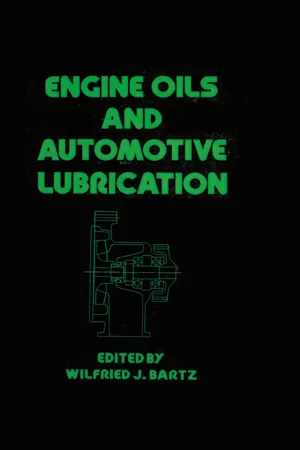
This is a test
- 832 pages
- English
- ePUB (mobile friendly)
- Available on iOS & Android
eBook - ePub
Engine Oils and Automotive Lubrication
Book details
Book preview
Table of contents
Citations
About This Book
Discusses all the major aspects of automotive and engine lubrication - presenting state-of-the-art advances in the field from both research and industrial perspectives. This book should be of interest to mechanical, lubrication and automotive engineers, automotive and machinery designers as well as undergraduate and graduate students in these fields.
Frequently asked questions
At the moment all of our mobile-responsive ePub books are available to download via the app. Most of our PDFs are also available to download and we're working on making the final remaining ones downloadable now. Learn more here.
Both plans give you full access to the library and all of Perlegoās features. The only differences are the price and subscription period: With the annual plan youāll save around 30% compared to 12 months on the monthly plan.
We are an online textbook subscription service, where you can get access to an entire online library for less than the price of a single book per month. With over 1 million books across 1000+ topics, weāve got you covered! Learn more here.
Look out for the read-aloud symbol on your next book to see if you can listen to it. The read-aloud tool reads text aloud for you, highlighting the text as it is being read. You can pause it, speed it up and slow it down. Learn more here.
Yes, you can access Engine Oils and Automotive Lubrication by Wilfried J. Bartz, Wilfried J. Bartz in PDF and/or ePUB format, as well as other popular books in Physical Sciences & Industrial & Technical Chemistry. We have over one million books available in our catalogue for you to explore.
Information
1. Oil Film Thickness in Engine Bearings
1.1 Measurement of Oil Film Thickness in Big-End Bearings and Its Relevance to Engine Oil Viscosity Classifications
1.2 Does the Automotive Industry Need a Standard Engine Test to Measure Journal Bearing Oil Film Thickness?
1.1 Measurement of Oil Film Thickness in Big-End Bearings and Its Relevance to Engine Oil Viscosity Classifications
Summary
Minimum oil film thickness (MOFT) measurements have been carried out in big-end bearings of V-6 and in-line four cylinder gasoline engines during engine operation. MOFT decreases with increasing crankshaft speed above 2000 r/min. The most severe, practical, steady-state operation is high-speed cruising. Maximum shear rates are in the region of 107 s-1 at 4000 r/min. The dynamic viscosities at a shear rate of 106 s-1 correlate significantly better with monograde MOFT data than with multigrade data; the correlation parameters for mono- and multigrade data are also significantly different. Although the dynamic viscosity measurement correlates with multigrade data better than the low-shear-rate kinematic viscosity, the differences are not always significant at the 95 % confidence level. Some other rheological parameter or combination of parameters may be better than either kinematic or dynamic viscosities.
1.1.1 Introduction
Until recently, the most widely used method of measuring journal bearing performance in operating gasoline or diesel engines was to measure bearing weight loss at the end of a test which inevitably involved operating under severe conditions of load and speed in order to obtain metal-to-metal contact (1.2). Such tests are the ultimate arbiter for assessing long-term durability performance. They are less than ideal, however, for studying the effects of oil rheology on journal bearing performance because of: (a) poor test repeatability; and (b) complications arising from operating under boundary/mixed lubrication conditions where chemical effects of the dispersant/inhibitor package complicate interpretation of the results in terms of oil rheology (1,2). Poor repeatability also makes bearing weight loss experiments unsatisfactory for studying the effects of bearing design on performance.
A preferred assessment of journal bearing performance is measurement of the oil film thickness during engine operationĀ·. The latter is critical since it ensures the bearing is subject to relevant dynamic loadings(as opposed to the use of tactically-loaded journal bearing rigs). Moreover, operation of the bearing under full-film hydrodynamic loading ensures only oil rheology effects are involved. Considerable progress has been made in the last ten years in instrumenting bearings of engines to allow measurement of oil film thickness during operation. Most of the activity has centred around main bearings (3, 4, 5, 6, 7, 8, 9). Big-end bearings, however, are of more interest because the combination of smaller bearing area and severe dynamic loadings make them more prone to field failure than main bearings. The problem of making electrical connections to the reciprocating big-end has been overcome by the use of light-weight, mechanical scissor linkages to support the wires and prevent their premature breakage (10, 11, 12, 13, 14).
As part of an extended CEC programme (15, 16, 17, 18) into the effects of oil viscometry on engine performance, the CEC Project Group PL-33 has initiated a study of the relationship between oil rheology and oil film thickness in the big-end bearings of two different engines. This study was initiated partly in response to a request from CCMC for further information on the role of high- temperature, high-shear viscosity (HTHSV) and other rheological properties on bearing performance, and partly to provide information which could be used as input to the debate on HTHSV classifications and limits in the SAE Viscosity Classification J300. There is considerable interest at the present time in a better characterization of the high-temperature performance of lubricants than that provided by the present low-shear, kinematic-viscosity limits in SAE J300. This interest stems from the trend towards lower viscosity oils for easier low-temperature starting and improved fuel economy. There is a concern that journal bearing durability problems may arise due to possible limitations of the kinematic viscosity as a guide to oil-rheological effects and its lack of relevance in terms of temperature and shear rate to critical areas of the engine. In journal bearings for instance shear rates in the region 105 s-1 to 107 s-1 occur.
1.1.2 Experimental
1.1.2.1 Engines
The connecting-rod, big-end bearings of two gasoline engines were instrumented. One engine was an in-line, four-cylinder, 2.3 litre, fuel-injected unit (hereinafter referred to as the 2.31 L-4 engine). The ungrooved big-end bearings were of lead/ bronze on a steel backing. There was a squirt hole in the upper shell for lubrication of the bore. The bearing corresponding to cylinder number 1 (pulley-end) was instrumented. The other engine was a 60°, V-6, fuel-injected unit of 2.8 litre capacity (referred to as the 2.81 V-6 engine). The ungrooved bearing material was copper/lead on a steel backing with an overlay of lead/tin. The cylinder of the instrumented bearing was in the middle of the bank. Special big-end bearing shells without the normal squirt hole in the upper shell were obtained from the engine manufacturer. Values of 40 μm and 25μm were used for the radial clearances of the instrumented big-end bearings of the 2.3 litre and 2.8 litre engines, respectively. These are estimated values based on pre-build information. Since the bearings have not been dismantled their present radial clearances are not known precisely. Table 1.1.1 gives further information on the engines and the bearing dimensions.
The engines were installed in a test cell, speed and torque being controlled by a dynamometer. Oil temperature was controlled at the gallery by passing the oil through an external oil cooler and electric heater.
Table 1.1.1: Test-engine data
2.31 L-4 | 2.81 V-6 | ||
Big-end bearing dimensions: | |||
length | , mm | 21.5 | 16.5 |
diameter | , mm | 48.5 | 54.0 |
area | , cm2 | 32.8 | 28.0 |
length:diameter ratio | 0.44 | 0.30 | |
shell thickness | , mm | 1.8 | 1.4 |
Maximum brake | |||
horsepower | , kW | 100 at 5100 r/min | 110 at 5800 r/min |
Maximum torque | ,NĀ·m | 205 at 3500 r/min | 216 at 4000 r/min |
Bore diameter | , mm | 95.5 | 93 |
Stroke | , mm | 80.3 | 68.5 |
Compression ratio | 9.0:1 | 9.2:1 | |
Radial clearance* | , μm | 40 | 25 |
* Estimated for the instrumented big-end bearing
1.1.2.2 Oil Film Thickness Measurement
The oil film thickness in the big-end bearing during engine operation was calculated from measurement of the total capacitance, C, of the oil film in the bearing. For a cylindrical bearing and shaft (i. e. no distortion) and in the absence of cavitation (i. e. uniform dielectric constant of the oil in the bearing), it can be shown (3) that:
(1) |
Here MOFT is the minimum oil film thickness at a given crankshaft position (see Fig. 1.1.1), R is the radial clearance, k the permittivity of free space, A the area of the bearing and e the dielectric constant of the oil at the temperature and pressure in the bearing.
In order to measure capacitance of the oil film in the bearing, the bearing shell was electrically insulated from the connecting rod by replacing ca. 200 μm of metal in the bearing housing by an equal thickness of alumina ceramic applied by plasma spraying (see. Fig. 1.1.1). The journal was earthed by means of copper braid held in tension over a pulley on the end of the crankshaft. The bearing shells and the journal now act as a cylindrical capacitor with the oil film as dielectric.
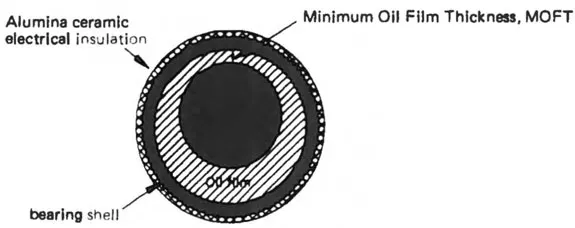
Figure 1.1.1: Electrical insulation of the big-end bearing shell for the measurement of the minimum oil film thickness, MOFT, as a function of crankangle
The oil film capacitance was measured continuously as a function of crankshaft angle by a capacitive divider circuit (3) in the case of the 2.3I L-4 engine and by a transformer ratio arm bridge circuit for the 2.8I V-6 engine (12). A check was made (19) that both techniques gave the same capacitance by replacing the ratio-arm circuit by a capacitive divider circuit for the 2.81 V-6 engine. The ac voltages applied to the bearing capacitor had frequencies of 100 kHz and 20 kHz for the 2.3 litre and 2.8 litre engines, respectively. The output voltage was used to calculate a c...
Table of contents
- Cover
- Half Title
- Title Page
- Copyright Page
- Table of Contents
- Preface
- 1. Oil Film Thickness in Engine Bearings
- 2. Base Oils
- 3. Additives and Mechanism of Effectiveness
- 4 Engine Oils and Their Evaluation/Engine Lubrication Aspects Engine Oils and Their Evaluation
- 5. Tractor Lubrication
- 6. Gear Lubrication
- 7. Lubricant Influence on Ceramic and Seal Materials
- Index
- The Authors