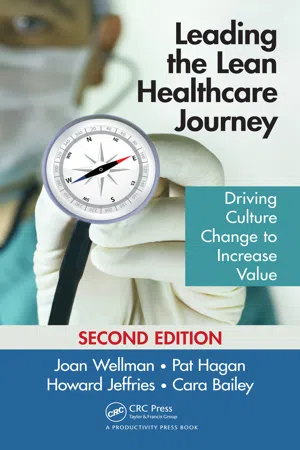
eBook - ePub
Leading the Lean Healthcare Journey
Driving Culture Change to Increase Value, Second Edition
This is a test
- 299 pages
- English
- ePUB (mobile friendly)
- Available on iOS & Android
eBook - ePub
Leading the Lean Healthcare Journey
Driving Culture Change to Increase Value, Second Edition
Book details
Book preview
Table of contents
Citations
About This Book
This book reveals and describes the leadership and culture change required to remove waste from healthcare processes and eliminate the root cause of soaring costs, poor quality and safety, and limited access. The book's delivery strategy revolves around personal and organizational stories and case studies told by physician and administrative leaders, all students of the Toyota Production System. This revised edition uniquely blends updated case studies with practical theory to describe how the healthcare value proposition can be changed by reducing waste, variation and complexity in healthcare. New to the book are chapters on clinical standard work and integration of lean and safety.
Frequently asked questions
At the moment all of our mobile-responsive ePub books are available to download via the app. Most of our PDFs are also available to download and we're working on making the final remaining ones downloadable now. Learn more here.
Both plans give you full access to the library and all of Perlego’s features. The only differences are the price and subscription period: With the annual plan you’ll save around 30% compared to 12 months on the monthly plan.
We are an online textbook subscription service, where you can get access to an entire online library for less than the price of a single book per month. With over 1 million books across 1000+ topics, we’ve got you covered! Learn more here.
Look out for the read-aloud symbol on your next book to see if you can listen to it. The read-aloud tool reads text aloud for you, highlighting the text as it is being read. You can pause it, speed it up and slow it down. Learn more here.
Yes, you can access Leading the Lean Healthcare Journey by Joan Wellman, Pat Hagan, Howard Jeffries, Cara Bailey in PDF and/or ePUB format, as well as other popular books in Medicina & Salud pública, administración y atención. We have over one million books available in our catalogue for you to explore.
Information
Chapter 1
Introduction
This book is about people who have implemented dramatic change in their organizations by applying the principles and methods of the Toyota Production System (TPS) to healthcare. In this second edition there are new chapters by people who have adopted a Lean strategy since we last published, epilogues to first-edition chapters by people who have been on this journey for many years, as well as chapters that remain as written from the first edition. Each chapter tells how determined men and women have applied the principles of TPS to their work, innovating and leading their organizations forward. These people are improving the patient experience by reducing waste and thereby reducing costs—vitally important to all of us, given that our healthcare system currently consumes almost 20 percent of U.S. gross domestic product.
Each of these stories started with a healthcare leader who was curious enough to read about TPS (or “Lean”), participate in training, and visit manufacturing companies that have proven Lean track records. Curiosity and exposure to new ways of thinking helped these leaders understand that much of what we do in healthcare is waste “cleverly disguised as real work.” Curiosity also led them to understand that quality, cost, patient access, and safety are not mutually exclusive trade-offs but intersecting aims that can be improved concurrently if we are willing to learn from the likes of Toyota.
In our first edition of this book, we described the approach and lessons learned from some of the earliest healthcare organizations to apply TPS to their operations. Our focus, and theirs, was primarily on the “breakthrough” half of the Lean journey: the exciting initial forays in breakthrough improvements that often produce impressive results in waste reduction and staff engagement. However, we learned through experience that the gains that improvement teams struggle so hard to achieve can be easily lost. Five years later, chapters in this second edition address the need to couple breakthrough improvements with the other half of the Lean journey: the Lean management system (LMS). In 2010, we began organizing study trips to manufacturers steeped in LMS so that healthcare leaders could learn from the best. We observed leaders using LMS as a powerful means of focusing their organizations and achieving breakthrough levels of performance. We also observed a commitment to sustaining gains and ongoing, never-ending improvement through the rigor and discipline of LMS. These study trips made us realize that everyone in our organization, from executive leaders to those at the front lines of care, needed to embrace a new way of thinking and a new way of going about their work. No longer could Lean be a project-by-project activity with episodes of improvement. We had to all take on the responsibility for continuous, daily improvement, the cornerstone of LMS.
The stories that follow come from Seattle Children’s Hospital (SCH) and other organizations that have engaged Joan Wellman & Associates (JWA Consulting) as consultants over the last 15 years: The Everett Clinic in Everett, Washington; Nemours Children’s Health System in Florida and Delaware; and Seattle Cancer Care Alliance. These organizations vary widely in size and complexity from stand-alone hospitals (SCH) to multi-institutional systems (Nemours). These organizations also have very different physician models including a primarily academic model (Seattle Children’s Hospital), an employed physician model (Nemours), and a physician-owned model (Everett Clinic).
The case studies demonstrate that organizations can effectively apply Lean principles regardless of their size, physician model, or structure. These organizations use different words to describe their version of the Lean approach, but their strategies are grounded in the same enduring philosophy around which everyone in the healthcare enterprise can rally: focus on the patient, support your people in their work, and take a strategic, long-term view. Lean is about reducing waste to achieve the goals that increase value for the patient. These goals, which we refer to in shorthand as QCDSE, are to improve quality, decrease cost, improve delivery (patient access), improve safety, and increase engagement of all organization members in continuous improvement. These stories demonstrate how Lean can drive and sustain improvement in QCDSE.
Furthermore, the variety of stories offered in the second edition demonstrate that Lean applies everywhere in the healthcare enterprise, with the engagement of everyone, every day. If the Lean effort in your organization has been pigeonholed to “only operations” or “only patient flow,” with your colleagues thinking that Lean has little to do with the business office, or the work of caregivers or executives, take heart. This edition provides evidence that Lean is relevant everywhere in your institution. You’ll learn, for example:












Achieving outstanding results is anything but easy. You don’t have to read between the lines of these stories to realize how hard it is to change deeply ingrained behaviors that embed waste and thwart the delivery of compassionate, safe, patient-centered care. You’ll no doubt recognize the challenges as the authors describe their efforts to build and maintain a consensus for change in their organizations.
This book is not a “how to” improve healthcare book, or a recipe on how to run an operating room or intensive care unit more efficiently. It is a book about curiosity, humility, and the tenacity to challenge deeply held assumptions about how we deliver healthcare. Implicitly, the most fundamental assumption that this book challenges is that our country needs more money to operate an effective healthcare system. What we need most is great leaders who, like the chapter authors in this book, have the skill and tenacity to look critically at what they are doing and find better, less wasteful ways to provide safe, high-quality care.
Patrick Hagan
Amelia Island, Florida
Amelia Island, Florida
Joan Wellman
Seattle, Washington
Seattle, Washington
Chapter 2
The Continuous Performance Improvement (CPI) Journey: A Long and Winding Road
Our continuous performance improvement (CPI) journey has be...
Table of contents
- Cover
- Half Title
- Title
- Copyright
- Dedication
- Table of Contents
- Preface to the First Edition
- Preface to the Second Edition
- Acknowledgments
- About the Authors
- Contributors
- 1 Introduction
- 2 The Continuous Performance Improvement (CPI) Journey: A Long and Winding Road
- 3 Creating High-Powered Healthcare Improvement Engines
- 4 Leadership and Culture Change: What We Need Most We Can’t Buy
- 5 Strategy Deployment and Daily Management: Implementing a Lean Management System at Nemours
- 6 Leadership and Lean Transformation at Seattle Cancer Care Alliance: If We Knew Then What We Know Now
- 7 Transforming Doctors into Change Agents
- 8 Clinician Engagement: Continuous Performance Improvement (CPI) Applied in a Not-So-Touchy-Feely Environment
- 9 Asthma: Continuous Improvement (Kaizen) of Clinical Standard Work
- 10 Supply Chain: Ensuring Clinical Staff Have What They Need
- 11 Intensive Care Unit: Developing and Implementing Pull Systems
- 12 Patient Rounding: Delivering Compassionate Care through Clinical Standard Work
- 13 Change That Nourishes the Organization: Making the Total Parenteral Nutrition (TPN) Process Safer
- 14 Hand Hygiene at Seattle Children’s Hospital: A Call to Action
- 15 Balancing the Line in Outpatient Pharmacy
- 16 Rapid Changeover in the Operating Room
- 17 Lean in the Lab: No Culture Left Behind
- 18 Registration to Cash Value Stream: Making the Right Call at the Everett Clinic
- 19 Integrated Facility Design at Seattle Children’s Hospital
- Glossary
- Index