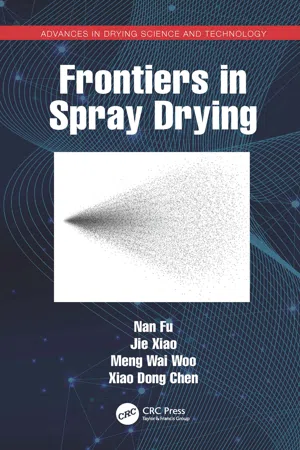
This is a test
- 100 pages
- English
- ePUB (mobile friendly)
- Available on iOS & Android
eBook - ePub
Frontiers in Spray Drying
Book details
Book preview
Table of contents
Citations
About This Book
This book covers the latest developments and advances in spray drying and describes how they impact the basic aspect of designing and operating spray dryers. This generic approach allows users to understand how different basic aspects of spray drying have advanced. Users will learn how to apply these advances in their own specific spray drying applications. This book also discusses the handling and control of spray dried products.
-
- Includes the latest techniques for use in the design and operation of spray drying operations
-
- Covers the basic operations of spray drying that can be applied to different applications of spray drying
-
- Discusses the handling and control of spray dried product qualities from a general approach, allowing readers to tailor these approaches to their own specific products
This book is aimed at professionals, researchers, and academics working in the fields of food, chemical, pharmaceutical, and industrial engineering.
Frequently asked questions
At the moment all of our mobile-responsive ePub books are available to download via the app. Most of our PDFs are also available to download and we're working on making the final remaining ones downloadable now. Learn more here.
Both plans give you full access to the library and all of Perlegoâs features. The only differences are the price and subscription period: With the annual plan youâll save around 30% compared to 12 months on the monthly plan.
We are an online textbook subscription service, where you can get access to an entire online library for less than the price of a single book per month. With over 1 million books across 1000+ topics, weâve got you covered! Learn more here.
Look out for the read-aloud symbol on your next book to see if you can listen to it. The read-aloud tool reads text aloud for you, highlighting the text as it is being read. You can pause it, speed it up and slow it down. Learn more here.
Yes, you can access Frontiers in Spray Drying by Nan Fu, Jie Xiao, Meng Wai Woo, Xiao Dong Chen in PDF and/or ePUB format, as well as other popular books in Medicine & Pharmacology. We have over one million books available in our catalogue for you to explore.
Information
1 Introduction
1.1 What is Spray Drying?
Spray drying is a common process used to convert liquid feed (e.g., milk) into solid particles (e.g., milk powders). It is a rapid process and can be made to huge scales (from grams of powder to tens of tonnes of powders made per hour per dryer) (see Figure 1.1.1). A typical spray drying process comprises atomization of liquid droplets into a hot air flow (in the order of liquid-to-air mass ratio of about 1:10) in the drying chamber and the collection of the resulting powder. Spray drying is the single stage that turns liquid droplets to particulate format (usually at least forming a dry surface around each droplet); then, the fluidized bed(s) can be connected up (in area D) to further dry these particles to the desired low moisture contents and shapes/structures (see Figure 1.1.2).


The evaporation rate of the moisture (or solvent content) is determined by the difference between the vapor pressure (or concentration) of water on the droplet surface and the vapor pressure (or concentration; or more generally the humidity) of the surrounding air. Since the water content (or solvent content) of the droplet is usually quite high, the drying process starts off more like evaporation of the pure solvent droplet. Conventionally, the literature tends to say that the droplet undergoes a constant drying rate period limited by mass transfer whereby moisture evaporates and a saturated vapor film forms on the droplet surface. The droplet surface temperature approaches the wet bulb temperature of the drying air. Eventually, the wet bulb temperature will be exceeded with the build-up of solid on the surface, restricting the solvent transfer as free as for pure solvent. When the droplet surface reaches a critical (low) solvent content, the second stage of the falling-rate drying period occurs as moisture/solvent diffusion within the particle becomes the rate-limiting step. As solid concentration continues to increase, the evaporation rate decreases as more energy is required to remove the same amount of moisture/solvent and the dropletâs temperature rises towards the dry bulb temperature. Increasing solid concentration increases the solvent transfer resistance, and the structure of the shell (with low permeability) influences the drying behavior. When the particle reaches the drying air temperature, the evaporation ceases at the equilibrium moisture/solvent content, which is dependent on the drying air temperature and relative humidity of the air used for drying (Kentish et al., 2005; Chen and Mujumdar, 2008).
The dried particles are then collected via a cyclone separator as product after all the stages of drying operations (spray dryer plus fluidized bed dryers in sequence) that (normally for agglomeration purposes) recycles the fines back to the main drying chamber (operated from the areas E and C in Figure 1.1.1). These fines are usually encouraged by design to intersect with the semi-dried droplets (with a sticky enough surface) to form agglomerates. These agglomerates are expected to perform better in the functionality tests, in particular the wetting, dispersion, and sinking.
Furthermore, in area A followed by area B, which may be called the liquid processing section, a component separation stage (as in milk processing), pasteurization stage (for many food liquids including milk), holding and vacuum flashing stages, and concentration stage (like falling film evaporation in milk processing) can selectively or all be implemented, depending on the nature of the product. We have already seen in Figure 1.1.1 a liquid (concentrate) heating stage just before the atomization stage to assist in controlling the atomization quality. The atomization in area C can be carried out using a pressure nozzle (or multiple nozzles), a single rotating disk atomizer, or a two-fluid atomizer (such as an airâliquid atomizer). Nozzle atomization demands a tall-form dryer (a much taller drying chamber due to the liquid trajectory effect) and rotating disk (or wheel) atomization requires a shorter but much wider chamber for drying (due to the droplets moving down spatially and the swirling air flow).
1.2 Chronological Development of the Process and Its Milestones
According to Santos et al. (2018) and as mentioned earlier, spray drying is a well-known particle production technology that consists of the transformation of a liquid material into dried particles. It takes advantage of a gaseous hot drying medium, usually air, and the exposure of the vast surface area of droplets to this gas medium (Masters, 1979; Cal and Sollohub, 2010). Its first observation can be dated back to 1860, when a primitive spray dryer device was patented by Samuel Percy in the United States in 1872 (Ortega-Rivas, Juliano, and Yan, 2006; Cal and Sollohub, 2010).
Ever since it was first discovered, the spray drying technique has been improved in its operational design and applications. In fact, the early spray drying devices lacked process efficiency and safety. After overcoming these issues, spray drying became a practical method for food industry purposes, ending up being used in milk powder production in the 1920s, which remains one of the most important applications until the present day. The evolution of spray drying was directly influenced by World War II, where there was an imperative need to reduce the weight and volume of food and other materials to be carried (Ortega-Rivas, Juliano, and Yan, 2006). As a result, spray drying has become an industry benchmark, namely in the production of dairy products. In the post-war period, the spray drying method continued to progress, finding application in the pharmaceutical, chemical, ceramic, and polymer industries (Vehring, Foss, and Lechuga-Ballesteros, 2007; Ortega-Rivas, Juliano, and Yan, 2006; Cal and Sollohub, 2010).
Even after more than a century of research, spray drying is still a target for study and innovation due to the increasing demand for complex particles with specific characteristics. This is considered a powerful technological process, since it brings feasibility to the production of free-flowing particles with well-defined particle size. Besides, bearing in mind the ability to use different feedstocks, as well as the techniqueâs high productivity and broad applications, makes it a more and more effective tool for the scientific community (Ortega-Rivas, Juliano, and Yan, 2006; Patel et al., 2009a,b).
Different arrangements of the gas flows and particle trajectories reduce energy losses as well as improving the ease of removing the particles from the gas medium (Huang, Mujumdar, and Chen, 2010). These arrangements can deviate considerably from the traditional design such as that shown in Figure 1.1.1. These new designs can be found at suppliersâ websites, such as GEA.
People today are not only concerned about the processing aspects of the technology; they are very concerned about how good quality products can be made, especially when the products are directly related to human nutrition and health. As such, product quality has to be related way back to the processes where it might be impacted adversely in a scientific analysis. This is not an easy task and has to be carried out systematically.
1.3 Motivation and Layout of the Book
Spray drying has been written about on a good number of occasions in the past. The current book has been made possible with a team of researchers who have been among the most active (and the most cited) in the area of spray drying and spray drying-related product research in recent years. The people working on this topic may well be referred to as âfrontiersmenâ. In particular, the senior author, X.D. Chen (XDC), has been involved in this field practically and academically since 1991, when he was associated with the milk powder section at New Zealand Dairy Research Institute, working for the former incarnation of todayâs Fonterra Dairy Coop Ltd. He was involved in the leaderships of some of the largest dryer renovations for the best quality products at the time. The team members have collaborated closely in spray drying research at various locations and have accumulated a wealth of knowledge in the area. The kinds of emphases in the current book reflect the expertise established among the authors. Although the authors have had close working experiences in R&D with the dairy powder industries in New Zealand and Australia, their knowledge and experiences have been limited when compared with the senior technical individuals well known in the industries worldwide; hence the inevitable drawbacks of this book.
Nevertheless, it is believed that the contents of this book fit well in attempting to fill the gaps in the fundamental understanding of the related processes as well as illustrating the kind of techniques employed in recent times in process diagnoses of the spray drying industry.
The book is laid out as follows: After the short introduction in Chapter 1, Chapter 2 presents the fundamentals of single droplet drying, which provides the essential understanding and modeling approaches. This the key to understanding the whole process of spray drying. Chapter 3 looks at information about spray drying configurations, including multistage drying with spray drying as the first stage. Chapter 4 covers mass and energy balances, which cannot be avoided in any spray drying descriptions. Here, stickiness, agglomeration, and CFD (Computational Fluid Dynamics) modeling are considered. Chapter 5 uniquely addresses a special development in spray drying, i.e., spray drying of mono-disperse droplets, which has helped immensely fundamental research into spray drying, which is usually affected badly by the wide particle size distribution. Finally, variations of spray drying with hot gas-like air, such as superheated steam spray drying, crystallization during spray drying and production of bio-actives, and antisolvent vapor precipitation spray drying, are described.
2 Droplet Drying Fundamentals
2.1 The Formation of Individual Particles during Spray Drying
Spray drying exhibits a number of advantages as a powder production approach, including little limitation on material, no requirement of a second solvent, rapid powder production, high production capacity, continuous and automated operation, and single-step production of microparticles encapsulating bio-active substances. It thus becomes the prevailing powder production approach in a variety of industries, such as food, pharmaceutical, and chemical. In these industries, the quality of powders is of paramount importance, in addition to the efficiency of the production process. The design of a spray drying process for a specific product needs to take into account chemical product engineering and chemical process engineering. Both aspects require understanding of how powders are formed by individual droplets inside the spray drying tower.
The basic transition to form a particle in spray drying is that w...
Table of contents
- Cover
- Half-Title
- Series
- Title
- Copyright
- Contents
- Advances in Drying Science and Technology
- Preface
- Authors
- Chapter 1 Introduction
- Chapter 2 Droplet Drying Fundamentals
- Chapter 3 Spray Dryer Designs Including Multistage
- Chapter 4 Mass and Energy Aspects of Spray Drying
- Chapter 5 Monodisperse Droplet Spray Drying
- Chapter 6 Advanced Applications of Spray Drying
- References
- Index