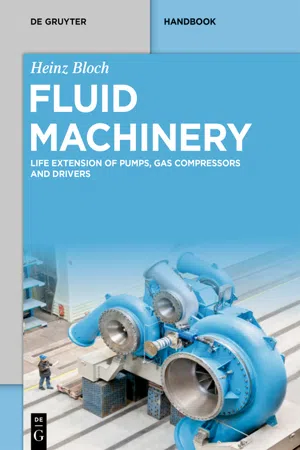
This is a test
- 208 pages
- English
- ePUB (mobile friendly)
- Available on iOS & Android
eBook - ePub
Book details
Book preview
Table of contents
Citations
About This Book
Fluid movers are extensively used in the process industries. New machines are specified, designed, manufactured and installed in a way that ensures their safety and reliability. Existing machines may be upgraded or retrofitted during maintenance or repair. This book describes how improved components and better lubricant application provisions, among other experience-based measures, can safely extend operating life and increase profitability.
Frequently asked questions
At the moment all of our mobile-responsive ePub books are available to download via the app. Most of our PDFs are also available to download and we're working on making the final remaining ones downloadable now. Learn more here.
Both plans give you full access to the library and all of Perlego’s features. The only differences are the price and subscription period: With the annual plan you’ll save around 30% compared to 12 months on the monthly plan.
We are an online textbook subscription service, where you can get access to an entire online library for less than the price of a single book per month. With over 1 million books across 1000+ topics, we’ve got you covered! Learn more here.
Look out for the read-aloud symbol on your next book to see if you can listen to it. The read-aloud tool reads text aloud for you, highlighting the text as it is being read. You can pause it, speed it up and slow it down. Learn more here.
Yes, you can access Fluid Machinery by Heinz Bloch in PDF and/or ePUB format, as well as other popular books in Biological Sciences & Science General. We have over one million books available in our catalogue for you to explore.
Information
Chapter 1 Why extending fluid machine life is still an essential pursuit
1.1 Upgrading vintage process machinery: the full picture
Ideally, the upgrading of pumps, compressors, steam turbines, and other fluid machines should start with improved component design. Improved components must be specified by the purchaser and the specification input must come from informed people. These are informed technical people whom we will identify as Reliability Professionals. There are also junior managers who play an important role, and there are, ultimately, senior managers whose approval must be sought.
Reliability Professionals act based on knowledge. Looking at accurate failure statistics points out components that had to be replaced or repaired more frequently than others. Quite obviously, these should be upgraded before they again find their way into a modern plant. In other words, these “weak links” should be designed-out before they find their way into new machines. However, for the most part, Reliability Professionals concern themselves with upgrading components in machines that have been in service for decades but have experienced above-average maintenance frequencies, cost outlays, or even repeat failure. Later in this book, we will discuss upgrades that, once made, were of immediate benefit. Some of these had perhaps been hidden from the eyes of the non-expert or were simply overshadowed by other priorities or experiences. Collectively, however, these upgrade events represent lessons learned. As these lessons were absorbed and evaluated, they showed how critically important machinery should be specified, designed, constructed, installed, commissioned, operated, and maintained.
The big payoff will materialize in specifying the next machine with upgraded components. A Reliability Professional must make the business case for the incremental cost of specifying, designing, fabricating, installing, and maintaining improved machines or improved parts. These professionals must teach, brief, and enlist junior managers who will seek the backing of senior managers or corporate heads without whose approval the brakes would be put on the figurative wheels of industry.
In the year 2020, refineries, petrochemical facilities, and other process plants are increasingly complex and equipment-intensive; some of these incorporate more than 100,000 assets. Suppose we are in the business of managing a processing plant, a department within the plant, or we just want to make a difference as individual technical persons, as Reliability Professionals. This clearly implies that we understand the importance of delivering value to our stakeholders for our own good – meaning our sense of self-worth, self-preservation, and for the good of our company. We would quickly realize that upgrading one critical piece of equipment may not always improve the bottom line if another critical piece of equipment in series with the one that was upgraded also has poor availability. Peeling away one layer at a time may be the best that we can do, but maximizing our use of the best available computerized technology is important. Doing so will greatly facilitate the process of managing data and information when time is of the essence. Indeed, time usually plays a hugely important role in delivering results. As we well know, time is money.
1.2 The path forward
The road ahead requires that we will have identified and will have made plans on what needs to be done and then to establish a priority listing. The listing becomes our schedule for going forward; our decisions on upgrading and sustaining equipment performance must have a goal. For lack of a better collective term, we call the goal “Operational Excellence” (or OE). Operational excellence might be used by others as a new and sweeping initiative, but for us it’s whatever maximizes long-term profits and safety. That said, it should be no surprise that each of our many upgrade decisions has as its singular and consistent objective the cost-justified maximizing of equipment availability. To be available for production, one must minimize the need for maintenance and eliminate or at least reduce, the risk of random failure.
We keep in mind that best-in-class facilities report on-stream factors of 95%. In many facilities, loss of production for just one single day can mean more than $2 million in lost profits. High rates of production equate to low unit cost of production, which explains the quest for optimizing equipment reliability. Our examples will make the point. See beyond them and, whenever possible, try to embrace the underlying principles.
1.3 Turning visions into actions
Turning visions into action requires knowledge. We cannot acquire the needed knowledge by listening to anecdotes, or by over-emphasizing on-the job training. We must read, we must acquire the ability to ask intelligent questions, and to act on facts, not opinions. Achieving high equipment reliability implies that we understand the condition of our equipment, the damage mechanisms and modes of failure, and the risk of continued operation without regard to early manifestations of deviations from normal. We must learn the details of applying the proper level of maintenance and scheduling of such maintenance.
Optimizing the expense in maintaining equipment requires the judicious stocking of spare parts. Sometimes the spare better be an upgraded part, a pre-engineered improved component, ready to be installed at the next opportunity. Therefore, spending our maintenance dollars in a way that drives the reliability and availability of equipment requires forethought. In other words, the next spare part should be an upgraded version which we designed, or which we specified to be different from the part that failed. We must view every maintenance intervention as an opportunity to upgrade if upgrading is both feasible and cost-justified. We justify the upgrade by estimating the enhanced safety of people and equipment. We realize that safety is directly influenced by equipment reliability, which is totally dependent on design, installation details, conscientious maintenance, and as-intended operation of the equipment. If we gain added safety in any of these areas, we will have improved the facility. It should be easier to make the business case for improved safety.
As we move toward meeting our upgrade objectives, we must spell out practices that translate our vision into action. The focus will remain on achieving operational excellence – creating a safe and profitable workplace. We will have to transform company cultures and mold individuals into organizations that support these objectives. Starting at the top levels of a company, there must be an active commitment toward achieving excellence. Our managers must be visionaries and leaders in fostering a supportive culture across all departments and having an organizational structure that can execute the work that needs to be done. And we must sometimes nudge them in that direction … … .
To make a vision materialize, we must maintain a work force that is highly trained, has the right tools, and is both skilled and motivated to achieve the desired results. Because the soul of a company is its people, the notion that one can always hire contractors or consultants is deeply flawed. Therefore, our hiring and retention practices must attract the best people. These people must have mentoring from both within and outside the company. They must be highly trained technically toward becoming the future leaders of the company and must develop the right skills in using the tools required in maintaining the facility. They must be given responsibility and be held accountable for results. Good performance must be recognized and rewarded to provide the motivation for continual success.
It follows that we always need to know the condition of our equipment. The figurative pinch points where allowing deviations from normal or anticipated conditions will cause unacceptable failure risk must be identified. Having the software tools to collect and analyze relevant equipment information and data is important. With these tools, one can gain or capture the knowledge needed for making smart business decisions; these are the decisions for upgrading and suitably maintaining one’s equipment. Computer technology has enabled industry to manage large amounts of data and information in support of the above objectives. But proving the cost-effectiveness of using the best available technology for design and upgrading of processing equipment will be needed. Reliability Professionals cannot wait for disasters to jolt them into action. Their main charter and roles are to describe what needs to be done to steer clear of accumulating deviations at a figurative pinch point. Deviations at pinch points will almost certainly lead to performance deficiencies and distress. Certain types of distress become disasters.
Being proactive is one of the overarching roles of Reliability Professionals. As they proactively seek out, cost-justify, and implement steps toward improving fluid machines, they will not simply go with the lowest bidder for parts, machines, contract services, and the like. Instead, these professionals support management by identifying the best assets or – in the case of contract service providers – the most qualified ones and let them demonstrate how, in the past, these contract service providers have gained the approval of their key clients. Never fall for claims that everything is highly proprietary, and nothing can ever be disclosed. Make “Trust but Verify” your motto. Seek out facts and advise management why not to make commitments based on mere opinions.
1.4 Goals
Without goals, our plant can be likened to a sailing ship without a harbor. For a ship without a harbor, all winds are favorable winds. If, on the other hand, the ship has a destination harbor, its progress toward arriving at that harbor, the clear goal of the voyage, can be measured. It’s no different with asset performance. Once we have established a goal based on Best-in-Class performance, uptime, profits, safety performance, and a host of other measurable, trackable, reportable common-sense goals, we are well on the road to Operational Excellence.
While we do not want to disagree with the saying: “You can’t manage what you can’t measure” we nevertheless know that not all metrics presently used as key performance indicators (KPIs) make sense. Giving the reader a listing of KPIs of questionable value is of little use, but our text will highlight several KPIs that do make eminent sense. Among these is a listing of machines and availabilities of fluid machines with failure frequencies (possibly) in excess of one’s own averages, or greater in number than experienced by our competitors.
As we proceed to list elementary observations, consider the following situations:
- On-stream factor is about 85% (low) and profits are marginal, at best
- Operator errors are not only having a negative impact on maintenance expenses, but are affecting production and revenue
- Equipment breakdowns are frequent, i.e., a large number of Emergency and Priority 1 work orders are observed
- Predominantly reactive rather than proactive scheduled maintenance work
- Job planning is at a low level
- Repairs are not always correctly carried out the first time
- Scheduled outages are over budget and exceed the scheduled duration
- Critical spare parts are not always in stock to minimize equipment down time
- The maintenance budget is out of control and is escalating at a double-digit rate per year
- Equipment maintenance strategies are informal, vague, not optimized or non-existent
- Well-experienced people are leaving the company at an alarming rate
- Use of contractors for maintenance is not optimized and no in-house expert has jurisdiction over the contractor’s quality of workmanship
- Completed capital projects are not reliable
- “Lost Time” and “Near Miss” safety statistics are trending upward
Ask now if, to some degree, this sounds like the situation in your plant or facility. Are our remedial actions and pursuits consistent with our objectives? Are our facility practices moving in the right direction? We would wish to develop a plan that ultimately drives plant profits and ensures the safety of people and equipment. The knowledge that unbiased SMEs have gained during decades of work in the industry deserves to be presented and illustrated with case studies that are time- tested. With that in mind, the depth of information in this book is not limited to only one person’s experience, although the author’s body of work will nevertheless provide a framework that readers can use and adapt to their situation. This text is not intended to restate what competent others have published, nor to imply that one person’s journey is the only path to achieving specific objectives.
The important point to convey is that the book is far more statement of factual and time-tested experience than futuristic vision or consultant-conceived generalities. It’s not a recounting of the passionate pursuit of a career-conscious dream, but rather a deliberate choice of enhancing one’s sense of self-worth by adding value rather than enhancing one’s career by playing games of office politics. The term “passion for work” has no place in this. The author was breathing a sigh of relief when reading Professor Calvin Newport’s hypothesis and premise [1] that our work product should be such that, in case we would quit our jobs or depart for other reasons, our no longer being there would be noticed. Our work should aim at adding value, but not excel in degrees of passion for the job that would create undue anxiety, hurt our families, or cause us to die prematurely. The author’s view of overtime is very simple: Apart from the occasional (and hopefully very rare) event where our unscheduled late even...
Table of contents
- Title Page
- Copyright
- Contents
- Foreword
- References
- Chapter 1 Why extending fluid machine life is still an essential pursuit
- Chapter 2 The people and the business case
- Chapter 3 Better rolling element bearings are available
- Chapter 4 Understanding value calculations using bearing housing protectors as our example
- Chapter 5 Upgrading general purpose steam turbines
- Chapter 6 Mechanical seal selection facilitated by applying principles of machinery quality assessment
- Chapter 7 Dry gas seals: success, OEMs versus non-OEMs, questions, and what to emphasize
- Chapter 8 Why consider perfluoro-alkoxy carbon-filled polymers
- Chapter 9 Oil rings are the weak link in lubricant application
- Chapter 10 Consider today’s canned motor pumps
- Chapter 11 More than one problem may be at work in machines
- Chapter 12 Common blower improvement opportunities
- Chapter 13 Integral gear CO2 compressors offer high reliability and efficiency
- Chapter 14 Power transmission couplings: select the best configurations
- Appendix 1 From early condition monitoring to wireless sensor technology
- Appendix 2 Training reliability professionals and subject matter experts
- Appendix 3 Specifying pumps for the oil and gas industries
- Index