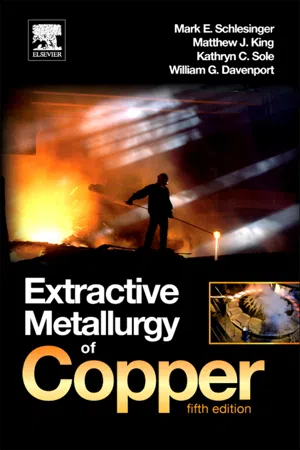
Extractive Metallurgy of Copper
- 472 pages
- English
- ePUB (mobile friendly)
- Available on iOS & Android
Extractive Metallurgy of Copper
About This Book
This multi-author new edition revises and updates the classic reference by William G. Davenport et al (winner of, among other awards, the 2003 AIME Mineral Industry Educator of the Year Award "for inspiring students in the pursuit of clarity"), providing fully updated coverage of the copper production process, encompassing topics as diverse as environmental technology for wind and solar energy transmission, treatment of waste by-products, and recycling of electronic scrap for potential alternative technology implementation. The authors examine industrially grounded treatments of process fundamentals and the beneficiation of raw materials, smelting and converting, hydrometallurgical processes, and refining technology for a mine-to-market perspective - from primary and secondary raw materials extraction to shipping of rod or billet to customers. The modern coverage of the work includes bath smelting processes such as Ausmelt and Isasmelt, which have become state-of-the-art in sulfide concentrate smelting and converting.
- Drawing on extensive international industrial consultancies within working plants, this work describes in depth the complete copper production process, starting from both primary and secondary raw materials and ending with rod or billet being shipped to customers
- The work focuses particularly on currently-used industrial processes used to turn raw materials into refined copper metal rather than ideas working 'only on paper'
- New areas of coverage include the environmentally appropriate uses of copper cables in power transmission for wind and solar energy sources; the recycling of electronic scrap as an important new feedstock to the copper industry, and state-of-the-art Ausmelt and Isasmelt bath smelting processes for sulfide concentrate smelting and converting
Frequently asked questions
Information
1.1. Introduction
![]() |
FIGURE 1.1 Open pit Cu mine. Note the new blast holes, top right, and blasted ore to the left of them. The shovel is placing blasted ore in the truck from where it will go to processing. The water truck is suppressing dust. The front end loader is cleaning up around the shovel. The shovel is electric. Its power wire mostly lies on the surface except over the wire bridge under which all vehicles travel to and from the shovel. (Photo courtesy of Freeport-McMoRan Copper & Gold Inc.). |
![]() |
FIGURE 1.2 Main processes for extracting copper from sulfide ores. Parallel lines indicate alternative processes. āPrincipally Mitsubishi and Vanyukov smelting. |
![]() |
FIGURE 1.3 Flowsheet for leaching oxide and Cu2S ores. The dissolved Cu is recovered by solvent extraction purification/strengthening then electrowinning. Leaching accounts for ~20% of primary (from ore) copper production. |
1.2. Extracting Copper from CopperāIronāSulfide Ores
1.2.1. Concentration by Froth Flotation (Chapter 3 and Chapter 4)
![]() |
FIGURE 1.4 Schematic view of flotation cell. Reagents cause CuāFe sulfide and Cu sulfide minerals in the ore to attach to rising air bubbles, which are then collected in a short-lived froth. This froth is de-watered to become concentrate. The un-floated waste passes through several cells before being discarded as a final tailing. Many types and sizes (up to 300 m3) of cell are used. |
1.2.2. Matte Smelting (Chapter 5, Chapter 6 and Chapter 9)
![]() |
FIGURE 1.5 Outokumpu oxygen-enriched air flash furnace. Flash furnaces are typically 20 m long and 7 m wide. They smelt 1000ā3000 to... |
Table of contents
- Cover image
- Table of Contents
- Frontmatter
- Copyright
- Preface
- Preface to the Fourth Edition
- Preface to the Third Edition
- Preface to the Second Edition
- Preface to the First Edition
- Chapter 1. Overview
- Chapter 2. Production and Use
- Chapter 3. Production of High Copper Concentrates ā Introduction and Comminution
- Chapter 4. Production of Cu Concentrate from Finely Ground Cu Ore
- Chapter 5. Matte Smelting Fundamentals
- Chapter 6. Flash Smelting
- Chapter 7. Submerged Tuyere Smelting
- Chapter 8. Converting of Copper Matte
- Chapter 9. Bath Matte Smelting
- Chapter 10. Direct-To-Copper Flash Smelting
- Chapter 11. Copper Loss in Slag
- Chapter 12. Capture and Fixation of Sulfur
- Chapter 13. Fire Refining (S and O Removal) and Anode Casting
- Chapter 14. Electrolytic Refining
- Chapter 15. Hydrometallurgical Copper Extraction
- Chapter 16. Solvent Extraction
- Chapter 17. Electrowinning
- Chapter 18. Collection and Processing of Recycled Copper
- Chapter 19. Chemical Metallurgy of Copper Recycling
- Chapter 20. Melting and Casting
- Chapter 21. Byproduct and Waste Streams
- Chapter 22. Costs of Copper Production
- Index