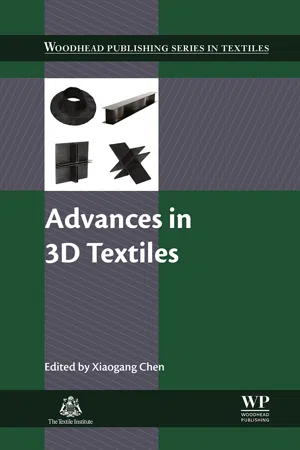
This is a test
- 404 pages
- English
- ePUB (mobile friendly)
- Available on iOS & Android
eBook - ePub
Advances in 3D Textiles
Book details
Book preview
Table of contents
Citations
About This Book
Advances in 3D Textiles presents the most recent advances in the production of three-dimensional fibrous structures and how their use has resulted in the creation of novel fabrics and applications. The text covers a wide range of fabric types, including their structures, properties, and uses in the textiles industry.
Beginning with the various types of woven three-dimensional fabrics, the text then examines 3-D knitted, braided, and non-woven textiles, and the main applications and uses of three-dimensional textiles.
- Presents the most recent advances in the production of three-dimensional fibrous structures and how their use has resulted in the creation of novel fabrics and applications
- Examines many types of 3-D textiles, including knitted, braided, and non-woven textiles, and the main uses of three-dimensional textiles
- Covers their structures, properties, and uses within the textiles industry
Frequently asked questions
At the moment all of our mobile-responsive ePub books are available to download via the app. Most of our PDFs are also available to download and we're working on making the final remaining ones downloadable now. Learn more here.
Both plans give you full access to the library and all of Perlegoās features. The only differences are the price and subscription period: With the annual plan youāll save around 30% compared to 12 months on the monthly plan.
We are an online textbook subscription service, where you can get access to an entire online library for less than the price of a single book per month. With over 1 million books across 1000+ topics, weāve got you covered! Learn more here.
Look out for the read-aloud symbol on your next book to see if you can listen to it. The read-aloud tool reads text aloud for you, highlighting the text as it is being read. You can pause it, speed it up and slow it down. Learn more here.
Yes, you can access Advances in 3D Textiles by Xiaogang Chen in PDF and/or ePUB format, as well as other popular books in Technology & Engineering & Materials Science. We have over one million books available in our catalogue for you to explore.
Information
1
Introduction
J.W.S. Hearle TexEng Software Ltd, Manchester, UK
Abstract
3D textiles, which have grown in importance since 1980, have 3D forms either in overall shape or in multilayer internal structure or both. They may be woven, braided, knitted, nonwoven, stitched, embroidered or in new special forms and may be used as flexible fabrics or rigid composites. Diverse uses include aerospace, automotive, military, sport, medical, protection, filtration, paper-making and geotextiles. There are opportunities in construction. For the future, a current engineering CAD culture needs to be developed, the market expanded in both specialist, high-performance and less demanding high-volume applications, and reliable sources of supply established.
Keywords
Weaving
Braiding
Knitting
Composites, Spacer fabrics
Technical applications
1.1 Introduction
1.1.1 Definition of 3D textiles
All textile materials have an internal 3D structure of fibres and, usually, yarns, but for practical purposes most have the form of single-layer, planar or sometimes cylindrical 2D sheets. What we now refer to as 3D fabrics have either an overall 3D shape or a more complex internal 3D structure or both. They include the following forms:
⢠Single-layer materials with an overall shape
⢠Multilayer hollow materials
⢠Solid planar materials with multiple layers
⢠Solid multilayer materials with an overall 3D shape
These fabrics may be woven, knitted, braided or nonwoven or made in new ways.
1.1.2 Traditional examples
Some 3D fabrics have a long history. Velvets are made as two woven fabric layers linked by spacer threads before cutting to expose a pile. Multilayer weaves with two or three layers are used for some technical fabrics, such as those used in filtration or papermaking. Hand-knitted socks have a 3D shape, turning at the heel.
1.1.3 Innovation in the 1980s
A wave of innovation started around 1980 and was reported on 10 years later (Chou and Ko, 1989; Hearle and Du, 1990). The impetus was the growth of composite materials into more demanding engineering applications. Table 1.1 shows the methods of making composites following the development of fibre-reinforced plastic (FRP) with glass fibre in the 1930s. There are limitations both in the composite properties and the manufacturing economics. 3D woven fabrics have several advantages: (1) better through-thickness performance than the separate layers of previous composites; (2) production close to the shape of the final composite and (3) ease of handling for consolidation.
Table 1.1
Conventional composite manufacture
Random fibre placement | Dispersed short-fibre injection mould Lay-up of fibre mats Nonwoven preforms |
Simple filament laminates | Lay-up of prepreg Filament winding |
Interlaced laminates | Simple woven fabrics Knitted fabrics with laid-in yarns |
3D shell structures | Filament winding Press-forming Fabric draping |
Problems: 3D short-fibre moulding: orientation; fibre length.
Laminates, essentially 2D: manually intensive lay-up; weak through thickness.
Press-forming and fabric draping: limited deformability.
The interest has widened in varying degrees to both composites bonded by a matrix and noncomposites without bonding between fibres and yarns. The improvements in technology and the diversity of products are shown by the Conferences on 3D Fabrics and Their Applications organised by TexEng Software Ltd. (2008ā2013).
1.2 Range of 3D textiles
1.2.1 Woven
The definition of what is a 3D weave is controversial. The broadest definition, which may be regarded as too inclusive and would include some braids or even knits, would be a structure that has yarns crossing in three mutually perpendicular X, Y and Z directions or, at least, with components through the thickness (Z axis). The extreme example, which Ko (1989) terms an orthogonal nonwoven (though that does not accord with the usual understanding of the term nonwovens), would have threads crossing one another but no interlacing. A more useful definition would be a fabric that was made on a conventional or modified weaving machine. The most restrictive definition, which Khokar has called noobing, requires interlacings not only between the X and Y directions but also with the Z direction. This involves dual-direction shedding in which warp yarns are both moved up and down, as in conventional weaving, but also from side to side to interlace with through-the-thickness yarns.
Fukuta et al. (1982) described a ādirect methodā in which the axial (Y) yarns are positioned through a rectangular, perforated comber-board and then the X and Z yarns are inserted between the Y yarns. There is no interlacing, and the process is slow. The ādirect methodā described by Stover et al. (1971) looks more like a weaving machine. Neither has survived.
Weaving machines specially designed for making 3D fabrics have been developed by Nandan Khokar for the company BITEAM and by Mansour Mohamed for 3Tex Inc., though that company is no longer operating. A more productive approach, which is used by the University of Manchester, Bally Ribbon Mills Inc., T.E.A.M. Inc. and others, employs regular weaving machines from commercial suppliers, possibly with some modifications.
Figure 1.1 illustrates various forms of 3D woven fabrics, solid with uniform thickness, solid shaped, hollow, multifaceted and domed. Many more complicated forms, such as T or I beams, can be made. Weaving can be regarded as the mainstream route to 3D composite preforms.

Figure 1.1 Examples of woven 3D fabrics.
The design of 3D weaves is more complicated than for 2D weaves, but a program, Weave Engineer, based on mathematical principles by Chen et al. (1996), is available from TexEng Software Ltd. It is easy to use in a series of steps. A typical output, which can be used as input to the control software of a weaving machine, is shown in Figure 1.2.
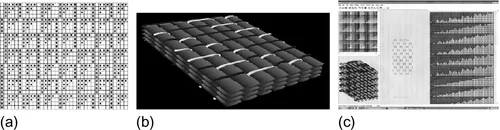
Figure 1.2 (a and b) Weave design and structure for orthogonal interlock. (c) Hollow structure.
1.2.2 Braids
In their simplest form, braids consist of single layers of yarns that are diagonally interlaced by moving supply packages around one another, typically by horn gears. Tubular 3D shapes with varying diameters can be made by braiding over a mandrel (Du and Popper, 1994; Figure 1.3(a)), and other variants are possible. For solid braids, the forms ...
Table of contents
- Cover image
- Title page
- Table of Contents
- Copyright
- List of Contributors
- Woodhead Publishing Series in Textiles
- 1: Introduction
- Part One: 3D Woven Textiles
- Part Two: 3D Knitted, Braided and Nonwoven Textiles
- Part Three: 3D Textiles for Industrial Applications
- Index