
eBook - ePub
Product Manufacturing and Cost Estimating using CAD/CAE
The Computer Aided Engineering Design Series
This is a test
- 570 pages
- English
- ePUB (mobile friendly)
- Available on iOS & Android
eBook - ePub
Product Manufacturing and Cost Estimating using CAD/CAE
The Computer Aided Engineering Design Series
Book details
Book preview
Table of contents
Citations
About This Book
This is the second part of a four part series that covers discussion of computer design tools throughout the design process. Through this book, the reader will...
- ...understand basic design principles and all digital design paradigms.
- ...understand CAD/CAE/CAM tools available for various design related tasks.
- ...understand how to put an integrated system together to conduct All Digital Design (ADD).
- ...understand industrial practices in employing ADD and tools for product development.
- Provides a comprehensive and thorough coverage of essential elements for product manufacturing and cost estimating using the computer aided engineering paradigm
- Covers CAD/CAE in virtual manufacturing, tool path generation, rapid prototyping, and cost estimating; each chapter includes both analytical methods and computer-aided design methods, reflecting the use of modern computational tools in engineering design and practice
- A case study and tutorial example at the end of each chapter provides hands-on practice in implementing off-the-shelf computer design tools
- Provides two projects at the end of the book showing the use of Pro/ENGINEERÂŽ and SolidWorksÂŽ to implement concepts discussed in the book
Frequently asked questions
At the moment all of our mobile-responsive ePub books are available to download via the app. Most of our PDFs are also available to download and we're working on making the final remaining ones downloadable now. Learn more here.
Both plans give you full access to the library and all of Perlegoâs features. The only differences are the price and subscription period: With the annual plan youâll save around 30% compared to 12 months on the monthly plan.
We are an online textbook subscription service, where you can get access to an entire online library for less than the price of a single book per month. With over 1 million books across 1000+ topics, weâve got you covered! Learn more here.
Look out for the read-aloud symbol on your next book to see if you can listen to it. The read-aloud tool reads text aloud for you, highlighting the text as it is being read. You can pause it, speed it up and slow it down. Learn more here.
Yes, you can access Product Manufacturing and Cost Estimating using CAD/CAE by Kuang-Hua Chang in PDF and/or ePUB format, as well as other popular books in Technology & Engineering & Mechanical Engineering. We have over one million books available in our catalogue for you to explore.
Information
Chapter 1
Introduction to e-Design
Chapter Outline
1.1 Introduction
1.2 The e-Design Paradigm
1.3 Virtual Prototyping
1.3.1 Parameterized CAD Product Model
Parameterized Product Model
Analysis Models
Motion Simulation Models
1.3.2 Product Performance Analysis
Motion Analysis
Structural Analysis
Fatigue and Fracture Analysis
Product Reliability Evaluations
1.3.3 Product Virtual Manufacturing
1.3.4 Tool Integration
1.3.5 Design Decision Making
Design Problem Formulation
Design Sensitivity Analysis
Parametric Study
Design Trade-Off Analysis
What-If Study
1.4 Physical Prototyping
1.4.1 Rapid Prototyping
1.4.2 CNC Machining
1.5 Example: Simple Airplane Engine
System-Level Design
Component-Level Design
Design Trade-Off
Rapid Prototyping
1.6 Example: High-Mobility Multipurpose Wheeled Vehicle
Hierarchical Product Model
Preliminary Design
Detail Design
Design Trade-Off
1.7 Summary
Questions and Exercises
References
Sources
Conventional product development employs a design-build-test philosophy. The sequentially executed development process often results in prolonged lead times and elevated product costs. The proposed e-Design paradigm employs IT-enabled technology for product design, including virtual prototyping (VP) to support a cross-functional team in analyzing product performance, reliability, and manufacturing costs early in product development, and in making quantitative trade-offs for design decision making. Physical prototypes of the product design are then produced using the rapid prototyping (RP) technique and computer numerical control (CNC) to support design verification and functional prototyping, respectively.
e-Design holds potential for shortening the overall product development cycle, improving product quality, and reducing product costs. It offers three concepts and methods for product development:
⢠Bringing product performance, quality, and manufacturing costs together early in design for consideration.
⢠Supporting design decision making based on quantitative product performance data.
⢠Incorporating physical prototyping techniques to support design verification and functional prototyping.
1.1 Introduction
A conventional product development process that is usually conducted sequentially suffers the problem of the design paradox (Ullman 1992). This refers to the dichotomy or mismatch between the design engineerâs knowledge about the product and the number of decisions to be made (flexibility) throughout the product development cycle (see Figure 1.1). Major design decisions are usually made in the early design stage when the product is not very well understood. Consequently, engineering changes are frequently requested in later product development stages, when product design evolves and is better understood, to correct decisions made earlier.
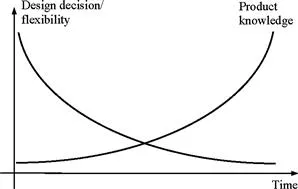
FIGURE 1.1 The design paradox.
Conventional product development is a design-build-test process. Product performance and reliability assessments depend heavily on physical tests, which involve fabricating functional prototypes of the product and usually lengthy and expensive physical tests. Fabricating prototypes usually involves manufacturing process planning and fixtures and tooling for a very small amount of production. The process can be expensive and lengthy, especially when a design change is requested to correct problems found in physical tests.
In conventional product development, design and manufacturing tend to be disjoint. Often, manufacturability of a product is not considered in design. Manufacturing issues usually appear when the design is finalized and tests are completed. Design defects related to manufacturing in process planning or production are usually found too late to be corrected. Consequently, more manufacturing procedures are necessary for production, resulting in elevated product cost.
With this highly structured and sequential process, the product development cycle tends to be extended, cost is elevated, and product quality is often compromised to avoid further delay. Costs and the number of engineering change requests (ECRs) throughout the product development cycle are often proportional according to the pattern shown in Figure 1.2. It is reported that only 8% of the total product budget is spent for design; however, in the early stage, design determines 80% of the lifetime cost of the product (Anderson 1990). Realistically, todayâs industries will not survive worldwide competition unless they introduce new products of better quality, at lower cost, and with shorter lead times. Many approaches and concepts have been proposed over the years, all with a common goalâto shorten the product development cycle, improve product quality, and reduce product cost.
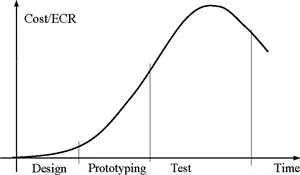
FIGURE 1.2 Cost/ECR versus time in a conventional design cycle.
A number of proposed approaches are along the lines of virtual prototyping (Lee 1999), which is a simulation-based method that helps engineers understand product behavior and make design decisions in a virtual environment. The virtual environment is a computational framework in which the geometric and physical properties of products are accurately simulated and represented. A number of successful virtual prototypes have been reported, such as Boeingâs 777 jetliner, General Motorsâ locomotive engine, Chryslerâs automotive interior design, and the Stockholm Metroâs Car 2000 (Lee 1999). In addition to virtual prototyping, the concurrent engineering (CE) concept and methodology have been studied and developed with emphasis on subjects such as product life cycle design, design for X-abilities (DFX), integrated product and process development (IPPD), and Six Sigma (Prasad 1996).
Although significant research has been conducted in improving the product development process, and successful stories have been reported, industry at large is not taking advantage of new product development paradigms. The main reason is that small and mid-size companies cannot afford to develop an in-house computer tool environment like those of Boeing and the Big-Three automakers. On the other hand, commercial software tools are not tailored to meet the specific needs of individual companies; they often lack proper engineering capabilities to support specific product development needs, and most of them are not properly integrated. Therefore, companies are using commercial tools to support segments of their product development without employing the new design paradigms to their full advantage.
The e-Design paradigm does not supersede any of the approaches discussed. Rather, it is simply a realization of concurrent engineering through virtual and physical prototyping with a systema...
Table of contents
- Cover image
- Title page
- Table of Contents
- Copyright
- Dedications
- Preface
- About the Author
- About the Cover
- Acknowledgements
- Chapter 1. Introduction to e-Design
- Chapter 2. Virtual Machining
- Chapter 3. Toolpath Generation
- Chapter 4. Sheet Metal Forming Simulation
- Chapter 5. Rapid Prototyping
- Chapter 6. Product Cost Estimating
- Project S4: Machining Simulation Using CAMWorks
- Project P4: Machining Simulation Using Pro/MFG
- Project M4: Machining Simulation Using Mastercam
- Index