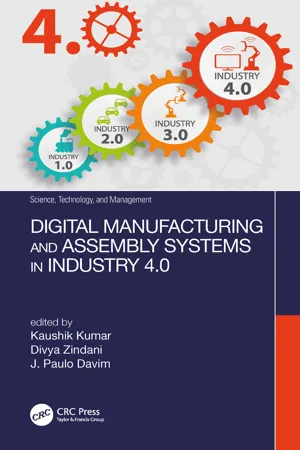
eBook - ePub
Digital Manufacturing and Assembly Systems in Industry 4.0
This is a test
- 162 pages
- English
- ePUB (mobile friendly)
- Available on iOS & Android
eBook - ePub
Digital Manufacturing and Assembly Systems in Industry 4.0
Book details
Book preview
Table of contents
Citations
About This Book
Manufacturing, like other industries, is rising to the challenges imposed by aggressive consumer demands and the need for cost-effective processing that delivers quality in the fastest possible time. Fierce competition means that keeping abreast of new developments and applications in technology is essential if companies are to meet demands profitably and keep ahead of competitors. This book investigates the design and management of digital manufacturing and assembly systems for an efficient, flexible, and modular production of customized products using the I40 (industry 4.0)-enabling technologies. This book will also provide case studies covering modeling, simulation, and optimization.
-
- eBook includes color figures.
-
- Discusses how the advancement of data communication and storage through the Internet of Things (IoT) opens the possibilities of connecting sensors, robots, and devices
-
- Sheds light on how the human role in industry is decreasing due to the development of connected manufacturing floors, allowing them to take more control over the manufacturing processes, decisions, and even maintenance
-
- Covers the benefits from exploiting digital manufacturing, manufacturing enterprises, and what they expect to achieve
-
- Explains the important roles that modeling, simulation, and optimization play
-
- Investigates the design and management of digital manufacturing and assembly systems for an efficient, flexible, and modular production of customized products exploiting the I40 (industry 4.0)-enabling technologies
Frequently asked questions
At the moment all of our mobile-responsive ePub books are available to download via the app. Most of our PDFs are also available to download and we're working on making the final remaining ones downloadable now. Learn more here.
Both plans give you full access to the library and all of Perlegoâs features. The only differences are the price and subscription period: With the annual plan youâll save around 30% compared to 12 months on the monthly plan.
We are an online textbook subscription service, where you can get access to an entire online library for less than the price of a single book per month. With over 1 million books across 1000+ topics, weâve got you covered! Learn more here.
Look out for the read-aloud symbol on your next book to see if you can listen to it. The read-aloud tool reads text aloud for you, highlighting the text as it is being read. You can pause it, speed it up and slow it down. Learn more here.
Yes, you can access Digital Manufacturing and Assembly Systems in Industry 4.0 by Kaushik Kumar, Divya Zindani, J. Paulo Davim, Kaushik Kumar, Divya Zindani, J. Paulo Davim in PDF and/or ePUB format, as well as other popular books in Technology & Engineering & Electrical Engineering & Telecommunications. We have over one million books available in our catalogue for you to explore.
Information
Section II
Applications
4
Applying Theory of Constraints to a Complex Manufacturing Process
CONTENTS
4.1 Introduction: Background and Driving Forces
4.2 Literature Review: What Is the Theory of Constraints All About?
4.2.1 The Five Focusing StepsâA Process of Continuous Improvement
4.3 Research Problems and Objectives
4.4 Relevant Analysis Techniques
4.5 The Case-in-Point: FD Solutions Private Limited
4.6 Applying the Theory of Constraints to the Case Company
4.6.1 Identify the Constraints
4.6.2 Exploit the Constraint
4.6.2.1 Primary ConstraintâAssembly and Testing
4.6.2.2 Secondary ConstraintâAssembly of Truss Box
4.6.2.3 Results Observed
4.6.3 Subordinate Everything to the System Constraint
4.6.4 Elevate the Constraints
4.6.4.1 Full Kitting
4.6.4.2 Future Actions and Investment Required
4.6.5 Repeat: Going Back to Step 1
4.7 Conclusion
4.7.1 Overall Results and Managerial Implications
4.7.2 Future Research on the Theory of Constraints
References
4.1 Introduction: Background and Driving Forces
Manufacturing companies are facing increasingly difficult challenges in managing their production processes. These challenges can arise from a number of different sources, one of which is Complexity of process. As time has passed and products have become more sophisticated and companies have increased their product offering, modern factories have had to produce various kinds of products with an increasing number of components and increasingly complicated production processes compared to those in the past (Mukherjee and Chatterjee 2007). Thus, factory managers face the challenge of managing and controlling the aforementioned complexity while simultaneously complying with the requirements of the organization and the end customer. As a result, factories are often required to perform at the edge of their capabilities (Calinescu et al. 1998). Some even go as far as defining all manufacturing systems as complex. Inevitably, as complexity increases, the factory must become nimbler and more flexible as well. As flexibility increases, one of the negative side effects can be loss of control. Controlling a complex manufacturing environment is essential; otherwise, the complexity will lend itself only to make the environment more difficult to manage. A number of philosophies and frameworks have been introduced to help people control manufacturing environments and all the processes present within it.
When (Goldratt and Cox 1984) first introduced the Theory of Constraints (TOC), it provided the manufacturing world with a perspective that was desperately needed. Factory managers, consultants, and auditors used to use a wide range of quality control and management techniques to have better control over their respective setups as well as specific process improvement. But the TOC provided these professionals with a systemâs approach to overall performance improvement. By looking at the system as a whole, and maintaining a single goal for every person, machine, or process to work toward, while continuously strengthening the weakest links, professionals were able to achieve holistic success.
This research examines the production processes of the case company, FD Solutions, through the TOC methodology, using systemâs approach. The TOC was used to develop the right suggestions at the right time to the right part(s) of the case companyâs system. Companies like FD Solutions produce quality products that enrich the lives of all their customers. This research is motivated by the need to help world-class companies such as FD Solutions to perform better, so that they stay ahead of the curve and continue providing the value they presently do.
4.2 Literature Review: What Is the Theory of Constraints All About?
Since 1984, the TOC has continued to evolve and further develop, and today it is a significant factor within the world of management best practices. The TOC has since been applied in various companies such as Boeing, 3M, Honeywell, and General Electric (GE). It was also highly applicable in large not-for-profit organizations such as NASA, The United States Department of Defense, and the Israeli Air Force. A successful TOC implementation will often yield the following benefits (Goldratt et al. 2010):
1. Increased profit (often the primary goal of TOC)
2. Fast-focused improvement (a result of putting all attention to one critical areaâthe bottleneck)
3. Improved capacity (when the constraint is optimized, more products can be manufactured)
4. Reduced lead times (when the constraint is optimized, there is smoother and faster flow)
5. Reduced inventory (eliminating bottlenecks results in lesser work in progress)
The TOC takes a rather scientific approach to process improvement. It hypothesizes that every system, as complex as it may be, consists of multiple linked activities. As no system can ever be perfect, one of the many linked activities acts as a constraint upon the entire system. Stated in the TOC are three measurable aspects in any production system:
1. Throughput: The rate at which the system generates money through sales
2. Inventory: All the money the system has invested in purchasing anything it intends to sell
3. Operating Expense: All the money spent to turn Inventory to Throughput
The TOC also states that this constraint limits the amount of throughput in the entire system. The throughput is, in turn, limited by the amount of inventory behind the constraint (Spencer 1994). Relieving the constraint reduces inventory and increases throughput, therefore lowering the operational expense (Goldratt and Cox 1984).
4.2.1 The Five Focusing StepsâA Process of Continuous Improvement
The TOC advocates a continuous improvement process that will enable organizations to always focus on the bottlenecks in any process (Vorne 2019). This is meant to be a check whether the company is on the right path. The core of this improvement process comes from what is termed as the Five Focusing Steps. In the novel Goal written by Goldratt and Cox (1984), lead characters gradually discover these steps as they try to improve the plantâs performance. The steps are a scientific methodology for successfully identifying and eliminating constraints. It is a cyclic process as shown in the Figure 4.1 below:...
Table of contents
- Cover
- Half Title
- Title Page
- Copyright Page
- Table of Contents
- Preface
- Editors
- Contributors
- Section I Overview
- Section II Applications
- Index