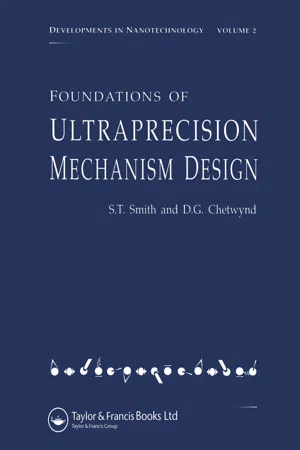
This is a test
- 364 pages
- English
- ePUB (mobile friendly)
- Available on iOS & Android
eBook - ePub
Foundations of Ultra-Precision Mechanism Design
Book details
Book preview
Table of contents
Citations
About This Book
The realm of ultra precision mechanisms, for example in controlling motion to small fractions of a micrometer, is encroaching into many fields of technology. This book aims to provide a bridge for those moving from either an engineering or physics background towards the challenges offered by ultraprecision mechanisms. Using case study examples, this book provides a guide to basic techniques and gives technical, analytical and practical information.
Frequently asked questions
At the moment all of our mobile-responsive ePub books are available to download via the app. Most of our PDFs are also available to download and we're working on making the final remaining ones downloadable now. Learn more here.
Both plans give you full access to the library and all of Perlego’s features. The only differences are the price and subscription period: With the annual plan you’ll save around 30% compared to 12 months on the monthly plan.
We are an online textbook subscription service, where you can get access to an entire online library for less than the price of a single book per month. With over 1 million books across 1000+ topics, we’ve got you covered! Learn more here.
Look out for the read-aloud symbol on your next book to see if you can listen to it. The read-aloud tool reads text aloud for you, highlighting the text as it is being read. You can pause it, speed it up and slow it down. Learn more here.
Yes, you can access Foundations of Ultra-Precision Mechanism Design by Stuart T. Smith in PDF and/or ePUB format, as well as other popular books in Technology & Engineering & Mechanical Engineering. We have over one million books available in our catalogue for you to explore.
Information
1 Introduction
The concept of ultraprecision engineering is illustrated through the scale of some typical processes that might be considered in this context. Technological examples are compared with similarly scaled biological systems in order to demonstrate both the fundamental nature of engineering at this scale and its relationship with nanotechnology. This chapter also provides a convenient place to clarify terminology that will be used throughout this book, by means of a brief review of common instrumentation terms and the nature of accuracy and errors.
1.1 The scale of ultraprecision
An engineering perspective on precision manufacture necessarily looks to a continuing refinement of machining and processing techniques for the overall improvement of products. The initial drive for high precision is firmly rooted in the industrial revolution and exemplified in such names as Henry Maudslay, Joseph Bramah and Joseph Whitworth in the UK and Eli Whitney, Simeon North and Samuel Colt in the USA. In the intervening century and a half the precision of conventional machine tools has improved by orders of magnitude. Today, some types of components can be produced on a routine basis with a precision (ratio of dimension to tolerance) of one part in 100,000 or more. This is an improvement of perhaps as much as one thousand from those early beginnings. Of course, Maudslay and Whitworth were building measuring machines of much better precision, but their methods were hardly routine. Also their work demonstrates the case that improved metrology instruments precede similar improvements in machine tools. Hume, 1980, provides a good review of the early development of modern precision engineering from this perspective.
By comparison with the rates of some other technological advances this is meagre fare. Advances have been consistently impeded by important barriers to ever increasing precision in mechanical manufacture. Working at high levels of precision requires the greatest care in mechanical design perhaps including the use of concepts not hitherto conceived of in normal engineering practice. The implementation of a novel design idea might wait upon the development of a material having sufficiently well controlled properties. As tolerances or artefact dimensions reduce further, it ceases to be safe to assume that bulk properties remain true and a completely new range of challenges appear. In order to emphasise the present range of demands, consider the logarithmic scale bar shown in Figure 1.1. Below the scale bar are examples drawn from biology. The fly is a familiar and tangible object and the human egg, the largest human cell at a fraction of a millimetre, is still of sufficient size to be visible to the naked eye. When we move to the size of typical cells, of the order of thousandths of a millimetre (that is a few micrometres*) it becomes increasingly difficult to discriminate objects either visually or by touch. Around this point we reach the limit of accuracy in most engineering workshop practices. At the micrometre level we are totally reliant on the use of measuring instruments to detect the presence of material or motions. Consequently the boundary between conventional and precision engineering is often considered to occur where tolerances to better than a few micrometres are specified.
Below one micrometre we start to discover major limitations to the traditional methods of measurement. Hand tools such as micrometers become more difficult to produce with such precision and, anyway, the human hand becomes rather clumsy. Laboratory microscopes are limited in lateral resolution by the wavelength of visible light. Materials related effects such as thermal expansion and deformation under small loads can totally invalidate measurements. Yet it is at the 0.1 μm level that microelectronic fabrication processes must perform on a routine basis. Reducing further to tens of nanometres, the scale of viruses and larger molecular structures, we move towards the limits of performance of some of the most powerful tools for measurement and manipulation. Scanning electron microscopes (SEMs), optical polishing machines and diffraction grating ruling engines all tend to become ineffectual at around 10 nm resolution. Nevertheless, there are numerous examples of everyday, mass produced engineering components which require tolerances at this level. Examples include gauge blocks, diesel fuel injectors and similar hydraulic components, spindles for high speed bearings and video recording heads, magnetic reading heads, force probes, optical lenses and moulds for plastic lenses.
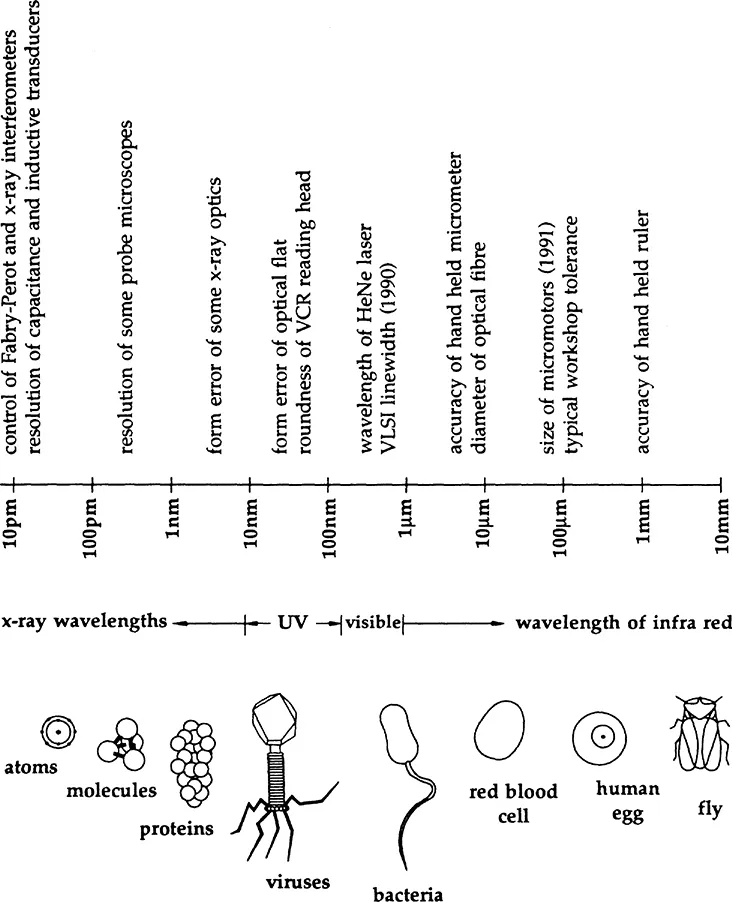
Figure 1.1 Scale bar showing the relative sizes of many familiar and unfamiliar systems
Except for a few special cases, it is difficult to envisage conventional approaches coping with such levels of precision, yet, as pointed out by Richard Feynman, 1961, there is still plenty of room at the bottom. Perhaps it is better to abandon traditional engineering methods and return to its roots in the basic models of physics, designing and manipulating from the atomic level upwards. This is the approach identified by some authorities as that of ‘Nanotechnology’, although we prefer the wider view that it should contain the best of both approaches in successfully addressing precisions in the 0.1 to 100 nm region, Taniguchi, 1974. Whichever definition is preferred, the mechanical aspects of such endeavours are the clear domain of ultra-precision engineering.
Where exactly lies the limit of precision for engineering applications? If we consider that an artefact must be produced, then the atomic dimension provides a limit on physical size and dimensional tolerance. However, to manipulate at the atomic level requires measurement and control of displacements to between a tenth and a hundredth of that limit. As will be seen, there are some jobs that need even crazier displacement sensitivities. The crystal radius of the carbon C4+ ion is around 0.15 nm, Pauling, 1945. Bonding together a few carbon, oxygen, hydrogen and nitrogen atoms results in amino acid molecules that are around a nanometre in length and which combine to form the basic proteins. In this region of size we find the tolerances for x-ray optics and the layer structures of electronic and optoelectronic devices. Increasing in dimension by an order of magnitude we are back at the scale of virus structures, (which some consider as equivalent to nanotechnological machines), and at the tolerance to which video recording heads and many other practical engineering components must be manufactured. Also around this level brittle materials often exhibit ductile behaviour; boundary lubrication film thickness is normally to be found; errors in diffraction gratings and optical cavity interferometers can seriously affect performance; and surface roughness begins to affect the reflectivity of a surface. Another order of magnitude increase to a few hundred nanometres sees conventional manufacturing techniques becoming feasible, Franse, 1990.
At the (sub-) nanometre level mechanical operations such as moving, machining and joining will be indistinguishable from the processes of chemistry and biology. The excitement of nanotechnology is that it is a unique engineering discipline that promises to have applications in all areas of science and industry. Engineering tools are rapidly being developed to fulfil the desire to operate routinely at this level. Seminal to their development was the invention of probe microscopy by Russell Young in 1972. His concept has since developed into a more generalized field of probe microscopy, in particular by Binnig et al., 1982 and 1986. These techniques regularly demonstrate subnanometre measurement resolution and under specific conditions are capable of achieving atomic scale surface modifications, Miller and Hocken, 1990. Several types of sensor and actuator used in engineering instrumentation appear capable of resolutions best expressed in picometres. Some complete instrument structures, and by no means all of them esoteric research tools, need sub-atomic positional stability. Two such are Fabry-Perot etalons and x-ray interferometers – both of which require control at the picometre level if they are to operate as well as is desired, Hicks et al., 1984, Bowen et al., 1990.
Ultraprecision engineering includes the discipline of scientific instrument making and it is from this that many of our examples are taken. This book is concerned with the design of mechanical mechanisms that can operate with tolerances within the nanometre or sub-nanometre regime. The same approaches may often profitably be used when somewhat less stringent tolerances will suffice.
There is a balance between analysis and explanations of why designs have evolved in the way that they have so that past lessons may be related to future designs. The techniques to be explored are relevant not only to the direct control of microdisplacements but also to any field where dimensional stability is needed; machines that incorporate the likes of force actuators, microdevices, balances and various probes in which nanometre level distortions or disturbances may lead to significant errors.
This book discusses both instruments and machines. The former is considered to be a device or system that is design...
Table of contents
- Cover
- Half Title
- Title Page
- Copyright Page
- Table of Contents
- INTRODUCTION TO THE SERIES
- PREFACE
- Chapter 1 Introduction
- Chapter 2 Introductory Mechanics
- Chapter 3 Fundamental Concepts in Precision Design
- Chapter 4 Flexure Design For Positioning And Control
- Chapter 5 Drive Couplings and the Mechanics of Contact
- Chapter 6 Lever Mechanisms of High Resolution
- Chapter 7 Actuators and Sensors for Controlled Displacements
- Chapter 8 Materials Selection in Precision Mechanical Design
- Chapter 9 Slideways for Long Range Precision Motion
- Chapter 10 The Dynamics of Instrumentation Mechanisms
- APPENDIX A Airy point mounting of datum bars
- AUTHOR INDEX
- SUBJECT INDEX