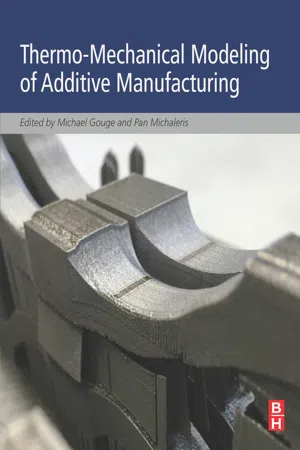
- 294 pages
- English
- ePUB (mobile friendly)
- Available on iOS & Android
Thermo-Mechanical Modeling of Additive Manufacturing
About This Book
Thermo-mechanical Modeling of Additive Manufacturing provides the background, methodology and description of modeling techniques to enable the reader to perform their own accurate and reliable simulations of any additive process. Part I provides an in depth introduction to the fundamentals of additive manufacturing modeling, a description of adaptive mesh strategies, a thorough description of thermal losses and a discussion of residual stress and distortion. Part II applies the engineering fundamentals to direct energy deposition processes including laser cladding, LENS builds, large electron beam parts and an exploration of residual stress and deformation mitigation strategies. Part III concerns the thermo-mechanical modeling of powder bed processes with a description of the heat input model, classical thermo-mechanical modeling, and part scale modeling.
The book serves as an essential reference for engineers and technicians in both industry and academia, performing both research and full-scale production. Additive manufacturing processes are revolutionizing production throughout industry. These technologies enable the cost-effective manufacture of small lot parts, rapid repair of damaged components and construction of previously impossible-to-produce geometries. However, the large thermal gradients inherent in these processes incur large residual stresses and mechanical distortion, which can push the finished component out of engineering tolerance. Costly trial-and-error methods are commonly used for failure mitigation. Finite element modeling provides a compelling alternative, allowing for the prediction of residual stresses and distortion, and thus a tool to investigate methods of failure mitigation prior to building.
- Provides understanding of important components in the finite element modeling of additive manufacturing processes necessary to obtain accurate results
- Offers a deeper understanding of how the thermal gradients inherent in additive manufacturing induce distortion and residual stresses, and how to mitigate these undesirable phenomena
- Includes a set of strategies for the modeler to improve computational efficiency when simulating various additive manufacturing processes
- Serves as an essential reference for engineers and technicians in both industry and academia
Frequently asked questions
Information
Acknowledgments
Chapter 1
Chapter 2
Chapter 3
Chapter 4
Chapter 6
Chapter 7
Chapter 8
Chapter 9
Chapter 10
Chapter 11
Chapter 12
Chapter 13
Chapter 14
Chapter 15
An Introduction to Additive Manufacturing Processes and Their Modeling Challenges
Abstract
Keywords
1.1 Motivation
Table of contents
- Cover image
- Title page
- Table of Contents
- Copyright
- List of Contributors
- About the Editors
- Acknowledgments
- Part I: The Fundamentals of Additive Manufacturing Modeling
- Chapter 1: An Introduction to Additive Manufacturing Processes and Their Modeling Challenges
- Chapter 2: The Finite Element Method for the Thermo-Mechanical Modeling of Additive Manufacturing Processes
- Part II: Thermomechanical Modeling of Direct Energy Deposition Processes
- Chapter 3: Convection Boundary Losses During Laser Cladding
- Chapter 4: Conduction Losses due to Part Fixturing During Laser Cladding
- Chapter 5: Microstructure and Mechanical Properties of AM Builds
- Chapter 6: Understanding Microstructure Evolution During Additive Manufacturing of Metallic Alloys Using Phase-Field Modeling
- Chapter 7: Modeling Microstructure of AM Processes Using the FE Method
- Chapter 8: Thermo-Mechanical Modeling of Thin Wall Builds using Powder Fed Directed Energy Deposition
- Chapter 9: Residual Stress and Distortion Modeling of Electron Beam Direct Manufacturing Ti-6Al-4V
- Chapter 10: Thermo-Mechanical Modeling of Large Electron Beam Builds
- Chapter 11: Mitigation of Distortion in Large Additive Manufacturing Parts
- Part III: Thermomechanical Modeling of Powder Bed Processes
- Chapter 12: Development and Numerical Verification of a Dynamic Adaptive Mesh Coarsening Strategy for Simulating Laser Power Bed Fusion Processes
- Chapter 13: Thermomechanical Model Development and In Situ Experimental Validation of the Laser Powder-Bed Fusion Process
- Chapter 14: Study of the Evolution of Distortion During the Powder Bed Fusion Build Process Using a Combined Experimental and Modeling Approach
- Chapter 15: Validation of the American Makes Builds
- Appendix A: Appendix
- Index