
- 211 pages
- English
- ePUB (mobile friendly)
- Available on iOS & Android
Mechanics of Sheet Metal Forming
About This Book
The basic theory of sheet metal forming in the automotive, appliance and aircraft industries is given. This fills a gap between the descriptive treatments in most manufacturing texts and the advanced numerical methods used in computer-aided-design systems.
The book may be used by lecturers in undergraduate courses in manufacturing; plentiful exercises and worked examples provide quantitative tutorial problems for students. A separate, but related simulation software package advertised on this page enables students to explore the limits of processes and understand the influence of different process and material variables.
Engineers in stamping plants and press shops find the book useful in understanding what happens during forming and why failures occur. The book is also used as a text for industrial short courses that have been given in many countries. Die designers and tooling engineers find the simple treatment of processes useful at the conceptual design stage and also in determining modifications needed to overcome problems indicated by detailed numerical analysis.
The original text, published 10 years ago, has been completely rewritten for this edition and newer topics such as hydroforming included. Simple equations governing plastic deformation, press forming, bending, punch stretching and deep drawing are derived and explained. The aim is to provide simple applicable methods rather than complex numerical techniques for practising engineers and for students interested in a quantitative and practical approach.
SIMPLIFIED STAMPING SIMULATION SOFTWARE "4S'
The analytical treatment in this book is used to develop simulation modules for simple cases of sheet forming such as stamping, deep drawing, bending and hydroforming. Students can investigate the influence of tooling dimensions, material properties and process variables such as friction on the outcome of operations and see from animated models how, for example, press loads develop during forming. Applications using this package greatly enhance interest in the development of theory in the book.
The website http://www.mssinternational.com provides further information and an opportunity to run some of the modules.
- Presents the fundamentals of sheet metal forming - bending, stretching, press forming, deep drawing and hydroforming
- Shows how deformation, loads and process limits can be calculated using simple equations
- Concentrates on simple, applicable methods rather than complex numerical techniques
- Contains many exercises, worked examples and solutions
- Used as a reference text in undergraduate manufacturing courses, as a required text in specialist graduate courses and as a course text for industrial short courses
- Is supported by a separate, but related simulation software package described below
Frequently asked questions
Information
1.1 Tensile test

1.1.1 The load–extension diagram
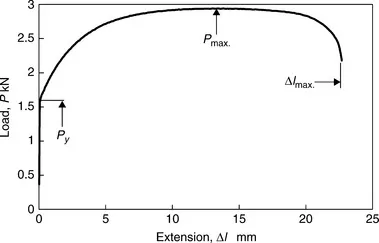
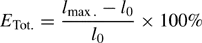
1.1.2 The engineering stress–strain curve
Table of contents
- Cover image
- Title page
- Table of Contents
- Copyright
- Preface to the second edition
- Preface to the first edition
- Disclaimer
- Introduction
- Chapter 1: Material properties
- Chapter 2: Sheet deformation processes
- Chapter 3: Deformation of sheet in plane stress
- Chapter 4: Simplified stamping analysis
- Chapter 5: Load instability and tearing
- Chapter 6: Bending of sheet
- Chapter 7: Simplified analysis of circular shells
- Chapter 8: Cylindrical deep drawing
- Chapter 9: Stretching circular shells
- Chapter 10: Combined bending and tension of sheet
- Chapter 11: Hydroforming
- Appendix A1: Yielding in three-dimensional stress state
- Appendix A2: Large strains: an alternative definition
- Solutions to exercises
- Index