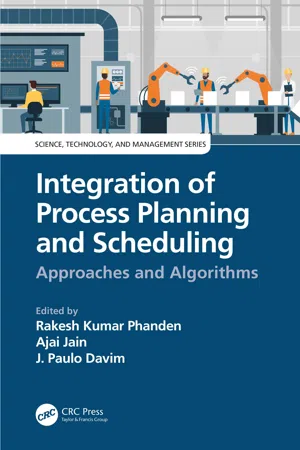
eBook - ePub
Integration of Process Planning and Scheduling
Approaches and Algorithms
This is a test
- 226 pages
- English
- ePUB (mobile friendly)
- Available on iOS & Android
eBook - ePub
Integration of Process Planning and Scheduling
Approaches and Algorithms
Book details
Book preview
Table of contents
Citations
About This Book
Both process planning and scheduling are very important functions of manufacturing, which affect together the cost to manufacture a product and the time to deliver it. This book contains various approaches proposed by researchers to integrate the process planning and scheduling functions of manufacturing under varying configurations of shops. It is useful for both beginners and advanced researchers to understand and formulate the Integration Process Planning and Scheduling (IPPS) problem effectively.
Features
-
- Covers the basics of both process planning and scheduling
-
- Presents nonlinear approaches, closed-loop approaches, as well as distributed approaches
-
- Discuss the outfit of IPPS in Industry 4.0 paradigm
-
- Includes the benchmarking problems on IPPS
-
- Contains nature-algorithms and metaheuristics for performance measurements in IPPS
-
- Presents analysis of energy-efficient objective for sustainable manufacturing in IPPS
Frequently asked questions
At the moment all of our mobile-responsive ePub books are available to download via the app. Most of our PDFs are also available to download and we're working on making the final remaining ones downloadable now. Learn more here.
Both plans give you full access to the library and all of Perlego’s features. The only differences are the price and subscription period: With the annual plan you’ll save around 30% compared to 12 months on the monthly plan.
We are an online textbook subscription service, where you can get access to an entire online library for less than the price of a single book per month. With over 1 million books across 1000+ topics, we’ve got you covered! Learn more here.
Look out for the read-aloud symbol on your next book to see if you can listen to it. The read-aloud tool reads text aloud for you, highlighting the text as it is being read. You can pause it, speed it up and slow it down. Learn more here.
Yes, you can access Integration of Process Planning and Scheduling by Rakesh Kumar Phanden, Ajai Jain, J. Paulo Davim in PDF and/or ePUB format, as well as other popular books in Negocios y empresa & Gestión de proyectos. We have over one million books available in our catalogue for you to explore.
Information
1
Integration of Process Planning and Scheduling: Introduction
Rakesh Kumar Phanden
Amity University Uttar Pradesh
Ajai Jain
National Institute of Technology Kurukshetra
CONTENTS
1.1 Introduction
1.2 Process Planning
1.3 Classification of Process Planning
1.3.1 Manual Process Planning
1.3.2 Computer-aided Process Planning (CAPP)
1.3.2.1 Variant CAPP Approach
1.3.2.2 Generative CAPP Approach
1.3.2.3 Semi-generative CAPP Approach
1.4 Master Production Scheduling (MPS)
1.5 Detailed Scheduling
1.5.1 Completion Time
1.5.2 Makespan
1.5.3 Flow Time
1.5.4 Lateness
1.5.5 Tardiness
1.5.6 Number of Tardy and Early Jobs
1.5.7 Throughput
1.6 Classification of Scheduling Approaches
1.7 Job Shop Scheduling
1.8 IPPS
1.9 IPPS in Industry 4.0 Paradigm
1.10 The Takeaway
References
1.1 Introduction
Manufacturing companies are striving for effective allocation of human resources to equipment/machines, as well as effective allocation of equipment/machines to raw material (product to be manufactured), in order to achieve better business results by enhancing the shop floor efficiency. There are different manufacturing functions which play an important role in enhancing the business output such as process planning, estimating and costing, scheduling, dispatching, inspection and expediting materials control, loading/unloading, etc. However, process planning, as well as scheduling, are the utmost commanding and critical functions that directly affect the performance of a production system. Also, Integration of Process Planning and Scheduling (IPPS) is essential to break down the wall between the two departments by increasing the pace of information exchange. This chapter is presenting the basics of process planning, production scheduling, IPPS, configurations of the manufacturing environment and its performance measures, as well the role of IPPS in the Industry 4.0 paradigm.
1.2 Process Planning
Process planning is performed in both discrete and process industries. In general, process planning can be divided into machining planning and assembly planning. In the former, machining instructions are determined for each part on an individual machining centre, whereas in assembly planning, as the name represents, only assembly instructions are determined to form a product. Basically, machining planning has been simplified as process planning or manufacturing process planning. It is important to understand the various terms like process, operation, and operation sequencing used in process planning. Process means a continuous procedure in which one or more parts are machined (treated or processed) on one or more machines by one or more operators, for instance, the rough drilling process of a hole, finish drilling process of the hole by a drilling machine, grinding process on a grinder wheel, etc. Operation is the part of a process in which the machining surface, machine tool, and machining conditions (feed, speed, depth of cut) remain unchanged. Operation is one small section of a process. When all operations of a process are arranged in the desired order, the arrangement is called operation sequencing. According to Society of Manufacturing Engineers (SME), process planning is defined as a systematic determination of the methods by which a product is manufactured economically and competitively. It connects design and manufacturing stages and involves a great amount of decision-making among various engineering activities. Process planning follows the procedural steps which are initialised with the recognition of product design specifications (data), trailed by the selection of manufacturing processes, machine tools, fixtures and datum surfaces, the sequence of operations, inspection procedures, determination of tolerances and cutting conditions, and the calculation of total processing time. These detailed instructions to transform the raw material into the finished product are documented on the process sheet (also termed as operation sheet, planning sheet or route sheet or route plan or part program or process plan). Different types of data related to product design, material, equipment, and quality are the input to process planning function and process plan is the output, as presented in Figure 1.1. Thus, process planning is an engineering activity and process plan is the outcome of it in the form of documentation of the manufacturing instructions.
The process planning influences the cost of production as well as the time to market. A process planner strives to produce the optimal process plan by considering each production activity and parameters to satisfy the desired criteria of production cost, time, and quality. Therefore, he must possess rich manufacturing knowledge and experience to comprehend the engineering drawing, bills of material, and machining equipment. Thus, process planning plays a key role in gaining competitive advantage.
The process planning can be categorised as “macro process planning” and “micro process planning”. The former includes the analysis of availability and accessibility of machining processes and manufacturing features, selection of machine tool and process, selection of operation sequences and setup planning, whereas the micro process planning involves the determination of cutting conditions, process optimisation, analysis of machining performance, optimisation of tool path, and trade-off amid part-process-fixture design.

FIGURE 1.1
Basic model of process planning.
Basic model of process planning.
The function of process planning can be extended up to the customer end if it involves transportation, packaging, metrology, and export activities of the final product. This inclusion makes the process planning function a much more complex task rather than being just a manufacturing recipe. In general, these are routine activities and are performed by creative and skilled experts. Hence, the process planning is a team activity that involves specialists from different domains, such as jigs and fixture designer, tool designer, cutting condition experts, and process planner, etc. A good process plan is the output of multiparty cooperation and effective information exchange among dedicated subsystems.
1.3 Classification of Process Planning
The process planning can be categorised as manual process planning and computer-aided process planning.
1.3.1 Manual Process Planning
Basically, manual process planning has been perceived as a traditional and a workbook approach. The former approach involves the study of the blueprint (of part design specification) and manual of machine tool and equipment to determine the suitable processes, machine, jig fixture, material and tools for the selected part, to form the routing sheet. In the workbook approach, process planner identifies the required manufacturing processes and uses the standardised sequence of operations from a canned workbook (for a class of product) to form the operation sheet. The manual process planning approaches need a skilled team of the planner. Also, it is a time-consuming method and lacks consistency to dynamically update the process plan for a fresh product.
1.3.2 Computer-aided Process Planning (CAPP)
CAPP can be defined as automation of process planning through the computer support and cutting-edge planning approaches [based on group technology (GT) and exact mathematical principles] to set up the fast information exchange amid design and manufacturing activities and to generate the viable process plans readily. It works as a channel amid the manufacturing and design departments in a computer-integrated manufacturing environment. CAPP can generate the feasible process plans considering various factors like manufacturing lead time, cost and volume of production, availability of machines and equipment, alternative material, and process routing, etc. In the last two decades, several CAPP systems have been established on the bases of variant approach, generative approach, and semi-generative approach to perform the process planning activity.
1.3.2.1 Variant CAPP Approach
Here, an existing process plan is edited to make it suitable for a fresh product. It works on the idea of GT. Basically, it follows two stages, namely, the “preparatory stage” and the “production stage”. In the former, the coding scheme and part family are designed, which is followed by the generation of standard process plans. At the production stage, the standard process plan is retrieved and modified to form a generic process plan for a new part. In fact, the part families and the classification schemes of GT are formed according to the similarities in terms of design features and manufacturing processes used to machine the parts.
Wolfe (1985) developed MAYCAPP variant CAPP system using FORTRAN programming language and it works based on DCCLASS coding characteristics. Tulkoff (1987) built CUTPLAN for rotational and prismatic parts for process determination only. CAPP-I, TOJICAP, WICAPP, CAM-I CAPP, MIPLAN, MITURN, MIAPP, ACUDATA SAPT, and many more are the variant CAPP systems developed based on GT. All the variant CAPP systems lack the ability of generating the process plan for an exclusively new product. Also, this approach requires human expertise to intervene for retrieving and editing of the existing standard process plan, which leads to poor quality of the process plan.
1.3.2.2 Generative CAPP Approach
This is a fully automatic approach to generate process plans for a new part automatically by gathering process information from scratch. The process-planning knowledge is applied to a generative CAPP system using process logics like decision trees and tables and cons...
Table of contents
- Cover
- Half Title
- Series Page
- Title Page
- Copyright Page
- Table of Contents
- Preface
- Editors
- Contributors
- 1. Integration of Process Planning and Scheduling: Introduction
- 2. Approaches to Integrate Process Planning and Scheduling
- 3. A Case Study on Optimisation of Integrated Process Planning and Scheduling Functions Using Simulation-Based Genetic Algorithm and Heuristic for Makespan Performance Measurement
- 4. An Approach to Integrated Process Planning and Scheduling Based on Variable Neighbourhood Search
- 5. Integration of Process Planning and Scheduling in an Energy-Efficient Flexible Job Shop: A Hybrid Moth Flame Evolutionary Algorithm
- 6. Integration of Scheduling and Process Planning in Shop Floor: A Probability Model-Based Approach
- 7. Integrated Process Planning and Scheduling Using Dynamic Approach
- 8. Due-Date Agreement in Integrated Process Planning and Scheduling Environment Using Common Meta-Heuristics
- 9. Integration of Process Planning and Scheduling: An Approach Based on Ant Lion Optimisation Algorithm
- 10. A Review on Testbed Problems for Integration of Process Planning and Scheduling
- Index