
This is a test
- English
- ePUB (mobile friendly)
- Available on iOS & Android
eBook - ePub
Book details
Book preview
Table of contents
Citations
About This Book
The book is concerned with design of cold-formed steel structures in building based on the Eurocode 3 package, particularly on EN 1993-1-3.
It contains the essentials of theoretical background and design rules for cold-formed steel sections and sheeting, members and connections for building applications.
Elaborated examples and design applications - more than 200 pages - are included in the respective chapters in order to provide a better understanding to the reader.
Frequently asked questions
At the moment all of our mobile-responsive ePub books are available to download via the app. Most of our PDFs are also available to download and we're working on making the final remaining ones downloadable now. Learn more here.
Both plans give you full access to the library and all of Perlego’s features. The only differences are the price and subscription period: With the annual plan you’ll save around 30% compared to 12 months on the monthly plan.
We are an online textbook subscription service, where you can get access to an entire online library for less than the price of a single book per month. With over 1 million books across 1000+ topics, we’ve got you covered! Learn more here.
Look out for the read-aloud symbol on your next book to see if you can listen to it. The read-aloud tool reads text aloud for you, highlighting the text as it is being read. You can pause it, speed it up and slow it down. Learn more here.
Yes, you can access Design of Cold-formed Steel Structures by in PDF and/or ePUB format, as well as other popular books in Technology & Engineering & Civil Engineering. We have over one million books available in our catalogue for you to explore.
Information
Chapter 1
INTRODUCTION TO COLD-FORMED STEEL DESIGN
1.1 GENERAL
Cold-formed steel products are found in all aspects of modern life. The use of these products are multiple and varied, ranging from “tin” cans to structural piling, from keyboard switches to mainframe building members. Nowadays, a multiplicity of widely different products, with a tremendous diversity of shapes, sizes, and applications are produced in steel using the cold-forming process.
The use of cold-formed steel members in building construction began about the 1850s in both the United States and Great Britain. However, such steel members were not widely used in buildings until 1940.
In recent years, it has been recognised that cold-formed steel sections can be used effectively as primary framing components. In what concerns cold-formed steel sections, after their primarily applications as purlins or side rails, the second major application in construction is in the building envelope. Options for steel cladding panels range from inexpensive profiled sheeting for industrial applications, through architectural flat panels used to achieve a prestigious look of the building. Light steel systems are widely used to support curtain wall panels. Cold-formed steel in the form of profiled decking has gained widespread acceptance over the past fifteen years as a basic component, along with concrete, in composite slabs. These are now prevalent in the multi-storey steel framed building market. Cold-formed steel members are efficient in terms of both stiffness and strength. In addition, because the steel may be even less than 1 mm thick, the members are light weight. The already impressive load carrying capabilities of cold-formed steel members will be enhanced by current work to develop composite systems, both for wall and floor structures.
The use of cold-formed steel structures is increasing throughout the world with the production of more economic steel coils particularly in coated form with zinc or aluminium/zinc coatings. These coils are subsequently formed into thin-walled sections by the cold-forming process. They are commonly called “Light gauge sections” since their thickness has been normally less than 3 mm. However, more recent developments have allowed sections up to 25 mm to be cold-formed, and open sections up to approximately 8 mm thick are becoming common in building construction. The steel used for these sections may have a yield stress ranging from 250 MPa to 550 MPa (Hancock, 1997). The higher yield stress steels are also becoming more common as steel manufacturers produce high strength steel more efficiently.
The use of thinner sections and high strength steels leads to design problems for structural engineers which may not normally be encountered in routine structural steel design. Structural instability of sections is most likely to occur as a result of the thickness of the sections, leading to reduced buckling loads (and stresses), and the use of higher strength steel typically makes the buckling stress and yield stress of the thin-walled sections approximately equal. Further, the shapes which can be cold-formed are often considerably more complex than hot-rolled steel shapes such as I-sections and unlipped channel sections. Cold-formed sections commonly have mono-symmetric or point-symmetric shapes, and normally have stiffening lips on flanges and intermediate stiffeners in wide flanges and webs. Both simple and complex shapes can be formed for structural and non-structural applications as shown in Figure 1.1. Special design standards have been developed for these sections.
In the USA, the Specification for the design of cold-formed steel structural members of the American Iron and Steel Institute was first produced in 1946 and has been regularly updated based on research to the most recent 2007 edition (AISI, 1996, 1999, 2001, 2004, 2007). The first edition of the unified North American Specification (AISI, 2001) was prepared and issued in 2001, followed by Supplement 2004: Appendix 1, Design of Cold-Formed Steel Structural Members Using Direct Strength Method (AISI, 2004). It is applicable to the United States, Canada and Mexico for the design of cold-formed steel structural members. In 2007, the second edition of the North American Specification for the Design of Cold- Formed Steel Structural Members was issued (AISI, 2007). The document was prepared on the basis of the 2001 edition of the Specification, the Supplement 2004 to the 2001 Specification, and subsequent developments. The new and revised provisions provide up-to-date information for the design of cold-formed steel structural members, connections, assemblies, and systems.
Figure 1.1 – Collection of cold-formed steel sections shapes: a) sections for cold-formed steel structural members; b) profiled sheets
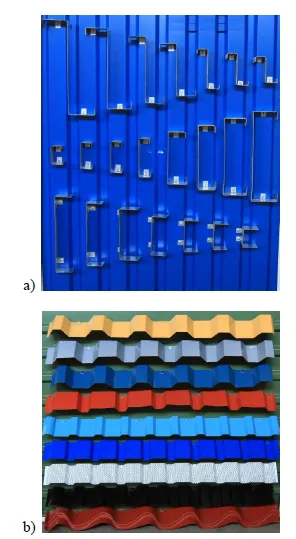
In Europe, the ECCS Committee TC7 originally produced the European Recommendations for the design of light gauge steel members in 1987 (ECCS, 1987). This European document has been further developed and published in 2006 as the European Standard Eurocode 3: Design of steel structures. Part 1-3: General Rules. Supplementary rules for cold-formed thin gauge members and sheeting (CEN, 2006a).
In Australia and New Zeeland, a revised limit states design standard AS/NZS4600 for the design of cold-formed steel structures was published in December 2005 (AS/NZS 4600:2005).
The market share of cold-formed structural steelwork continues to increase in the developed world. The reasons for this include the improving technology of manufacture and corrosion protection which leads, in turn, to the increase competitiveness of resulting products as well as new applications. Recent studies have shown that the coating loss for galvanised steel members is sufficiently slow, and indeed slows down to effectively zero, that a design life in excess of 60 years can be guaranteed.
The range of use of cold-formed steel sections specifically as load-bearing structural components is very wide, encompassing residential, office and industrial buildings, the automobile industry, shipbuilding, rail transport, the aircraft industry, highway engineering, agricultural and industry equipment, office equipment, chemical, mining, petroleum, nuclear and space industries.
This book is primarily concerned with the design of cold-formed steel members and structures in building construction in Europe and for this reason it is based on the European Design Code EN1993-1-3 (CEN, 2006a).
1.2 COLD-FORMED STEEL SECTIONS
1.2.1 Types of cold-formed steel sections
Cold-formed members and profiled sheets are steel products made from coated or uncoated hot-rolled or cold-rolled flat strips or coils. Within the permitted range of tolerances, they have constant or variable cross section.
Cold-formed structural members can be classified into two major types:
– Individual structural framing members;
– Panels and decks.
Individual structural members (bar members) obtained from so called “long products” include:
– single open sections, shown in Figure 1.2a;
– open built-up sections (Figure 1.2b);
– closed built-up sections (Figure 1.2c).
Figure 1.2 – Typical forms of sections for cold-formed structural members
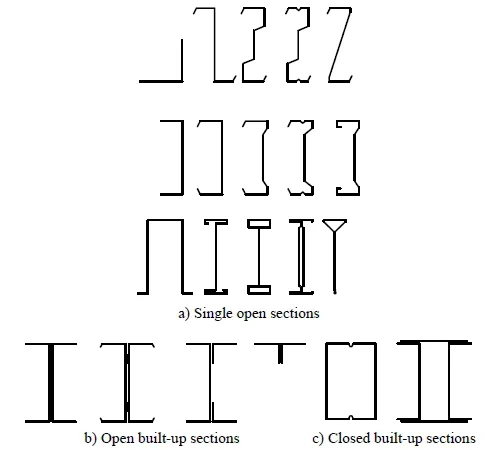
Usually, the depth of cold-formed sections for bar members ranges from 50 – 70 mm to 350 – 400 mm, with thickness from about 0.5 mm to 6 mm. Figure 1.3 shows, as an example, some series of lipped channel and “sigma” sections (www.kingspanstructural.com/multibeam/ – Multibeam products).
Figure 1.3 – Multibeam sections: a) Lipped Channels; b) Σ sections
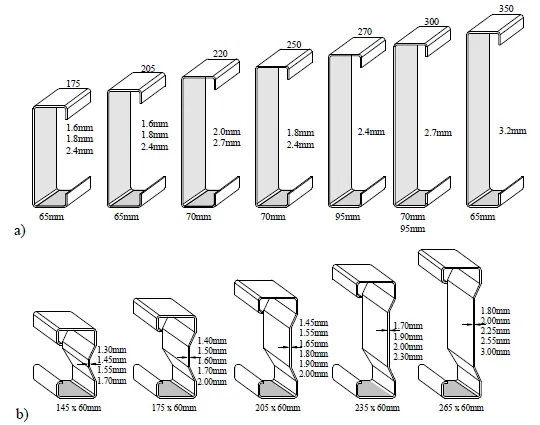
Panels and decks are made from profiled sheets and linear trays (cassettes) as shown in Figure 1.4. The depth of panels usually ranges from 20 to 200 mm, while thickness is from 0.4 to 1.5 mm.
Figure 1.4 – Profiled sheets and linear trays
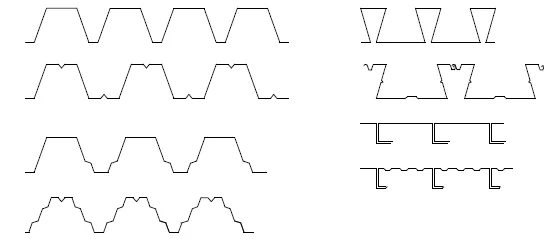
Figure 1.5 shows examples of Rannila corrugated sheets for roofing, wall cladding systems and load-bearing deck panels.
Figure 1.5 – Rannila sheeting products
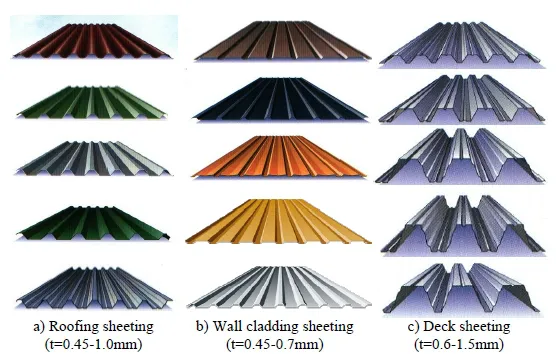
In order to increase the stiffness of both cold-formed steel sections and sheeting, edge and intermediate stiffeners are used (Figure 1.6); they can be easily identified in examples from Figures 1.3 and 1.5.
Figure 1.6 – Typical forms of stiffeners for cold-formed members and sheeting
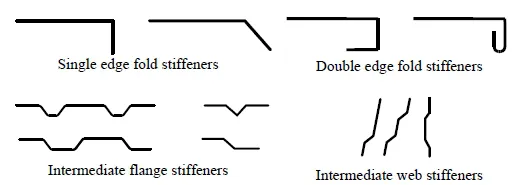
In general, cold-formed steel sections provide the following advantages in building construction (Yu, 2000):
- As compared with thicker hot-rolled shapes, cold-formed steel members can be manufactured for relatively light loads and/or short spans;
- Nestable sections can be produced, allowing for compact packaging and shipping;
- Unusual sectional configurations can be produced economically by cold-forming operations (see Figure 1.1), and consequently favourable strength-to-weight ratios can be obtained;
- Load-carrying panels and decks can provide useful surfaces for floor, roof, and wall construction, and in other cases they can also provide enclosed cells for electrical and other conduits;
- Load-carrying panels and decks not only withstand loads normal to their surfaces, but they can also act as shear diaphragms to resist force in their own planes if they are adequately interconnected to each other and to supporting members.
Compared with other materials such timber and concrete, the following qualities can be realised for cold-formed steel structural members.
- Lightness;
- High strength and stiffness;
- Ability to provide long spans, up to 12 m (Rhodes, 1991);
- Ease of prefabrication and mass production;
- Fast and easy erection and installation;
- Substantial elimination of delays due to weather;
- More accurate detailing;
- Non-shrinking and non-creeping at ambient temperatures;
- Formwork unnecessary;
- Termite-proof and rot-proof;
- Uniform quality;
- Economy in transportation and handling;
- Non-combustibility;
- Recyclable material.
The combination of the above-mentioned advantages can result in cost saving in construction.
1.2.2 Manufacturing
Cold-formed members are normally manufactured by one of two processes. These are:
- Roll forming;
- Folding and press braking.
Roll forming consists of feeding a continuous steel strip through a series of opposing rolls to progressively deform the steel plastically to form the desired shape. Each pair of rolls produces a fixed amount of deformation in a sequence of type shown in Figure 1.7a. Each pair of opposing rolls is called a stage as shown in Figure 1.7. In general, the more complex the cross sectional shape, the greater the number of stages required. In the case of cold-f...
Table of contents
- COVER
- CONTENTS
- ECCS EUROCODE DESIGN MANUALS
- TITLE PAGE
- COPYRIGHT
- FOREWORD
- PREFACE
- Chapter 1: INTRODUCTION TO COLD-FORMED STEEL DESIGN
- Chapter 2: BASIS OF DESIGN
- Chapter 3: BEHAVIOUR AND RESISTANCE OF CROSS SECTION
- Chapter 4: BEHAVIOUR AND DESIGN RESISTANCE OF BAR MEMBERS
- Chapter 5: SHEETING ACTING AS A DIAPHRAGM (STRESSED SKIN DESIGN)
- Chapter 6: STRUCTURAL LINER TRAYS
- Chapter 7: CONNECTIONS
- Chapter 8: BUILDING FRAMING
- REFERENCES