
eBook - ePub
Gas Turbines Modeling, Simulation, and Control
Using Artificial Neural Networks
This is a test
- 206 pages
- English
- ePUB (mobile friendly)
- Available on iOS & Android
eBook - ePub
Gas Turbines Modeling, Simulation, and Control
Using Artificial Neural Networks
Book details
Book preview
Table of contents
Citations
About This Book
Gas Turbines Modeling, Simulation, and Control: Using Artificial Neural Networks provides new approaches and novel solutions to the modeling, simulation, and control of gas turbines (GTs) using artificial neural networks (ANNs). After delivering a brief introduction to GT performance and classification, the book: Outlines important criteria to consi
Frequently asked questions
At the moment all of our mobile-responsive ePub books are available to download via the app. Most of our PDFs are also available to download and we're working on making the final remaining ones downloadable now. Learn more here.
Both plans give you full access to the library and all of Perlegoās features. The only differences are the price and subscription period: With the annual plan youāll save around 30% compared to 12 months on the monthly plan.
We are an online textbook subscription service, where you can get access to an entire online library for less than the price of a single book per month. With over 1 million books across 1000+ topics, weāve got you covered! Learn more here.
Look out for the read-aloud symbol on your next book to see if you can listen to it. The read-aloud tool reads text aloud for you, highlighting the text as it is being read. You can pause it, speed it up and slow it down. Learn more here.
Yes, you can access Gas Turbines Modeling, Simulation, and Control by Hamid Asgari, XiaoQi Chen in PDF and/or ePUB format, as well as other popular books in Physical Sciences & Energy. We have over one million books available in our catalogue for you to explore.
Information
Chapter one
Introduction to modeling of gas turbines
The knowledge of anything, since all things have causes, is not acquired or complete unless it is known by its causes.
Ibn Sina (Avicenna)
Persian Polymath, 980ā1037
A gas turbine (GT) is an internal combustion engine that uses the gaseous energy of air to convert chemical energy of fuel into mechanical energy. It is designed to extract, as much as possible, the energy from the fuel [1]. The service of GTs in industrial equipment and utilities located on power plants and offshore platforms has increased in the past 50 years. This high demand is because of their low weight, compactness, and multiple fuel applications [2]. Although the story of GTs has taken root in history, it was not until 1930s that the first practical GT was developed by Frank Whittle and his colleagues in Britain for a jet aircraft engine [3]. GTs were developed rapidly after World War II and became the primary choice for many applications. That was especially because of the enhancement in different areas of science such as aerodynamics, cooling systems, and high-temperature materials, which significantly improved the engine efficiency. Thus, it is not surprising that GTs have been increasing in popularity year by year. They have the ability to provide a reliable and continuous operation. The operation of nearly all available mechanical and electrical equipment and machinery in industrial plants such as petrochemical plants, oil field platforms, gas stations, and refineries, depends on the power produced by GTs. The wide application of GTs throughout the world especially in electrical utilities is due to their reliability, availability, adaptability, fast start capability, low initial cost, and short delivery time [4]. They are independent of cooling water and can operate on a variety of fuels. GTs provide high rates of load growth in the summer time and respond fast to load changes [4].
During recent years, considerable activities have been carried out especially in the field of modeling and simulation of GTs. It is because the need for and use of GTs have become more apparent in the modern industry. Creating models of GTs and their related control systems has been a useful technical and cost-saving strategy for performance optimization of the equipment before the final design process and manufacturing. GT models and simulators can be used for off-design performance prediction, and evaluation of emissions, turbine creep life usage, and the engine control system [5]. Mathematical modeling is considered as a general methodology for system modeling. It uses mathematical language to describe and predict the behavior of a system.
Great efforts have been made in developing GTs to overcome their related challenging economic and engineering problems [6] and to have a reliable and cost-effective design [7]. One of the best approaches for optimization of design, performance, and maintenance of GTs is offline modeling and simulation. It helps manufacturers and users in different ways. Manufacturers can evaluate and optimize the performance of a specific model of GT during design and manufacturing processes. Models may also be used online on sites by operators and site engineers for condition monitoring, sensor validation, fault detection, troubleshooting, and so on. A variety of analytical and experimental models of GTs has been built so far. However, the need for optimized models for different objectives and applications has been a strong motivation for researchers to continue to work in this area.
This chapter briefly explains the principles of performance of a typical GT and classification of GTs. Main considerations in GT modeling including GT types and configurations, modeling methods, control system types and configurations, as well as modeling objectives and approaches, are explained in the following sections of this chapter; followed by problems and limitations and modeling objectives.
1.1 GT performance
GTs work based on Brayton cycle: Figure 1.1 shows a typical single-shaft GT and its main components including compressor, combustion chamber (combustor), and turbine. The set of these components is called engine core or gas generator (GG). Compressor and turbine are connected to the central shaft, and they rotate together.
Figure 1.1
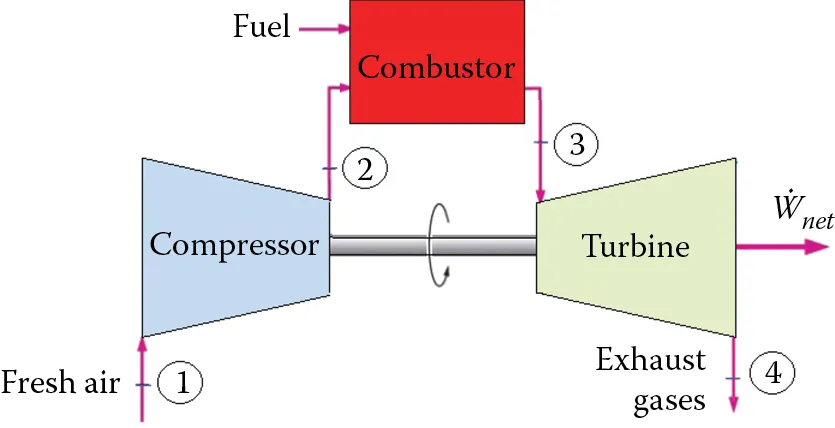
Schematic of a typical single-shaft GT.
Figure 1.2 shows standard Brayton cycle in pressureāvolume (PāV) and temperatureāentropy (TāS) frames, respectively [8]. As the figure shows, air enters the compressor at section 1 and is compressed through passing the compressor. The hot and compressed air enters the combustion chamber (combustor) at section 2. In combustor, fuel is mixed with air and ignited. The hot gases which are the product of combustion are forced into the turbine at section 3 and rotate it. Turbine drives the compressor and the GG mechanical output, which can be an electricity alternator in a power plant station, a large pump, or a large compressor. The ideal processes in the compressor (1-2) and turbine (3-4) are isentropic. There is also an isobaric process in the combustor (2-3) and environment (4-1) for the ideal cycle. However, the actual processes in the compressor and turbine are irreversible and nonisentropic. There is also a pressure loss during the process in the combustor. Neglecting the pressure loss in the air filters and the combustor, processes 2-3 and 4-1 can be considered isobaric [9].
Figure 1.2
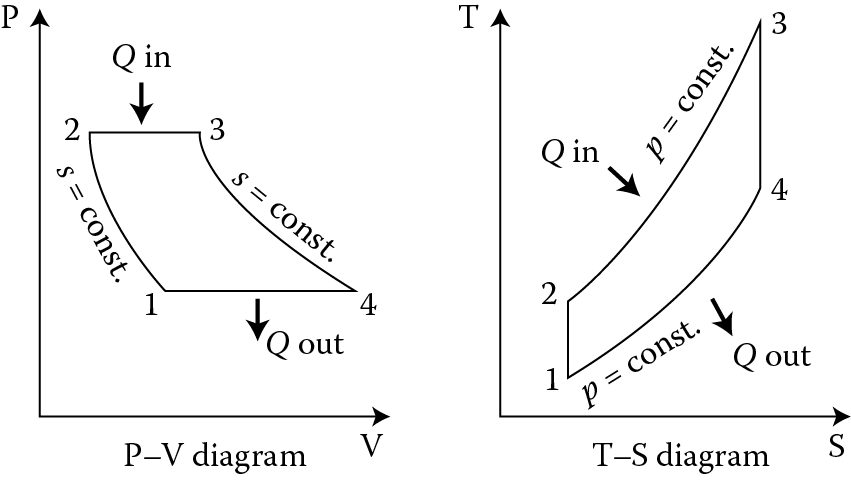
Typical Brayton cycle in pressureāvolume and temperatureāentropy frames. (From Wikimedia Commons Webpage. 2013. [Online]. Available: http://en.wikipedia.org. [Accessed June 14, 2013].)
1.2 GT classification
GTs can be divided into two main categories including aero GTs and stationary GTs. In aero industry, GT is used as propulsion system to make thrust and move an airplane through the air. Thrust is usually generated based on the Newtonās third law of action and reaction. There are varieties of aero GTs including...
Table of contents
- Preface
- Acknowledgments
- Authors
- Nomenclature
- Chapter one - Introduction to modeling of gas turbines
- Chapter two - White-box modeling, simulation, and control of GTs
- Chapter three - Black-box modeling, simulation, and control of GTs
- Chapter four - ANN-based system identification for industrial systems
- Chapter five - Modeling and simulation of a single-shaft GT
- Chapter six - Modeling and simulation of dynamic behavior of an IPGT
- Chapter seven - Modeling and simulation of the start-up operation of an IPGT by using NARX models
- Chapter eight - Design of neural network-based controllers for GTs
- References