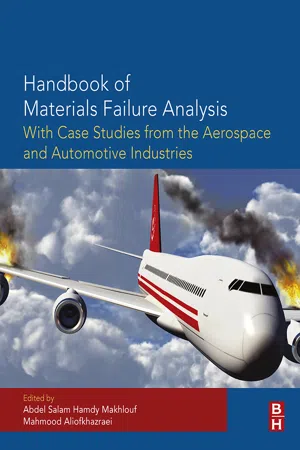
Handbook of Materials Failure Analysis with Case Studies from the Aerospace and Automotive Industries
- 524 pages
- English
- ePUB (mobile friendly)
- Available on iOS & Android
Handbook of Materials Failure Analysis with Case Studies from the Aerospace and Automotive Industries
About This Book
Handbook of Materials Failure Analysis: With Case Studies from the Aerospace and Automotive Industries provides a thorough understanding of the reasons materials fail in certain situations, covering important scenarios, including material defects, mechanical failure as a result of improper design, corrosion, surface fracture, and other environmental causes.
The book begins with a general overview of materials failure analysis and its importance, and then logically proceeds from a discussion of the failure analysis process, types of failure analysis, and specific tools and techniques, to chapters on analysis of materials failure from various causes. Later chapters feature a selection of newer examples of failure analysis cases in such strategic industrial sectors as aerospace, oil & gas, and chemicals.
- Covers the most common types of materials failure, analysis, and possible solutions
- Provides the most up-to-date and balanced coverage of failure analysis, combining foundational knowledge, current research on the latest developments, and innovations in the field
- Ideal accompaniment for those interested in materials forensic investigation, failure of materials, static failure analysis, dynamic failure analysis, fatigue life prediction, rotorcraft, failure prediction, fatigue crack propagation, bevel pinion failure, gasketless flange, thermal barrier coatings
- Presents compelling new case studies from key industries to demonstrate concepts
- Highlights the role of site conditions, operating conditions at the time of failure, history of equipment and its operation, corrosion product sampling, metallurgical and electrochemical factors, and morphology of failure
Frequently asked questions
Information
Strategies for static failure analysis on aerospace structures
Abstract
1 Introduction
2 Delamination Growth in Composites
Table of contents
- Cover image
- Title page
- Table of Contents
- Copyright
- Contributors
- Preface
- Part 1: Failure Analysis in Aircraft and Aerospace Structures
- Part 2: Failure Analysis in Automotive and Transportation Structures
- Index