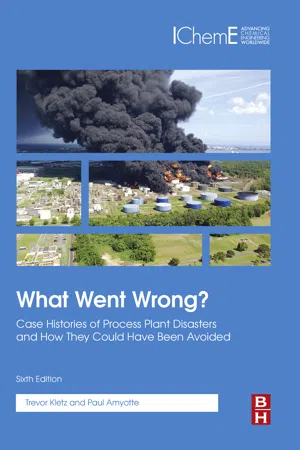
eBook - ePub
What Went Wrong?
Case Histories of Process Plant Disasters and How They Could Have Been Avoided
This is a test
- 840 pages
- English
- ePUB (mobile friendly)
- Available on iOS & Android
eBook - ePub
What Went Wrong?
Case Histories of Process Plant Disasters and How They Could Have Been Avoided
Book details
Book preview
Table of contents
Citations
About This Book
What Went Wrong? 6th Edition provides a complete analysis of the design, operational, and management causes of process plant accidents and disasters. Co-author Paul Amyotte has built on Trevor Kletz's legacy by incorporating questions and personal exercises at the end of each major book section. Case histories illustrate what went wrong and why it went wrong, and then guide readers in how to avoid similar tragedies and learn without having to experience the loss incurred by others. Updated throughout and expanded, this sixth edition is the ultimate resource of experienced-based analysis and guidance for safety and loss prevention professionals.
- 20% new material and updating of existing content with parts A and B now combined
- Exposition of topical concepts including Natech events, process security, warning signs, and domino effects
- New case histories and lessons learned drawn from other industries and applications such as laboratories, pilot plants, bioprocess plants, and electronics manufacturing facilities
Frequently asked questions
At the moment all of our mobile-responsive ePub books are available to download via the app. Most of our PDFs are also available to download and we're working on making the final remaining ones downloadable now. Learn more here.
Both plans give you full access to the library and all of Perlegoās features. The only differences are the price and subscription period: With the annual plan youāll save around 30% compared to 12 months on the monthly plan.
We are an online textbook subscription service, where you can get access to an entire online library for less than the price of a single book per month. With over 1 million books across 1000+ topics, weāve got you covered! Learn more here.
Look out for the read-aloud symbol on your next book to see if you can listen to it. The read-aloud tool reads text aloud for you, highlighting the text as it is being read. You can pause it, speed it up and slow it down. Learn more here.
Yes, you can access What Went Wrong? by Trevor Kletz,Paul Amyotte in PDF and/or ePUB format, as well as other popular books in Technology & Engineering & Chemical & Biochemical Engineering. We have over one million books available in our catalogue for you to explore.
Information
Part I
Introduction
Chapter 1
Case histories and their use in enhancing process safety knowledge
Abstract
This chapter opens the Introduction section of the book. It describes how process incidents are caused by a number of factors ranging from the immediate technical level to deeper management system and cultural factors. While there can sometimes be long- lasting, exceptionally negative impacts from these events, the goal in studying case histories is to learn lessons for future prevention, not to point fingers and lay blame.
Keywords
Case histories; Case studies; Process safety management; Process safety culture; Lessons learned
To paraphrase G. Santayana, one learns from history or one is doomed to repeat ita.
Crowl and Louvar [1]
AIChE Engage (a mobile platform for connecting AIChE members) contained an online discussion in early January 2018 framed around these questions: How can we mitigate risk in industry? What is the impact of a safety team on avoiding incidents? [2].
Responses included the following comments (edited where appropriate):
- ā Books have been written to answer your question. But in all the process safety incidents I have ever investigated, one or both of these are recurring contributors: (i) failure of operational discipline (usually a failure to follow procedures), and (ii) failure to maintain equipment (primary containment integrity and/or safety-critical equipment) in good working order. So the surest way a safety team can reduce risk is to ensure the fundamentals of following procedures and maintaining equipment are central to the organization's culture [3].
- ā As a risk engineer, I often advise clients to observe good PSM [Process Safety Management] and loss prevention. But the level of PSM awareness varies from oil majors to small plants. It is interesting to note that oil majors with good procedures and maintenance programs may suffer a major loss by not following them, while a small plant with a less sophisticated system may not suffer a loss because their systems of operation and maintenance are less complicated and easily followed by the operators [4].
- ā Many of the reasons why the Bhopal gas disaster occurred are still observed in recent times. The CSB [US Chemical Safety Board] investigation report of the Caribbean Petroleum tank terminal explosion and multiple fires (released by the CSB in October 2015) finds that systemic failures at CAPECO [Caribbean Petroleum Corporation] included (highlighted failures are the same failures that happened in Bhopal): (i) history of poorly maintaining terminal operations, (ii) inherent financial pressure to fill the tanks within the Planning Department's stipulated time, which was at odds with safety, (iii) failure to learn from previous overfill incidents at the facility, (iv) lack of preventive maintenance for the malfunctioning float and tape gauges, (v) unreliable computer for calculating tank fill times, (vi) lack of overfill prevention safeguards as an independent alarm, (vii) lack of formal procedures for tank-filling operations and managers, (viii) insufficient mechanical integrity program for safety-critical equipment, and (ix) poor adherence to human factor principles for safety-critical equipment [5].
- ā I think a safety team is a vital part of any safety program. If a priority of your company is to keep your plant running, you hire engineers. In the same way, if your company wants safety as a core focus, it should have dedicated safety personnel. The safety team also has to focus on getting the entire staff to buy into the importance of safety, however, as it only takes one person not doing their job the right way/dangerously to jeopardize many others. Some of the ways that an old employer of mine mitigated risk were PHAs [Process Hazard Analyses], safety audits, PSSRs [Pre-Startup Safety Reviews], and a robust MOC [Management of Change] process [6].
- ā If you have not heard of the name Trevor Kletz, you should look him up and read him. I will give you just one teaser from his many tidbits of wisdom concerning process safety and inherent safety in chemical processing: āif you don't have it, it can't leakā [7].
- ā Interestingly, I just finished reading a book titled āInviting DisasterāLessons from the Edge of Technologyā. The author, James R. Chiles, delves into various disasters, Bhopal included, and finds that in many cases, the cause of the mishaps was something that occurred prior to the actual incident. The Apollo 13 incident started with a damaged pipe that was undetected by the supplier, followed by unauthorized procedures after testing that only became apparent when the oxygen tank was stirred. In an incident like the Apollo 13 near-disaster (in terms of loss of life), literally every nut and bolt and piece of circuitry is examined with a fine-toothed comb by investigators. Unfortunately, most plant disasters are not subject to such rigorous analysis; a cause(s) is found, and corrections or improvements are made. In many cases a plant will resume operation [8].
- ā Some incidents occur because of lack of knowledge. Contractors sometimes are not trained very well. They are given directions, but need more. I am thinking about how to enhance safety culture in industry [2].
Embodied in the above quotes are a number of topics that are highly relevant to the discussion in this book: operating procedures, equipment maintenance, process safety management systems, specific PSM elements such as management of change and mechanical integrity, learning from previous incidents, inherent safety, root-cause analysis, incident investigati...
Table of contents
- Cover image
- Title page
- Table of Contents
- Copyright
- Dedication
- Dedications and quotes
- Preface to the sixth edition
- Preface to the fifth edition
- Acknowledgments
- Units and nomenclature
- Part I: Introduction
- Part II: Maintenance and operations
- Part III: Equipment and materials of construction
- Part IV: Hazards and loss of containment
- Part V: Knowledge and communication
- Part VI: Design and modifications
- Part VII: Conclusion
- Appendix A: Relative frequencies of incidents
- Appendix B: Why should we publish accident reports?
- Appendix C: Some tips for accident investigators
- Appendix D: Recommended reading
- Appendix E: Afterthoughts
- Index