be bought without achieving the essence or intent of the design control regulation. Compliance to design control guidance through established procedures is basic and will certainly have positive effects on traditionally uncontrolled disciplines in the design and development of medical devices.
As part of its focus on design control enforcement, the October 1999 issue of “The Silver Sheet” presented change control problems cited in 483s issued between June 1, 1998, and September 30, 1999. The top 12 deficiencies are cited in Table I.1 and shown graphically in Figure I.1.
The management and technical personnel of those firms that spent a great deal of time and resources might still be asking themselves the same questions:
- What is required in design control?
- What sections of the guidance document are applicable to us?
- Where is the line between process and product development?
- Will the FDA design control requirements apply to a manufacturing facility?
- What is “verification,” and what is its connection to “validation”?
- What shall we do with existing products?
- During a pilot or qualification run, are we validating the design of the product or the process?
TABLE I.1 Top 12 Design Deficiencies Cited by the FDA
The positive effects of successful design control implementation can be very evident: fewer customer complaints and medical device reports (MDRs), more satisfied customers, and faster time to market. In addition, manufacturing operations should see fewer “deviations,” fewer “nonconforming” reports, less scrap, and fewer retests or other “re-do” operations before shipping the products. Through the implementation of design control guidelines, the FDA has given the industry a compelling reason to increase its markets or market share by improving quality. Those companies that do not approach design control with enthusiasm or strength of conviction may eventually realize their weak positions among competitors.
Medical device companies that are in the process of true implementation of design control must realize that their industry is, as mentioned earlier, very complex and “high tech.” The challenges posed by the elements involving life sciences, engineering, statistics, and mathematics, to mention a few, are enormous. A good reality check is to answer a set of questions that include the following:
- Do we know what we are doing?
- Are our design control procedures practical and effective?
- Can we predict our device performance and safety level in the marketplace?
- Are our control parameters adequate to evaluate internal processes as well as field performance?
- How can we measure design control effectiveness?
- Are we effectively capturing the knowledge that goes into the design and development of medical devices?
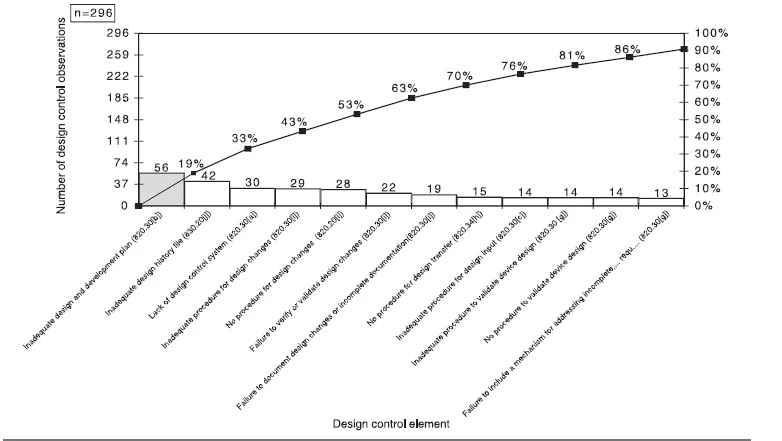
FIGURE 1.1 Design control deficiencies cited by the FDA.
Source: Adapted from “The Silver Sheet.” Copyright 1999 F-D-C Reports, Inc. Reprinted with permission.
The books currently available to answer some of these questions focus either on design control or reliability engineering. No current book brings these two concepts together. With these realizations in mind, we have written this book to help medical device companies to understand the practical implementation aspects of design control guidelines. We also present device reliability engineering tools and techniques, which complement the successful implementation of design control.
Content
Chapters 1 through 5 of this book focus on the practical aspects of design control implementation for medical devices. Design control implementation is not extremely difficult. Its fundamental concepts as presented by the FDA are not new and are no different than those already found in books such as those by Deming (1986) and Juran (1992). What is new, however, is the adoption by the FDA of such principles and their consequent enforcement. Also new to the medical device industry will be the different technical concepts as well as the tools and techniques necessary to implement design control. Every attempt has been made in each chapter of this book to link the FDA design control elements with practical advice and insight.
Chapters 6 through 10 focus on the reliability of medical devices and its link to design control. This concept is utilized during the entire product life cycle and is complementary to design control. Reliability engineering characterizes the objective of any engineering science—the achievement of products that are reliable and are easy to operate and maintain in a cost-effective manner. Reliability analysis is also a fundamental part in any safety assessment of potentially dangerous products, which are currently being subjected to even more stringent regulations and public attention.
Typical product design and development phases with the corresponding reliability and risk analysis tools such as failure modes and effects analysis (FMEA), hazard analysis, reliability planning, reliability prediction, design verification, and validation are presented with easy-to-understand examples. The linkage of reliability engineering to design control is presented throughout to help the reader understand how these concepts are interrelated. We sincerely think that this book will help medical device companies, both small and large, to successfully implement design control and reliability engineering to not only meet the FDA guidelines but also meet or exceed customer expectation.
Intended Audience
We wrote this book with all levels of management and technical personnel in mind. Whereas the Introduction and Chapter 1 can give top management a macro view of what it takes to develop and design medical devices per the Quality System Regulation, Chapters 2 through 5 are more tactical in nature. These chapters, however, provide useful information to top management regarding what kinds of human resources and technical knowledge are needed.
Chapters 6 and beyond are specifically aimed at technical personnel involved with product design and design changes. A reliability engineering background is not necessary because the material presented is very simple and can be seen as an introduction.
Another way to look at the chapters is as follows: Chapters 1 through 5 address the issue of how to reliably design and develop medical devices, whereas Chapters 6 through 11 address the issue of how to design and develop reliable medical devices.
This book is useful whether the reader is interested in strategic or tactical implementation of design control for medical device design. The main purpose of this book is to expose the medical device industry audience to a topic that is very applicable to design control and validation. Top management is encouraged to read Chapters 6 through 11 to assess the resources needed to design reliable medical devices.
CHAPTER ONE
Motivation for Design Control and Validation
The motivation for controlling the process of designing medical devices is twofold. First, the obvious motivation is that the FDA included such control as part of its Quality System Regulation. The second and better motivation is that such a set of disciplines can improve business for any manufacturer. This chapter aims to impart an understanding of what the FDA and its Center for Devices and Radiological Health (CDRH) are seeking with design controls and validations. At the same time, the chapter addresses the business benefits beyond being in compliance with the regulation.
Motivation from the FDA and the CDRH
CDRH data analysis of the proportion of quality problems resulting in recalls between 1985 and 1989 revealed that approximately 50 percent were due to Good Manufacturing Practice (GMP) and 45–50 percent were preproduction (with no legal authority over the design process) (FDA CDRH “Human Factors Implications”). Half of the GMP problems were related to the manufacturer’s ability to control the manufacturing process.1 Both percentages suggest the need for a greater emphasis on design control and process validation.
A January 1990 FDA study, “Device Recalls: A Study of Quality Problems,” based on data between October 1983 and September 1989, found that 44 percent of the quality problems leading to voluntary recalls were attributable to device design deficiencies (FDA CDRH 1990). The FDA deemed that percentage to be unacceptable and, after reviewing the data, determined that most of these design problems were preventable. Another FDA study showed that design controls can reduce design problems by 73 percent, which is equivalent to preventing 44 deaths per year (FDA CDRH 1996a). The FDA understands that ineffective and/or unsafe devices can be the result of informal device development. In practical terms, informality is the lack of a disciplined approach.
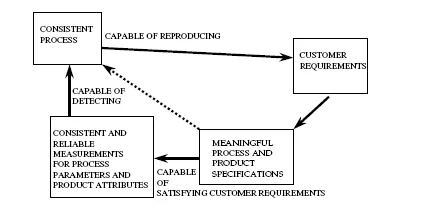
FIGURE 1.1 Practical business needs.
The Safe Medical Devices Act of 1990 added design control (820.30) requirements to the GMP in section 520(f ) of the act. Prior to 1990, the FDA used the term “preproduction” in an attempt to go beyond the typical “cGMPs” (current GMPs). Additionally, since 1990, the medical device industry has seen heavier scrutiny on compliance with process validation (820.75) and the effectiveness of corrective and preventive action (CAPA; 820.70[a] and [b], and 820.100[2] and [3]).
The Business Motivation
Any business that develops and manufactures any product has a set of practical needs. Such a set of needs becomes more relevant as the application it serves as well as the technology it uses become more complex. Figure 1.1 depicts this relationship. The 1:1 correlation between FDA Quality System Regulation provisions and business needs is shown in Table 1.1.
Business Growth, Competition, and FDA Regulations
All businesses have to understand the markets or market segments they serve. This is a basic input to develop business growth strategies that are usually shaped by competition. Business strategies are typically based on planned actions aimed at dealing with the forces of competition (Porter 1979), which include:
- the threat of new entrants,
- the bargaining power of suppliers,
- the bargaining po...
Indice dei contenuti
- Cover Page
- Title Page
- Copyright Page
- PART ONE: Practical Design Control Implementation
- PART TWO: Medical Device Reliability
Stili delle citazioni per Practical Design Control Implementation for Medical Devices
APA 6 Citation
Justiniano, J., & Gopalaswamy, V. (2003). Practical Design Control Implementation for Medical Devices (1st ed.). CRC Press. Retrieved from https://www.perlego.com/book/1711969/practical-design-control-implementation-for-medical-devices-pdf (Original work published 2003)
Chicago Citation
Justiniano, Jose, and Venky Gopalaswamy. (2003) 2003. Practical Design Control Implementation for Medical Devices. 1st ed. CRC Press. https://www.perlego.com/book/1711969/practical-design-control-implementation-for-medical-devices-pdf.
Harvard Citation
Justiniano, J. and Gopalaswamy, V. (2003) Practical Design Control Implementation for Medical Devices. 1st edn. CRC Press. Available at: https://www.perlego.com/book/1711969/practical-design-control-implementation-for-medical-devices-pdf (Accessed: 14 October 2022).
MLA 7 Citation
Justiniano, Jose, and Venky Gopalaswamy. Practical Design Control Implementation for Medical Devices. 1st ed. CRC Press, 2003. Web. 14 Oct. 2022.