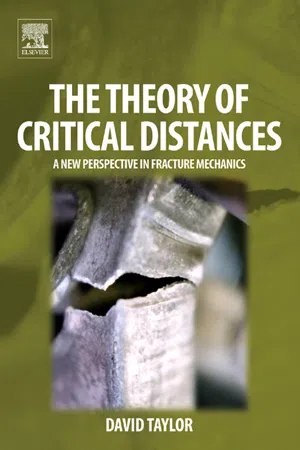
- 306 pages
- English
- ePUB (mobile friendly)
- Available on iOS & Android
About This Book
Critical distance methods are extremely useful for predicting fracture and fatigue in engineering components. They also represent an important development in the theory of fracture mechanics. Despite being in use for over fifty years in some fields, there has never been a book about these methods ā until now.
So why now? Because the increasing use of computer-aided stress analysis (by FEA and other techniques) has made these methods extremely easy to use in practical situations. This is turn has prompted researchers to re-examine the underlying theory with renewed interest.
The Theory of Critical Distances begins with a general introduction to the phenomena of mechanical failure in materials: a basic understanding of solid mechanics and materials engineering is assumed, though appropriate introductory references are provided where necessary. After a simple explanation of how to use critical distance methods, and a more detailed exposition of the methods including their history and classification, the book continues by showing examples of how critical distance approaches can be applied to predict fracture and fatigue in different classes of materials. Subsequent chapters include some more complex theoretical areas, such as multiaxial loading and contact problems, and a range of practical examples using case studies of real engineering components taken from the author's own consultancy work.
The Theory of Critical Distances will be of interest to a range of readers, from academic researchers concerned with the theoretical basis of the subject, to industrial engineers who wish to incorporate the method into modern computer-aided design and analysis.
- Comprehensive collection of published data, plus new data from the author's own laboratories
- A simple 'how-to-do-it' exposition of the method, plus examples and case studies
- Detailed theoretical treatment
- Covers all classes of materials: metals, polymers, ceramics and composites
- Includes fracture, fatigue, fretting, size effects and multiaxial loading
Frequently asked questions
Information
Introduction
Materials Under Stress
Publisher Summary
1.1 StressāStrain Curves
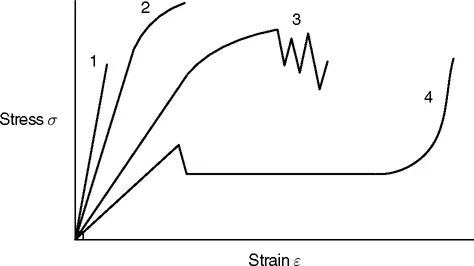
1.2 Failure Mechanisms
1.2.1 Failure at the atomic level
1.2.2 Failure modes in engineering components
Table of contents
- Cover image
- Title page
- Table of Contents
- Preface
- Nomenclature
- Chapter 1: Introduction: Materials Under Stress
- Chapter 2: The Theory of Critical Distances: Basics: An Introduction to the Basic Methodology of the TCD
- Chapter 3: The Theory of Critical Distances in Detail: The History, Background and Precise Definition of the TCD
- Chapter 4: Other Theories of Fracture: A Review of Approaches to Fracture Prediction
- Chapter 5: Ceramics: Brittle Fracture in Engineering Ceramics, Building Materials, Geological Materials and Nanomaterials
- Chapter 6: Polymers: Brittle Fracture in Polymeric Materials
- Chapter 7: Metals: Brittle Fracture in Metallic Materials
- Chapter 8: Composites: Brittle Fracture in Fibre Composite Materials
- Chapter 9: Fatigue: Predicting Fatigue Limit and Fatigue Life
- Chapter 10: Contact Problems: Failure Processes at Points of Contact Between Bodies
- Chapter 11: Multiaxial Loading: Fracture and Fatigue Under Complex Stress States
- Chapter 12: Case Studies and Practical Aspects
- Chapter 13: Theoretical Aspects
- Author Index
- Subject Index