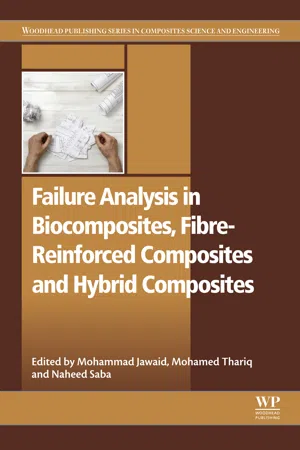
Failure Analysis in Biocomposites, Fibre-Reinforced Composites and Hybrid Composites
- 274 pages
- English
- ePUB (mobile friendly)
- Available on iOS & Android
Failure Analysis in Biocomposites, Fibre-Reinforced Composites and Hybrid Composites
About This Book
Failure Analysis in Biocomposites, Fibre-Reinforced Composites and Hybrid Composites covers key aspects of fracture and failure in natural/synthetic fiber reinforced polymer based composite materials, ranging from crack propagation, to crack growth, and from notch-size effect, to damage-tolerant design. The book describes a broad range of techniques and strategies for the compositional and failure analysis of polymeric materials and products. It also illustrates the application of analytical methods for solving commonly encountered problems. Topics of interest include failure analysis, mechanical and physical properties, structural health monitoring, durability and life prediction, modelling of damage processes of natural fiber, synthetic fibers, and more.
Written by leading experts in the field, and covering composite materials developed from different natural fibers and their hybridization with synthetic fibers, the book's chapters provide cutting-edge, up-to-date research on the characterization, analysis and modelling of composite materials.
- Contains contributions from leading experts in the field
- Discusses recent progress on failure analysis, SHM, durability, life prediction and the modelling of damage in natural fiber-based composite materials
- Covers experimental, analytical and numerical analysis
- Provides detailed and comprehensive information on mechanical properties, testing methods and modelling techniques
Frequently asked questions
Information
Fatigue delamination of carbon fiber-reinforced polymer-matrix composites
Abstract
Keywords
1.1. Introduction
Table of contents
- Cover image
- Title page
- Table of Contents
- Copyright
- Dedication
- List of contributors
- About the editors
- Preface
- 1. Fatigue delamination of carbon fiber-reinforced polymer-matrix composites
- 2. Investigation of the deformation behavior of epoxy-based composite materials
- 3. Effects of strain rate on failure mechanisms and energy absorption in polymer composites
- 4. Bolted joint behavior of hybrid composites
- 5. Failure analysis and the optimal toughness design of sheepāwool reinforced epoxy composites
- 6. Edge crack effect on tensile behavior of diversified wood particulate composites
- 7. Investigation of mechanical testing on hybrid composite materials
- 8. Cracks, microcracks, and fracture toughness of polymer composites: Formation, testing method, nondestructive detection, and modifications
- 9. Shape memory polymer and its composites as morphing materials
- 10. Fabric-Reinforced Cementitious Matrix (FRCM) composites: Mechanical behavior and application to masonry walls
- 11. Failure analysis in hybrid composites prepared using industrial wastes
- Index