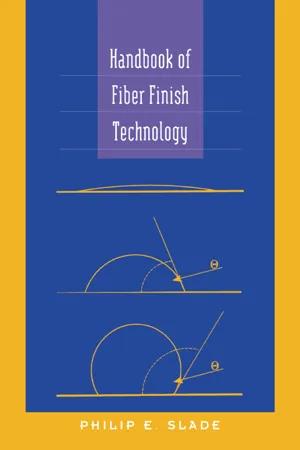
This is a test
- 540 pages
- English
- ePUB (mobile friendly)
- Available on iOS & Android
eBook - ePub
Handbook of Fiber Finish Technology
Book details
Book preview
Table of contents
Citations
About This Book
Discusses the components of textile finishes, and the chemical and physical properties of, as well as their effects on, various fibres. The book covers fundamentals of fibre finish science, such as theories of friction; laboratory testing of formulations, from preliminary component evaluation to analyses for material characterization; and the influence of wetting, emulsification and finish distribution on coatings.
Frequently asked questions
At the moment all of our mobile-responsive ePub books are available to download via the app. Most of our PDFs are also available to download and we're working on making the final remaining ones downloadable now. Learn more here.
Both plans give you full access to the library and all of Perlegoâs features. The only differences are the price and subscription period: With the annual plan youâll save around 30% compared to 12 months on the monthly plan.
We are an online textbook subscription service, where you can get access to an entire online library for less than the price of a single book per month. With over 1 million books across 1000+ topics, weâve got you covered! Learn more here.
Look out for the read-aloud symbol on your next book to see if you can listen to it. The read-aloud tool reads text aloud for you, highlighting the text as it is being read. You can pause it, speed it up and slow it down. Learn more here.
Yes, you can access Handbook of Fiber Finish Technology by Philip E. Slade in PDF and/or ePUB format, as well as other popular books in Scienze fisiche & Chimica. We have over one million books available in our catalogue for you to explore.
Information
CHAPTER 1
INTRODUCTION
Although many valuable products are fabricated each day from synthetic fibers, these items could never exist unless a lubricating finish had been applied to the fibers during the extrusion or spinning process. A package, bobbin, or bale cannot be made without application of a spin finish. No drawing or texturing could take place and additional processing of the yarn could not be accomplished, either through internal manufacturing or at a customerâs plant, without the presence of this finish. The fibers would be a useless, tangled mass of extruded polymer unless the creativity of the finish chemists results in the formulation of a lubricating mixture that is applied early in the manufacturing process. These may appear to be strong statements to a casual observer, but they are not without validity since all natural fibers are created with a lubricating finish on the surface of those products.
Wool is coated with a product known as wool fat, which in its purified form is called lanolin. One curious observation is that the lubricating fat content of wool varies depending upon the country of origin [1]. This is shown in Table 1â1. The composition of wool fat has been investigated and it consists mostly (73%) of the esters of cholesterol and other fatty alcohols, some fatty acid esters and free alcohols (25%), and small amounts of free fatty acids and hydrocarbons [1].
Cotton also has a coating on the surface of the fiber, called cotton wax. This wax is composed of about 43% free monohydroxy aliphatic alcohols, about 13% phytosterols, both in the free form and as their esters, about 22% esters of wax acids, and about 8% hydrocarbons and some smaller amounts of other products [1].
Table 1â1
Fat Content of Wool from Various Sources
Wool | Wool Fat (%) |
Australian | 35 to 46 |
African | 28 to 41 |
Peruvian | 9 to 14 |
English | 9 |
(Ref. [1]. Reprinted by permission of Van Nostrand Reinhold)
As a silkworm spins its cocoon, the silk fiber, or fibroin, is held together by a substance called sericin, or silk gum. A cocoon consists of about 80% fibroin and 20% sericin. The sericin, a protein, is the natural silk finish that is necessary for future processing of that fiber. Some of the sericin is removed by boiling water during processing so that the cocoon can be unwound, but the remainder is left to prevent damage to those delicate fibers [2].
It would be virtually impossible to duplicate either wool fat, cotton wax, or sericin as a spin finish formulation since most of the components of these compositions are not commercially available. The finish chemist must, therefore, formulate a mixture of available chemical components that will allow synthetic fibers to be processed on textile machinery into a final product that the consumer will buy.
In this handbook of finish science and technology, we will explore the chemistry, physics, and engineering of finishes and their components. The testing of those products to predict how the materials will process on synthetic fiber manufacturing equipment, and how these fibers are processed into a final product, will also be examined.
1.1 ART AND TECHNOLOGY
The synthetic fiber industry began in the middle of the 19th century with the introduction of nitrocellulose fibers, but full commercial production of this type of fiber did not commence until after 1890. The nitrocellulose process was followed by the cuprammonium process and then the viscose process, for which commercial production began in about 1905. Some spin finishes were necessary for fibers made using these processes, but little is known about their compositions. With the production of rayon, then known as artificial silk, during the First World War, mineralâoilâbased finishes emulsified with a soap began to be produced. Their formulation was based mainly on trial and error and the compositions were safeguarded as secret mixtures. Until about twenty years ago, spin finish development was almost entirely an art, and one gained experience through many failures and only with an instinct that a formulation would be satisfactory. Since then, a substantial amount of time and energy have gone into the transformation of finish development from art into technology. This transition was accomplished in both the synthetic fiber producersâ research laboratories and in the laboratories of finish formulators or component suppliers.
There are many difficulties when finish formulation is perceived as an art, without logical scientific reasoning. Some people never seem to develop the knack for putting together a group of components and arriving at a finish composition that will solve a problem. There are major disadvantages, however, for remaining in the art mentality:
1. Individual chemists tend to become highly specialized in their jobs, which might limit their chances for advancement or in their professional development.
2. For the fiber company, a large amount of critical technology accumulates in the skills of a few people who might not be inclined to pass this technology along to others.
3. It takes a very long incubation time for a technologist to become skilled in finish development. In rapidly changing fiber markets, that time may be excessive if a person who is skilled in finishes should leave the company or retire. Despite being apprenticed to some excellent tutors, this author did not achieve a comfortable feeling about finish formulation for at least five years after entering the field.
Although one can never completely change finish development from an art into an exact science, it is undeniably worth the effort to attempt that approach.
This manual is not intended to be the last word in finish technology. In the fiber manufacturing business, change is ever present. Each time that a technique is perfected or a new component evaluated, another improvement thrusts itself upon the horizon. It is important to broaden the knowledge base and to determine that the latest formulation is certainly not the last. One must always work toward making his or her latest creation obsolete, and efforts must be directed toward something better, for if they are not, a competitor will achieve that goal.
1.2 REQUIREMENTS FOR SPIN FINISHES
A spin finish must satisfy many requirements [3] to allow the yarn on which it has been applied to be processed satisfactorily. The finish chemists must keep these in mind when compounding their formulations. The considerations may be summarized as:
1. Safety. The finish must not contain any materials that are toxic or cause injury to persons in contact with the finish, either in the liquid state or on the yarn. One area that must be addressed specifically is that of waste disposal. Many finish components are removed from the yarn during dyeing or some other processing step, and these must not be hazardous to the environment.
2. Yarn Lubrication. Perhaps one of the most important characteristics of a spin finish is to provide the proper lubricity for the yarn or fiber. This lubricity includes both fiber to metal and fiber to fiber lubrication. It is most important to note the use of the phrase proper lubricity, because many people who are not skilled in the science of fiber lubrication assume that the lower the friction between the fiber and another object the better the fiber will process, but that is not always the case. Often one must adjust the lubrication of the yarn to higher frictional values to yield enhanced yarn performance.
3. Antistatic Properties. The finish must be able to dispel the static electrical charges that build up on the yarn. While static dissipation is attributed chiefly to the conductance of a water layer, the use of an antistatic agent to enhance this conductance is very important.
4. Microorganism Growth. The finish must not allow the growth of bacteria, fungi, or yeast since these organisms could seriously interfere with the processing of the yarn.
5. Wetting. If the finish does not wet the yarn properly, the application will be uneven and this will present problems in processing.
6. Emulsion Quality. Since most finishes in the United States are made as an oilâinâwater emulsion, the emulsion must be a stable suspension with small particle size and a large negative zeta potential.
7. Chemical Effects. The finish should neither absorb too quickly into the fiber, nor react with the fiber in any way.
8. Oxidation. During prolonged storage of the fiber, finishes should not undergo any oxidative degradation.
9. Viscosity. The viscosity of the components and the final finish formulation should be homogeneous and be relatively free of temperature effects.
10. Removal. Spin finishes should be easily removed during the scouring process prior to dyeing.
11. Cost. The components should be available at a reasonable price.
12. Biodegradability. The finish must be biodegradable in the public waste treatment facilities that are available to the plants involved.
13. Thermal Properties. The finish should have the correct thermal properties to allow the proper processing on heated equipment.
Although it is probably impossible to formulate a finish that meets all these requirements, it is possible to compromise and thus achieve as nearly as possible the ideal composition.
1.3 COMPONENTS IN SPIN FINISHES
Every spin finish consists of one or more components [4]â[6], with the choice of materials dependent upon the end use of the yarn being prepared. Generally, a finish will contain the following materials:
1. Lubricants. These components may be water insoluble materials such as esters, alkanolamides, mineral oils, long chain fatty acids or alcohols, fluorocarbons, or silicones. Water soluble materials as ethylene oxideâpropylene oxide copolymers are very valuable as components. At times, emulsifiers, cohesive agents, or antistats may provide lubrication properties.
2. Emulsifiers. If the lubricant is water insoluble and if the finish is to be applied as an oilâinâwater emulsion, an emulsifier is necessary to obtain the proper suspension. Some typical emulsifiers are ethoxylated glycerides, ethoxylated fatty acids or fatty alcohols, and polyglycol esters. Anionic emulsifiers, such as sodium lauryl sulfate normally used in dishwashing detergents, find limited use in spin finishes.
3. Antistatic Agents. Anionic, cationic, nonionic, and some amphoteric components are used in spin finishes a...
Table of contents
- Cover
- Half Title
- Title Page
- Copyright Page
- Table of Contents
- Preface
- CHAPTER 1. INTRODUCTION
- CHAPTER 2. TENSION, FRICTION, AND LUBRICATION
- CHAPTER 3. LABORATORY TESTING AND COMPONENT PROPERTIES
- CHAPTER 4. YARN TO HARD SURFACE LUBRICANTS FOR FIBER FINISHES
- CHAPTER 5. COHESIVE AGENTS AND FIBER TO FIBER LUBRICANTS
- CHAPTER 6. EMULSIFIERS
- CHAPTER 7. ANTISTATS
- CHAPTER 8. OTHER FINISH ADDITIVES: ANTIOXIDANTS, DEFOAMERS, ANTIMICROBIALS, AND WETTING AGENTS
- CHAPTER 9. SOILâ AND STAINâRESISTANT TEXTILE FINISHES
- CHAPTER 10. ENVIRONMENTAL DEGRADATION OF FINISH MATERIALS
- AUTHOR INDEX
- SUBJECT INDEX