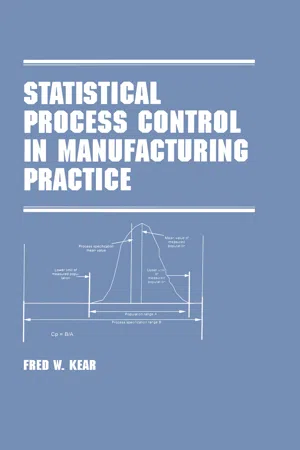
eBook - ePub
Statistical Process Control in Manufacturing Practice
Fred W. Kear
This is a test
- 240 pages
- English
- ePUB (mobile friendly)
- Available on iOS & Android
eBook - ePub
Statistical Process Control in Manufacturing Practice
Fred W. Kear
Book details
Book preview
Table of contents
Citations
About This Book
Emphasizing the importance of understanding and reducing process variation to achieve quality manufacturing performance, this work establishes how statistical process control (SPC) provides powerful tools for measuring and regulating manufacturing processes. It presents information derived from time-tested applications of SPC techniques at on-site process situations in manufacturing. It is designed to assist manufacturing organizations in explaining and implementing successful SPC programmes.
Frequently asked questions
How do I cancel my subscription?
Can/how do I download books?
At the moment all of our mobile-responsive ePub books are available to download via the app. Most of our PDFs are also available to download and we're working on making the final remaining ones downloadable now. Learn more here.
What is the difference between the pricing plans?
Both plans give you full access to the library and all of Perlegoâs features. The only differences are the price and subscription period: With the annual plan youâll save around 30% compared to 12 months on the monthly plan.
What is Perlego?
We are an online textbook subscription service, where you can get access to an entire online library for less than the price of a single book per month. With over 1 million books across 1000+ topics, weâve got you covered! Learn more here.
Do you support text-to-speech?
Look out for the read-aloud symbol on your next book to see if you can listen to it. The read-aloud tool reads text aloud for you, highlighting the text as it is being read. You can pause it, speed it up and slow it down. Learn more here.
Is Statistical Process Control in Manufacturing Practice an online PDF/ePUB?
Yes, you can access Statistical Process Control in Manufacturing Practice by Fred W. Kear in PDF and/or ePUB format, as well as other popular books in Sciences physiques & Chimie industrielle et technique. We have over one million books available in our catalogue for you to explore.
Information
1
The History and Application of Statistical Process Control
This chapter provides an overview of how statistical process control was developed by American and international companies as a prevention tool to improve quality, cut costs, and establish customer satisfaction in an era of unprecedented competition. The discussion of the development of SPC provides a general understanding of how it is used to prevent unnecessary costs by measuring process performance as well as monitoring the process performance.
AN OVERVIEW OF STATISTICAL PROCESS CONTROL
Statistical process control (SPC), while being one of the most powerful tools for manufacturing management, is also often misunderstood by those for whom it offers the greatest benefit. Perhaps, some of this misunderstanding has come from the use of the word âcontrol.â Process control, as it is commonly understood, implies the use of corrective action for a situation in which a potentially catastrophic change is occurring. We often think of controls as being knobs or fixtures on a panel that are used to monitor a process and that are provided to make any necessary corrections. Statistical process control has far wider implications than the job of making corrections to an errant process.
Historically, the wide use of SPC and the appreciation for what it can do for manufacturing management generally developed in the post-World War II era, when world industries were struggling to recover from the results of that war, convert to peacetime activities, and compete on a global scale. The American policy of assisting both friends and former enemies to recover their economies set the stage for generating a global manufacturing community with each sector seeking to provide goods having the quality and cost that would capture large market shares in this economy.
Astute manufacturing managers knew that if they were going to prosper, the key to success lay in understanding and managing their processes well. Traditionally, quality assurance organizations had tried to control quality by inspecting the parts coming off manufacturing lines, auditing manufacturing processes, and demanding corrective action when the process yields slipped below certain prescribed levels. This helped, but it fell far short of giving management the results that it needed to stay alive in this competitive era
Although this competitive urgency was global, the primary drive for improvement was in America and Japan. A number of plans and ideas emerged for improving manufacturing processes and, primarily through the work of W. Edwards Deming (and others), both countries began development of SPC as we know it. As it finally emerged, SPC focused on four key points relating to manufacturing processes. These are:
- Understanding of the process fully and completely
- Making sure that the process is fully capable of fulfilling its mission
- Making sure that the process is operating optimally at all times
- Continuously improving the process
Manufacturing, along with the service industries, is one of the key activities in human commerce that generates jobs and income for most of the workers in our society. Throughout recorded history, men and women have made things from material, either for their own use or for sale to others. Manufacturing has changed at an astounding pace in the Industrial Era, with the greatest changes occurring during the last 75 years. Mass production, introduced by Henry Ford, and the automation of manufacturing processes have driven the practices used in manufacturing to bring the changes that we see in the typical factory operating today. With these changes, uniform products could be manufactured and distributed to consumers at prices that allowed the typical family or business to afford commodities that had been available only to the affluent under the old system. Most of us understand, basically, what manufacturing involves. It is an activity wherein materials are altered either in form or by the addition of other materials to yield a product for a specific use. This general definition is important to those working in the field of manufacturing.
The complexity of industrial manufacturing challenges our understanding of its fine points and how its processes function (or are supposed to function) in order to produce satisfactory results. Since almost all communities in the modern world have some form of manufacturing sector, it would seem that, by now, we would have a detailed understanding of what it takes to do the job. Also, with most every sector of society struggling to compete in manufacturing, it follows that we should understand that we have to do the job well if we are to gain and retain the customers that we need in order to survive as manufacturers.
We have applied this knowledge this relatively well, but the challenge still faces us. In fact, the challenge will never go away. Since manufacturing uses the labor of people combined with materials to make products, we can expect that the people will change with time (new employees) and that the materials will vary from batch to batch. The methods that we use to alter the materials for our products are called âmanufacturing processesâ (in this book, we will refer to smaller segments of a process as âoperations"). The tools and equipment that we use in these manufacturing processes also change from time to time as the processes are improved or altered to accommodate new requirements and when better technology provides us with better tools with which to do the job.
Each change in the personnel involved in the manufacturing process, each change in material, each change in tools and equipment, has a potential effect on the product. As consumers, we recognize that there are variations (changes) from product to product in goods produced by manufacturing. We are either willing to accept certain variations or compelled to use the products because of circumstances. However, when variations do exist and these variations are beyond what we can accept, we look for new sources that can meet our expectations. No one in manufacturing wants to loose customers, so it is important to understand variations in manufacturing processes and how to control them.
In order to know what variations there are in manufactured products, we must have some method of measuring the attributes of the product and of determining how these attributes change from product to product (measuring methods are discussed in the next chapter). Measuring product quality (a function of variation) is most important when the product is in the hands of the customer but, by then, it is too late for the manufacturer to avoid the displeasure that a poor product produces. Therefore, as manufacturers, we must find a way to characterize and define unnecessary variations while we still have control of the product. The following list describes some of the product attributes (or characteristics) that are useful for measuring manufacturing processes:
- Appearance
- Color, finish, design, feel
- Function
- Electrical/mechanical performance
- Size
- Dimension, weight
- Cost
- Competitiveness and affordability
- Availability
- On-time delivery
The connection between the above attributes and the manufacturing processes that go into making the product is inescapable. It is this connection that SPC seeks to manage in a way that makes the manufacturer competitive among world-class peers.
Characterization of a product implies that we want to compare it against a standard. It also implies that we want to have this information not only about one piece that we have produced, but also about all of the pieces that come out of our process. We usually refer to the total output of our process as the âproduct population.â Population is a term more commonly used to refer to the inhabitants of a country or a community, but in manufacturing, it refers to all the products of a given type that are produced from a single process.
Just as we often do when attempting to characterize a specific group of people, we can select a given attribute of a product and, by using appropriate means of measurement, determine how the pieces vary as they emerge from a process. These measurements may be made for any aspect of the product, such as weight, dimensions, density, electrical performance, color, etc. However, we need to do more than just measure these attributes. We need to know two basic things as we perform a measurement. First, we need to know what the measurement result should be (standard), and how much variation is allowed by the standard. Second, we need to know what portion of the process affects the attribute that we are measuring. When we are measuring a product attribute, we are actually measuring the effectiveness of the process. We need to keep this in mind.
HOW VARIATIONS IN PROCESSES AFFECT QUALITY
In any evaluation of product attributes, we will find variations because no two products are exactly alike. Our objective is to determine how much the products are varying and how important this variation is to the productâs function (and customer satisfaction). Customersâ expectations regarding variation have increased in recent years as worldwide competition has forced higher standards on manufacturing. Manufacturers have developed a strong sensitivity for eliminating unnecessary variation from their processes (therefore, from their products).
If there are variations in all products we are manufacturing, regardless of how carefully they are manufactured, we must determine what portion of the variation is unavoidable and how much of the variation present is avoidable. Avoiding or eliminating the variation may add cost to the product or it may cut the cost of the product. This is why we must understand what portion of the process is responsible for the attribute that we are measuring. Throughout this book, the causes for variation in processes are addressed according to the following definitions:
CAUSES FOR VARIATION IN MANUFACTURING PROCESSES
Common Causes: These are unavoidable process variations that are always present and for which no specific cause can be assigned
Special Causes: These are avoidable process variations that either occur sporadically or are present at the time that the measurement is made
It is important to understand what we are talking about when we discuss variations in manufacturing processes. Our perception of variation depends on the context within which we are used to operating.
In nonmanufacturing environments, commonly acceptable variations can consist of relatively large amounts such as ±Œ inch or several ounces (such as might be encountered in food service or carpentry). This is not true in manufacturing, where it may not be acceptable to have variations as much as .001â-.002â in a dimension or a fraction of a gram in weight. Yet, variations do occur in manufacturing from one piece to the next, regardless of how closely the process is controlled. Often, these variations are very small (as compared with established tolerances for the process) and can be ignored. At other times, these variations may become significantly large and cause concern for product quality. We watch the processes closely in order to detect when this has occurred so that we can make corrections before the variations become unacceptable. When the process is under control, we note these incidental variations but do not implement changes when such changes would not improve the process.
PROCESS CHARACTERIZATION
We have mentioned that we measure a particular attribute (an attribute, in this context, means a feature such as a dimension or a giv...
Table of contents
- Cover
- Half Title
- Series Page
- Title Page
- Copyright Page
- Dedication Page
- Preface
- Contents
- 1. The History and Application of Statistical Process Control
- 2. Measuring Manufacturing Processes
- 3. Characterization of Manufacturing Processes
- 4. Key Aspects of the Manufacturing Process
- 5. Planning the Statistical Process Control Management System
- 6. Problem Solving and Corrective Action
- 7. Continuous Process Improvement
- 8. Customer Satisfaction and Statistical Process Control
- Appendices
- Glossary
- Bibliography
- Index
Citation styles for Statistical Process Control in Manufacturing Practice
APA 6 Citation
Kear, F. (2020). Statistical Process Control in Manufacturing Practice (1st ed.). CRC Press. Retrieved from https://www.perlego.com/book/2023733/statistical-process-control-in-manufacturing-practice-pdf (Original work published 2020)
Chicago Citation
Kear, Fred. (2020) 2020. Statistical Process Control in Manufacturing Practice. 1st ed. CRC Press. https://www.perlego.com/book/2023733/statistical-process-control-in-manufacturing-practice-pdf.
Harvard Citation
Kear, F. (2020) Statistical Process Control in Manufacturing Practice. 1st edn. CRC Press. Available at: https://www.perlego.com/book/2023733/statistical-process-control-in-manufacturing-practice-pdf (Accessed: 15 October 2022).
MLA 7 Citation
Kear, Fred. Statistical Process Control in Manufacturing Practice. 1st ed. CRC Press, 2020. Web. 15 Oct. 2022.