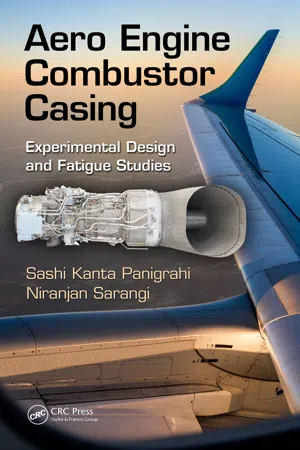
eBook - ePub
Aero Engine Combustor Casing
Experimental Design and Fatigue Studies
This is a test
- 156 pages
- English
- ePUB (mobile friendly)
- Available on iOS & Android
eBook - ePub
Aero Engine Combustor Casing
Experimental Design and Fatigue Studies
Book details
Book preview
Table of contents
Citations
About This Book
The book is focused on theoretical and experimental investigation aimed at detecting and selecting proper information related to the fundamental aspect of combustion casing design, performance and life evaluation parameters. A rational approach has been adopted to the analysis domain underlying the complexities of the process.
Frequently asked questions
At the moment all of our mobile-responsive ePub books are available to download via the app. Most of our PDFs are also available to download and we're working on making the final remaining ones downloadable now. Learn more here.
Both plans give you full access to the library and all of Perlegoâs features. The only differences are the price and subscription period: With the annual plan youâll save around 30% compared to 12 months on the monthly plan.
We are an online textbook subscription service, where you can get access to an entire online library for less than the price of a single book per month. With over 1 million books across 1000+ topics, weâve got you covered! Learn more here.
Look out for the read-aloud symbol on your next book to see if you can listen to it. The read-aloud tool reads text aloud for you, highlighting the text as it is being read. You can pause it, speed it up and slow it down. Learn more here.
Yes, you can access Aero Engine Combustor Casing by Sashi Kanta Panigrahi, Niranjan Sarangi in PDF and/or ePUB format, as well as other popular books in Technology & Engineering & Civil Engineering. We have over one million books available in our catalogue for you to explore.
Information
1
Introduction
1.1Background and Motivation
The main objective of an aero gas turbine engine is to provide thrust. To perform this duty, the engine must meet weight and efficiency targets. Of the thousands of parts comprising an aircraft gas turbine engine, the most critical parts that have the most significant effect on thrust are the rotating components and the high-pressure casings, such as the combustor casing. The first step in the process of establishing and minimizing the risk of failure of aircraft engines is to perform a failure mode and effect analysis to identify the possible consequences of failure of an individual part and of multiple failures in service. From this analysis, the components are categorized as âcriticalâ or ânoncriticalâ depending on the consequences of their failure.
The combustor casing is classified as one of the most critical components as it experiences the highest pressure in the aero engine and its failure can have catastrophic effects, resulting in the destruction of the engine due to uncontained fire from the flame tube. Therefore, the combustor casing should be designed with utmost care and include various design features such as circumferential welds, adaptors, and bosses for the ignitor, customer bleed, pressure probes, atomizers, and boroscope ports, and so on. Mounting of these bosses by welding over the double-curvature casing surface acts as stress raisers and reduces the strength and fatigue life of the component.
For any critical aero engine component, it is a mandatory requirement that the component must demonstrate its strength and fatigue life in a simulated engine environment before being declared fit for use in the engine. To meet this requirement, a full-scale prototype of the component needs to be tested in a test facility designed to simulate the engine environment. Development of the test facility to test the component in the engine environment is a challenging task. The necessary adaptors are designed to adapt the component suitably in the test facility and to apply the load that the component experiences in the engine. Being a highly critical component, a combustorâs design validation test is undertaken to meet the airworthiness requirement of the engine. The primary motivation of this book is derived from this requirement.
This book aims at providing an expansive framework for evaluation of the fatigue life of a full-scale model of an aero engine combustor casing, identifying critical parameters affecting its life, and recommending suitable design modifications for life improvement. The importance of the structural test of a critical component such as a combustor casing is outlined in Figure 1.1.

FIGURE 1.1
Importance of structural tests in an aero engine development cycle.
Importance of structural tests in an aero engine development cycle.
1.2Outline of this Book
Figure 1.2 outlines the important sections of the research work that constitute this book. The details of the research, implementation of the outcomes, and their demonstrations are presented in eight chapters. In order to provide an easier and streamlined reading of this book, each chapter is written as an independent paper that presents an introduction, methodology, test details (if any), and conclusions.
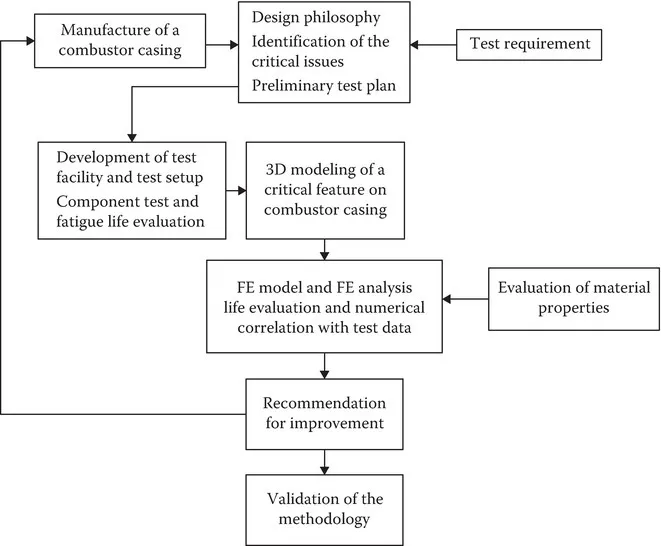
FIGURE 1.2
Outline of this book.
Outline of this book.
After this introductory chapter, which presents the development sequences of aero engines and aero engine combustion chambers, followed by the significant contributions made in this study, Chapter 2 provides the fatigue design philosophy of an aero engine combustor casing, covering the research work carried out in the fields related to the present publication, the theoretical and experimental details of fatigue life evaluation of a combustor casing, and offering an overview of life evaluation methodologies and relevant technical literature.
Chapter 3 provides the details pertaining to the development of a novel servo hydraulic pressure test rig to carry out the fatigue test on the combustor casing. Design and manufacture of the adaptors and the test setup required to assemble the combustor casing in the test facility are also highlighted in this chapter.
Chapter 4 presents the manufacturing details of an aero engine combustor casing and its experimental evaluation by conducting a cyclic pressure test is explained. When the component failed prematurely, it emphasized the need to focus on the critical design feature that led to its failure. This chapter emphasizes the methodology followed to identify the material properties, the numerical analysis of the combustor casing, and the critical feature using the finite element method and the life evaluation methodology. This information was correlated with the values obtained during testing in order to recommend design and manufacturing modifications of the component.
In accordance with the recommendations in Chapter 4, a modified combustor casing was manufactured by machining forging forged billet. The details of this manufacturing process are explained in Chapter 5. In addition to this, the instrumentation details carried out on this new modified component are explained. This chapter explains the assembly procedure and details of the fatigue life test carried out on the modified combustor casing. The component successfully demonstrated its intended life.
Chapter 6 presents a novel approach to conducting the proof pressure test on the modified combustor casing to ensure its overpressure capability during its operation. The component withstood the proof pressure, which is double the maximum operating pressure applied during the cyclic pressure test.
To enhance the study further, it was planned to evaluate the effect of fatigue on the proof strength of the combustor casing by applying proof pressure on a fatigue loaded combustor casing. The study indicates that proof strength is affected by fatigue. Details of this study are presented in Chapter 7.
Chapter 8 presents a comprehensive summary emphasizing the major achievements, experimental results, and the conclusions drawn.
1.3Initial Phase of Aero Engine Development
During the period between the two World Wars, the design of aircraft engines improved dramatically and made possible unprecedented progress in aircraft design. Engine development in those daysâand, to a large extent, even todayâis a very laborious process. The detailed process of building an engine, running it to destruction, analyzing what failed, and redesigning the necessary parts is a repetitive process. No product ever comes to market without a number of engineers having spent many hours perfecting that product. This is especially true for aircraft engines which, by their very nature, push all the limits of ingenuity, materials, and manufacturing processes.
Since the late 1930s, enormous achievements have been witnessed in the field of aero engines, covering technology, design, and manufacture, advancing the state of the art not only for gas turbines, but also for many related industries and products. Gas turbine technology continues to be at the forefront of mechanical and aero technologies, materials and coatings, and production and manufacturing science. The efforts of some of the worldâs most successful corporations and most respected engineers have placed this ind...
Table of contents
- Cover
- Halftitle Page
- Title Page
- Copyright Page
- Dedication
- Contents
- Preface
- Authors
- 1. Introduction
- 2. Fatigue Design Philosophy of an Aero Engine Combustor Casing
- 3. Development of Test Facility and Test Setup
- 4. Manufacturing of an Aero Engine Combustor Casing, the Experimental Evaluation of Its Fatigue Life, and Correlation with Numerical Results
- 5. Reassessment of Fatigue Life of the Modified Combustor Casing
- 6. Safety Test on Modified Combustor Casing
- 7. Effect of Fatigue on the Proof Strength of an Aero Engine Combustor Casing
- 8. Conclusions
- References
- Index