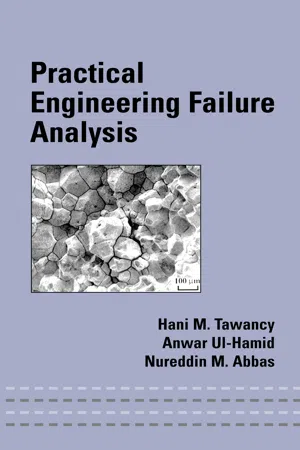
eBook - ePub
Practical Engineering Failure Analysis
Hani M. Tawancy, Anwar Ul-Hamid, Nureddin M. Abbas
This is a test
Share book
- 616 pages
- English
- ePUB (mobile friendly)
- Available on iOS & Android
eBook - ePub
Practical Engineering Failure Analysis
Hani M. Tawancy, Anwar Ul-Hamid, Nureddin M. Abbas
Book details
Book preview
Table of contents
Citations
About This Book
Filling a gap in the literature, Practical Engineering Failure Analysis vividly demonstrates the correct methodology to conduct successful failure analyses, as well as offering the background necessary for these investigations. This authoritative reference covers procedures to reduce the occurrence of component failures due to errors in material se
Frequently asked questions
How do I cancel my subscription?
Can/how do I download books?
At the moment all of our mobile-responsive ePub books are available to download via the app. Most of our PDFs are also available to download and we're working on making the final remaining ones downloadable now. Learn more here.
What is the difference between the pricing plans?
Both plans give you full access to the library and all of Perlego’s features. The only differences are the price and subscription period: With the annual plan you’ll save around 30% compared to 12 months on the monthly plan.
What is Perlego?
We are an online textbook subscription service, where you can get access to an entire online library for less than the price of a single book per month. With over 1 million books across 1000+ topics, we’ve got you covered! Learn more here.
Do you support text-to-speech?
Look out for the read-aloud symbol on your next book to see if you can listen to it. The read-aloud tool reads text aloud for you, highlighting the text as it is being read. You can pause it, speed it up and slow it down. Learn more here.
Is Practical Engineering Failure Analysis an online PDF/ePUB?
Yes, you can access Practical Engineering Failure Analysis by Hani M. Tawancy, Anwar Ul-Hamid, Nureddin M. Abbas in PDF and/or ePUB format, as well as other popular books in Technology & Engineering & Industrial Engineering. We have over one million books available in our catalogue for you to explore.
Information
1
Introduction
1.1 Engineering Products and Their Performance
Any engineering product ranging from a vacuum cleaner to an aircraft is designed and manufactured to perform specific functions serving human needs over a predetermined service life. Its history includes three main stages: (i) engineering design, (ii) manufacturing, and (iii) service as schematically illustrated in Fig. 1.1.
Engineering design is essentially a decision-making process by which a product can be manufactured at a reasonable cost. Differences in design of a given product, which are reflected on its performance can be related to the extent of engineering analysis preceding any decision made by the designer. Parameters included in such an analysis are (i) geometry and dimensions of different parts, (ii) types of materials used in manufacturing and their specifications, (iii) fabrication and assembling techniques, and (iv) service conditions.
Design is initiated after establishing the market need for a new product or improving the performance of an existing product. Subsequently, the design engineer conceives, plans, and conducts a program to develop complete engineering drawings of the product specifying the above design parameters. A prototype product is then manufactured and tested. If necessary, the design is modified so that the product meets all required specifications. Following this stage, the design is materialized into a commercial product by the manufacturer. Finally, the product is put into service to meet its functional requirements specifying the procedures of start-up and shutdown as well as the maintenance procedure and its schedule. Figure 1.2 summarizes the above aspects of engineering design.

Figure 1.1 Main stages in the history of an engineering product.
From our daily experience, we come to realize that various brands of a given product can significantly differ in their performance and durability. When a household item breaks down after a short usage, statements such as “the item is made of a cheap material,’’ “the item is so cheap,’’ “the item is poorly made” are often heard to explain the incident. In technical terms, such statements refer to design and manufacturing. Another possible explanation for the incident is that the item is misused, referring to service conditions deviating from manufacturer’s recommendations based upon design parameters.
A direct correlation exists between the cost of any product and the effort spent in engineering analysis to optimize its design, including the quality of materials used in manufacturing as well as the fabrication techniques. One of the most important aspects of design determining performance is the quality of material selected for the application. Proper selection of material by the designer determines to what extent the user of the product realizes its reliability and satisfactory service life. Quite often, the material dictates the fabrication technique. It then becomes evident that the service performance of any engineering product can be envisioned as a step in a chain of a continuous process beginning with design, as further explained in Chap. 2. Differences in performance and cost of various brands of a given product can therefore be related to variations in (i) design including materials used in manufacturing and (ii) the fabrication techniques used to manufacture the product.

Figure 1.2 Main aspects of engineering design.
Design engineers are usually more concerned with structural and mechanical functions of the products. Therefore, the reaction of materials to mechanical usage, i.e., how materials respond to applied forces or loads, assumes a primary importance in deciding which material is to be selected. Any engineering product, however, cannot operate in complete isolation fulfilling its mechanical functions without interference from the environment. Various types of environmental effects, e.g., temperature and nature of substances in the environment, can have an important impact on the reliability and functional characteristics of the product.
Almost every design and useful application devised by the engineer is dictated by the quality of materials used in manufacturing, which limits the performance capabilities of the product. For example, the efficiency of an aircraft gas turbine engine is limited by the temperature capabilities of the materials used to manufacture its hottest sections.
Materials used to manufacture engineering products are referred to as engineering or structural materials. To classify a material as an engineering material, it must fulfill two main requirements. First, it must possess desirable qualities or properties rendering it suitable to manufacture certain products. Secondly, it must be readily fabricated in large quantities by standard techniques. Engineering materials can be classified into two main types: (i) metallic and (ii) nonmetallic. Even though the number of nonmetallic materials and their use in manufacturing continue to increase, metallic materials remain indispensable in many industrial applications because of their unique combination of properties.
Since engineering materials are the primary building blocks of any engineering product, material selection is one of the most important decisions made by the designer. It is important that the designer must have a broad knowledge of the meaning of each material property and how it is determined. Such knowledge is essential in terms of identifying the properties relevant to the application and whether their listed values are derived under conditions similar to those encountered in practice. A brief account of the engineering properties of materials is given in Sec. 1.2, and the various classes of engineering metallic materials are described in Sec. 1.3.
To summarize the above discussion, the service performance of a given product is dependent upon the extent to which the various steps of the continuous process of engineering design-manufacturing-performance are correlated and tailored so that the product can effectively perform its functions over its intended service life. Each step in the above process can be considered as a link in a chain connecting design with manufacturing and performance. Depending upon the extent of engineering analysis spent to strengthen these links, various brands of the same product can significantly differ in their performance as well as cost. On the other hand, the above chain can be expected to fall apart at its weakest link, as described in Sec. 1.5.
1.2 Engineering Properties of Materials
Engineering properties are those qualities of structural materials which qualify them for use in manufacturing various products. They can be classified into four main types: (i) mechanical properties, (ii) physical properties, (iii) chemical properties, and (iv) fabrication properties, as summarized in Fig. 1.3. In this section, the various engineering properties are briefly defined. Procedures used to measure these properties and their origin are described in Chap. 4.
1.2.1 Mechanical Properties
Design engineers are primarily concerned with mechanical properties which describe the response of the material to externally applied mechanical loads or forces. A material reacts to an applied force whether it is small or large by distortion or deformation; i.e., it undergoes a change in shape or dimensions, which is known as strain. Simultaneously, the material develops internal forces known as stress to counteract the effect of the applied force. Strain can be measured directly, but stress can only be calculated from knowledge of strain. For a given material, the amount of strain is determined by the magnitude of the applied force. Two types of strain are distinguished: (i) elastic strain and (ii) plastic strain, as shown in Fig. 1.4.

Figure 1.3 A summary of important engineering properties of materials.
When the applied load is relatively small, the strain is elastic. By elastic is meant that when the applied force is removed, the material springs back to its original dimensions; i.e., the elastic strain is reversible or recoverable. In contrast, the plastic strain is irreversible; i.e., a plastically strained material undergoes a permanent change in shape or dimensions. It occurs when the applied load exceeds a certain critical value dependent upon the material. Plastic deformation continues to occur as the applied load is increased until ultimately it is terminated by fracture. Materials which can readily deform in a plastic manner to accommodate the effect of an applied load prior to fracture are said to be ductile.
Plastic deformation of a given material to accommodate the effect of an applied force is a thermally activated time-dependent process, and therefore it is influenced by two important parameters: (i) the rate at which the force is applied or strain rate and (ii) temperature. At a given temperature, if the force is applied relatively slowly in a progressive manner, the material can readily deform; however, the same material can fracture without undergoing an appreciable deformation if the load is applied very rapidly. Increasing the temperature has the same effect as reducing the strain rate.

Figure 1.4 Schematics illustrating the difference between elastic and plastic deformation. (a) Elastic deformation: When the applied load P1 is relatively small, the deformed part (loaded) springs back to its original shape after the load is removed (unloaded). (b) Plastic deformation: When the load is increased to P2, the deformed part (loaded) undergoes a permanent change in shape after the load is removed (unloaded).
It can be concluded from the above discussion that the response of a material to an applied force or load can be described in terms of three separate phenomena: (i) elastic deformation, (ii) plastic deformation, and (iii) fracture. Usually, designers are primarily concerned with the capacity of the material to carry an applied load without fracturing. In some applications, a certain amount of deformation usually elastic can be tolerated. Frequently, however, the amount of deformation must be limited to a rigidly minimum value, as described below.
An applied load can either be static or dynamic defining various sets of mechanical properties. By definition, a static load such as a dead weight is applied only once. Tensile loads which tend to stretch the material are of primary importance in applications for structural and mechanical functions. Under the influence of a static tensile load, a part made of a given material is stretched and its cross- sectional area is reduced. Two different sets of mechanical properties are defined under static loading condition: (i) tensile properties and (ii) creep properties.
Tensile properties define the response of a material to a progressively increasing tensile load until fracture occurs. They include yield strength, ultimate tensile strength, and tensile ductility. Yield strength is defined as the load per unit cross-sectional area required to initiate plastic deformation on a macroscopic scale. It is a measure of the useful load-carrying ability of the material. Ultimate tensile strength or shortly tensile strength is the load per unit area beyond which fracture occurs. Tensile ductility can be expressed as the percentage elongation at the point of fracture; however, a more meaningful measure is the reduction in cross-sectional area. Up to a temperature corresponding to about one-third the melting point of the material on the absolute scale (degrees Kelvin), the tensile properties are not significantly influenced by the strain rate. However, above that temperature, the effect of strain rate becomes significant.
Since plastic deformation is a thermally activated process, a material can progressively deform in a plastic manner with time at elevated temperatures under the influence of a static load even if it is below the corresponding tensile yield strength at the same temperature. Such a phenomenon is called creep and it becomes significant at temperatures >0.5Tm, where Tm is the melting point on the absolute scale. Plastic deformation resulting from creep is terminated by fracture. Creep properties are expressed in terms of the stress required to produce specific creep strain in a given time at a certain temperature or the stress required to cause fracture.
Dynamic loads are classified into two types: (i) impact loads and (ii) fatigue loads. An impact load resembles a static load in that it can be a single application of a force. However, in contrast with a static load, the rate of deformation is very high, which can localize the stresses in the weak sections of the part leading to fracture. Resistance to fracture under impact loading condition is measured in terms of the energy required to cause fracture, which is known as impact toughness. Fatigue loading is a more common type of a dynamic load. In this case, a load considerably smaller than the static load corresponding to the yield strength is repeatedly applied to the part in a cyclic manner. Even though the fatigue load is lower than that corresponding to the yield point, it ultimately leads to fracture after a certain number of cycles. Fatigue strength is expressed in terms of the number of cycles required to cause fracture under a given stress.
Resistance to fracture of a given material is expressed in terms of a parameter called the fracture toughness. It relates the stress required to propagate an existing crack with the initial crack length.
Another mechanical property which is frequently used to evaluate the strength of materials is hardness. However, it is not as well defined as other properties such as yield and ultimate strengths because of its dependence on the method of measurement as well as the measurement conditions. Nevertheless, if the hardness value is accurately defined, a direct correlation exists between hardness and strength. A higher hardness reflects higher yield and ultimate strengths and in turn, a lower ductility.
1.2.2 Physical Properties
Among the important physical properties in engineering applications are density and thermal properties. In several applications particularly aerospace, the strength-to-weight ratio of the part is an important design parameter. A high ratio requires that a material of a smaller density has a sufficiently high strength.
When a product is designed to operate at high temperatures, it is essential to check the mechanical properties at the actual service temperature. Frequently, temperature gradients exist in components operating at high temperatures, which are designed to either preserve or minimize this gradient depending upon the particular application. If it is required to maintain a steep temperature gradient, a structural material with low thermal conductivity must be used. Metallic materials are generally classified as good thermal conductors. Thermal properties are expressed in terms of thermal co...