
eBook - ePub
Advances in Welding Technologies for Process Development
This is a test
- 289 pages
- English
- ePUB (mobile friendly)
- Available on iOS & Android
eBook - ePub
Advances in Welding Technologies for Process Development
Book details
Book preview
Table of contents
Citations
About This Book
Within manufacturing, welding is by far the most widely used fabrication method used for production, leading to a rise in research and development activities pertaining to the welding and joining of different, similar, and dissimilar combinations of the metals. This book addresses recent advances in various welding processes across the domain, including arc welding and solid-state welding process, as well as experimental processes. The content is structured to update readers about the working principle, predicaments in existing process, innovations to overcome these problems, and direct industrial and practical applications.
Key Features:
-
- Describes recent developments in welding technology, engineering, and science
-
- Discusses advanced computational techniques for procedure development
-
- Reviews recent trends of implementing DOE and meta-heuristics optimization techniques for setting accurate parameters
-
- Addresses related theoretical, practical, and industrial aspects
-
- Includes all the aspects of welding, such as arc welding, solid state welding, and weld overlay
Frequently asked questions
At the moment all of our mobile-responsive ePub books are available to download via the app. Most of our PDFs are also available to download and we're working on making the final remaining ones downloadable now. Learn more here.
Both plans give you full access to the library and all of Perlegoâs features. The only differences are the price and subscription period: With the annual plan youâll save around 30% compared to 12 months on the monthly plan.
We are an online textbook subscription service, where you can get access to an entire online library for less than the price of a single book per month. With over 1 million books across 1000+ topics, weâve got you covered! Learn more here.
Look out for the read-aloud symbol on your next book to see if you can listen to it. The read-aloud tool reads text aloud for you, highlighting the text as it is being read. You can pause it, speed it up and slow it down. Learn more here.
Yes, you can access Advances in Welding Technologies for Process Development by Jaykumar Vora,Vishvesh J. Badheka in PDF and/or ePUB format, as well as other popular books in Technology & Engineering & Chemical & Biochemical Engineering. We have over one million books available in our catalogue for you to explore.
Information
1
Multiple-Wire Welding GMAW and SAW
Syed Quadir Moinuddin and Abhay Sharma
Indian Institute of Technology Hyderabad
CONTENTS
1.1 Introduction
1.2 Background
1.3 Multiple-Wire Technology
1.3.1 Twin-Wire Welding
1.3.2 Welding with Three or More Wires
1.4 Recent Advancements in Multiple-Wire Technology
1.4.1 Tandem GMA
1.4.2 Power Source Synchronization
1.4.3 TIME-Twin
1.4.4 Double-Electrode GMAW and SAW
1.4.5 Twin-Wire Indirect Arc Welding
1.4.6 Cable-Type Welding Wire Arc Welding
1.4.7 Metal Powered-Assisted Multiple-Wire Welding
1.5 Recent Trends in Research in Multiple-Wire Welding
1.6 Conclusions
References
1.1 Introduction
Welding is a well-established joining technique used in industries for various applications. This technique is classified based on various factors such as use or no use of filler wire, fusion or solid-state welding, and shielding medium (gas or flux) (Eisenhauer 1998). The fusion welding is the most frequently used process wherein an electric arc is generated between a workpiece and an electrode. The resulting arc heat is used to melt the electrode wire and the material. The submerged arc-welding (SAW) and gas metal arc-welding (GMAW) processes are widely used in industries because of higher deposition rates and economic efficiency. In the past few decades, a significant advancement in both the processes has taken place. The requirement of deposition and production rates at the shop floor is quite higher than what is possible with single-wire welding. In order to overcome these limitations, research is being conducted on existing technologies and materials as well as on new materials and technologies. The multiple-wire welding is one of such techniques that came into existence to increase the productivity. This process finds application where a high deposition rate without deep penetration is beneficial. Heavy corner welds, surfacing deposits, and different butt and fillet welds, where fit-up or melt-thru is critical, are some of the examples. Initial applications were focused on twin-wire welding and later with the help of advancements in torch configuration (triple-wire, four-wire, and six-wire) and power source, where several wires were connected to single or individual power sources. Various techniques have been developed for faster deposition: twin-wire welding, tandem welding, transferred ionized molten energy (TIME), double-electrode indirect arc welding, cable-type welding, etc. The difference between twin-wire and tandem welding is based on contact tube arrangement, i.e., common contact tube is used in twin-wire, whereas separate contact tubes are used in single or different torch/s in tandem welding. The double-electrode process consists of two torches: a main torch and a bypass torch. The bypass torch is used to provide additional melting without affecting the base metal, thus increasing the deposition rate. Indirect arc-welding process redistributes the energy between the wires, and the base plate is independent of the current circuit. The arc burns between the wires and increases the deposition rate. In the cable-type welding process, the wires are twisted around the center. In this process, arc rotation phenomenon causes an increase in deposition rate and reduces the arc pressure forming shallow molten pool. A considerable progressâacademic and industrialâin the past decade has taken place in multiple-wire welding, which needs consolidation for the use of practitioners and researchers. The current chapter presents the recent developments in multiple-wire welding from the technology and research perspectives.
1.2 Background
The idea of multiple-wire welding in the form of twin-wire welding was first proposed by Ashton (1954). The references of multi-wire welding can be found in the earlier works of the 1950s and 1960s (Mandelberg and Lopata 1966; Uttrachi 1966). The interest in this technology started to grow in the 1980s with the initiation of the shop-floor application of the process. Thereafter, several developments have been reported (Chandel 1990; Tusek and Suban 2003; Sharma et al. 2008a,b, 2009aâc, 2015; Shi et al. 2014a; Yu et al. 2016). The initial research studies were mainly related to process establishment and feasibility. With the development of advanced power sources and modeling and simulation techniques, the research interest has grown in topics like melting rate (Tusek 2000), heat transfer, fluid flow modeling (Sharma et al. 2005a,b), etc. In the late 20th century, the idea of the multiple-wire was first applied in the GMAW process by Lassaline et al. (1989). Thereafter, twin and tandem wire with the GMAW was also reported (Suga et al. 1997; Michie et al. 1999). In the past decade, research interest in multiple-wire GMAW has grown due to the availability of advanced power sources that provide precise control and modulation of the welding arc (Scotti et al. 2006; Chen et al. 2016; Moinuddin et al. 2016; Ueyama et al. 2005b; Reis et al. 2015). The multiple-wire welding is expected to make a significant impact in the coming time that necessitates a consolidation of existing technologies and future possibilities. In order to understand the process, the following section briefs about the multiple-wire welding technique followed by the recent developments.
1.3 Multiple-Wire Technology
The multiple-wire welding uses more than one electrode (wires in the case of consumable arc welding), in which the electrodes travel simultaneously with the same or different feed rates through a joint contact tube. The wires may have a joint or individual feed rate control based on the application of one or more power sources. The wires in the contact nozzle can be arranged in parallel, series, or to form an optional shape (e.g., triangle) with regard to the welding direction (Tusek and Suban 2003). The multiple-wire operations cover the following three techniques:
- Multiple Electrodes, Parallel Power: In this system, multiple electrodes are connected with the same power source.
- Two Electrodes, Series Power: In this system, each electrode operates independently and remains isolated to each other. Each electrode possesses a feed motor and a voltage control. The power supply cable is connected to one welding head, and the return cable is connected to the second welding head instead of the workpiece.
- Multiple Electrodes, Multiple Powers: In this system, two or more electrodes are connected to individual power sources. The electrodes are separately connected to AC or DC power sources.
A classification, specifically for multi-wire GMAW/SAW, based on power source arrangement and contact tip configuration (Blackman et al. 2002) is suggested as given in Table 1.1.
TABLE 1.1
Classification of Multi-Wire for GMAW/SAW Systems
Classification of Multi-Wire for GMAW/SAW Systems
Description Power | Wire Feeding Unit | Contact Tip Configuration | Transfer Modes |
Twin-wire with single power source | A single-wire feed unit modified to feed two wires | A single common potential contact tip | Pulsed |
Twin-wire with two power sources | Two-wire feed units that feed two wires | A single common potential contact tip | Pulsed |
Asynchronous tandem | Two-wire feed units that are not directly synchronized | Two electrically isolated contact tips | Dip, pulsed, spray |
Synchronized tandem | Two-wire feed units with synchronized directly | Two electrically isolated contact tips | Dip, pulsed, spray |
In view of the significant developments in the past few years, a comprehensive classification of multiple-wire welding based on the torch, contact tube, power sources, polarity, and welding directions is shown in Figure 1.1.
In multiple-wire welding, the wire arrangement within the contact tube and welding direction play important roles. In the case of wire in series, the first wire melts the parent metal. The weld pool thus produced stays behind the first arc due to high welding velocity and rearward motion of weld metal. The remaining wire/s, traveling behind the first one, shape/s the weld. The first wire, due to lower resistance, conducts a higher current than the other wires (Tusek and Suban 2003). Apart from this, the process parametersâwelding current, voltage, wire diameter, the distance between two wires, contact tube-to-work piece distance (CTWD), welding speed, shielding gas, flux height, etc.âplay a vital role.
1.3.1 Twin-Wire Welding
The twin-wire welding is the most investigated and frequently used variant of the multiple-wire technology. The term âtwin-wireâ, or sometimes âtwin-electrodeâ, is characterized by a twin bore contact tube (as shown in Figure 1.2), in which two wires are fed through a single welding torch into a common weld pool (Tusek 2000).
In some of the earlier references like Mandelberg and Lopata (1966), a two-wire and two-power source type of system is described as the twin-wire welding process. In due course of time, a clear definition emerged for twin-wire welding. As categorically mentioned by Hinkel and Frosthoefel (1976), âTwin-electrode SAW, for those who are not familiar with the system, differs significantly from tandem arc welding, but only slightly from the single arc operation.â Instead of feeding one electrode, the feeder is equipped with a double set of drive rolls and guides so that two electrodes can be fed simultaneously at the same feed rate. Both of these electrodes are normally fed through a common contact tip or set of jaws, so that the current from the power source splits between the two electrodes. Thus, a clear definition for twin-electrode welding, now more-often termed as âtwin-wire weldingâ, clearly exists. Furthermore, the process with two electrodes with individual power sources, where one electrode is following the other, is termed as tandem welding.

FIGURE 1.1
Classification of multiple-wire welding (Tusek and Suban 2003). (With kind permission from Elsevier.)
Classification of multiple-wire welding (Tusek and Suban 2003). (With kind permission from Elsevier.)

FIGURE 1.2
Schematic diagram of twin-wire welding (Sharma et al. 2008a,b). (With kind permission from Springer.)
Schematic diagram of twin-wire welding (Sharma et al. 2008a,b). (With kind permission from Springer.)
In twin-wire welding, the two wires are positioned in-line or at any angle across the seam with a single or multiple power sources. Figures 1.3 and 1.4 show the schematic diagrams of twin-wire systems connected to a single power source with possible welding directions and with an individual power source for GMAW and SAW processes, respectively. When both the wires remain on the same polarity, arcs attract each other and in some ways act like a single elongated arc. In the case of wires arranged in tandem (i.e., one after another), due to mutual interaction, arc at lead wire is subject to rearward blow, whereas arc at the trail wire experiences forward blow. In this type of arrangement, trail arc controls the final welding shape; the forward deflection allows the use of higher welding speed before encountering weld undercut (Uttrachi 1966).
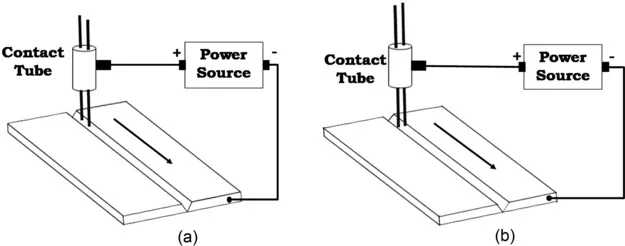
FIGURE ...
Table of contents
- Cover
- Half Title
- Title Page
- Copyright Page
- Table of Contents
- Preface
- Foreword
- Acknowledgments
- Editors
- Contributors
- 1. Multiple-Wire Welding GMAW and SAW
- 2. Regulated Metal Deposition (RMDâ˘) Technique for Welding Applications: An Advanced Gas Metal Arc Welding Process
- 3. Friction Stir Welding and Its Variants
- 4. Different Methodologies for the Parametric Optimization of Welding Processes
- 5. Additive Manufacturing with Welding
- 6. Cares to Deal with Heat Input in Arc Welding: Applications and Modeling
- 7. Friction Stir Welding of High-Strength Steels
- 8. Friction Stir Spot Welding of Similar and Dissimilar Nonferrous Alloys
- 9. Linear Friction Welding
- 10. Joining of Dissimilar Materials Using Friction Welding
- 11. Insights into the Flux-Assisted TIG Welding Processes
- 12. Friction Stir Welding of Aluminum Alloy: Principle, Processing, and Safety
- Index