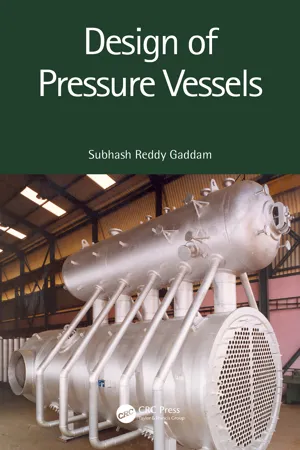
This is a test
- 234 pages
- English
- ePUB (mobile friendly)
- Available on iOS & Android
eBook - ePub
Design of Pressure Vessels
Book details
Book preview
Table of contents
Citations
About This Book
Pressure vessels are prone to explosion while in operation, due to possible errors in material selection, design and other engineering activities. Addressing issues at hand for a working professional, this book covers material selection, testing and design of pressure vessels which enables users to effectively use code rules and available design softwares. Relevant equation derivations have been simplified with comparison to ASME codes. Analysis of special components flange, bellow and tube sheet are included with their background. Topics on tube bend, supports, thermal stresses, piping flexibility and non-pressure parts are described from structural perspective. Vibration of pressure equipment components are covered as well.
Frequently asked questions
At the moment all of our mobile-responsive ePub books are available to download via the app. Most of our PDFs are also available to download and we're working on making the final remaining ones downloadable now. Learn more here.
Both plans give you full access to the library and all of Perlegoâs features. The only differences are the price and subscription period: With the annual plan youâll save around 30% compared to 12 months on the monthly plan.
We are an online textbook subscription service, where you can get access to an entire online library for less than the price of a single book per month. With over 1 million books across 1000+ topics, weâve got you covered! Learn more here.
Look out for the read-aloud symbol on your next book to see if you can listen to it. The read-aloud tool reads text aloud for you, highlighting the text as it is being read. You can pause it, speed it up and slow it down. Learn more here.
Yes, you can access Design of Pressure Vessels by Subhash Reddy Gaddam in PDF and/or ePUB format, as well as other popular books in Physical Sciences & Industrial & Technical Chemistry. We have over one million books available in our catalogue for you to explore.
Information
1 Introduction
Mechanical design (analysis) reported in this book is the calculation of thickness for maximum allowable stress or maximum induced relevant stresses for a given thickness of any element for which equation is derived using maximum principal stress theory of failure by any analytical method of analysis and relevant design theories. The activities involved in connection with pressure vessel design for manufacturing them are briefly covered in this chapter.
Design in general starts with process design, which is normally performed in R & D organization. The next step is plant design for satisfactory operation and facilitating maintenance of the plant, which is the design and linking of other auxiliary parts:
- Equipments in which process or part of it takes place.
- Controlling parts such as instruments, valves, etc., which are used to isolate or regulate the process parameters such as flow, pressure, and temperature or any other required controls to perform.
- Instruments, gauges, control valves, etc., which are involved in measuring the process parameters in field as well as in a control room/a digital control system.
- Auxiliary rotating equipments such as pumps, fans, and other such equipments.
Linking between equipments is performed by process piping with required instruments, field gauges, process valves, etc. as per piping and instrumentation diagrams required for the process.
Instruments and valves are normally manufactured by specialized organizations. Other auxiliary equipments are also manufactured by specialist organizations mostly involving casting, forging, and fabrication. Equipment and piping are manufactured by fabricating mostly welding using raw materials such as plates, tubes, pipes, pipe fittings, etc.
Equipment, piping, and most of the line/process instruments are under pressure and hence are called pressure vessels.
Pressure vessels are first designed (detailed process design and operating parameters involving heat transfer and fluid dynamics) to give arrangement, shape, and size required for a specified process. Then, design data are obtained, residual process design is carried out, materials are selected, remaining geometry and arrangement are finalized, and thickness is calculated to withstand prevailing loads.
The pressure vessel consists mostly of plates and tubular shaped parts formed as required and welded. Most of the components of pressure vessels excluding nonpressure parts such as attachment supports and internals are subjected to pressure and hence called pressure parts. Selection of materials, calculation of thickness, and other requirements shall be in accordance with relevant national technical codes and statutory rules/acts. Materials for nonpressure parts welded to pressure parts shall be the same as those for pressure parts. All the nonpressure parts are to be designed as per relevant standards, fundamentals, and accepted technical literature and practices. It also includes the preparation of detailed specification or data sheets of controls, instruments, and auxiliaries for procurement/manufacturing. Design also includes arrangement and calculation of handling and shipping components.
Design details not given in codes for pressure parts are submitted for the acceptance of the statutory or authorized inspector, and the designer provides details of design from other sources such as other codes, standards, fundamentals, and excepted practices, which will be as safe as those provided by the rules of code. Alternately, strength of pressure parts can be established by a proof test or finite element analysis.
The next step is engineering and producing drawings for arrangement and details of parts of equipments required for manufacturing, erection, and shipping. The material list, detailed data sheets for the purchase of raw materials, and other components are prepared.
Pressure vessels including boilers are normally allowed to use in most of the countries duly registered, and certified for use similar to automobile vehicles. The statutory and/or mandatory rules vary from country to country and are not the same for boilers and pressure vessels and more stringent for boilers. In general, complete activity of manufacturing boilers and pressure vessels (generally termed pressure parts) right from raw materials until completion of installation at the place of their use is inspected as per the Acts and Rules of the country by agency authorized in the Acts and Rules for the purpose before being registered and certified for use.
The manufacturing drawings are to be approved by the inspection agency duly conforming to the rules (code), the components are inspected, required tests are carried out in various stages, identification marks are stamped, and finally the pressure vessels are hydraulically tested for preliminary check of their resistance to pressure before transporting to the place of erection. The code stipulates that the manufacturer should prepare all required documents duly signed by them and the inspection agency which will accompany the pressure component for verification before erection and for registration.
2 Material
2.1 Metallurgical Fundamentals
- Toughness: Strength and ductility = area under stress-strain curve, toughness of structural steel > spring steel.
- Microstructure: Ferrite, austenite, cementite, pearlite, and martensite.
- Ferrite: It has a body centered cubic crystal structure. It is pure or 0.01% c (dissolve at room temperature), soft, and ductile.
- Austenite: It has a face centered cubic crystal structure and exists over 912°C.
- Cementite: Compounds of iron and carbon iron carbide (Fe3C) are hard and brittle.
- Pearlite: The lamented structure is formed of alternate layers of ferrite and cementite. It combines the hardness and strength of cementite with the ductility of ferrite. The laminar structure acts as a barrier to crack movement as in composite, which gives its toughness.
- Martensite: It has a very hard needle-like structure of iron and carbon and is formed by rapid cooling of the austenitic structure (above the upper critical temperature), which needs to be modified by tempering before acceptable properties are reached.
2.2 Variety of Materials
The following materials are normally used in manufacture of boilers and pressure vessels.
2.2.1 Carbon Steel (CS)
CS generally contains carbon 0.3% max. CS is easily formable, weldable, and machinable. However, CS has limited corrosion resistance and low creep strength and is normally not advised for use in the creep range that is for higher temperatures more than 400°C.
2.2.2 Low Alloy Steel (LAS)
LAS contains one or more alloying elements to improve mechanical and other properties such as corrosion resistance, strength at elevated temperatures, impact and toughness at low temperatures, and resistance to pitting. The most usual used alloying elements are chromium 9% max, molybdenum 1% max, traces of vanadium, nickel, etc. Nickel up to 9% is used for special requirements. Objects of main alloying elements are given below:
- Chromium (Cr) improves resistance to oxidation and improves corrosion resistance, abrasion resistance, high-temperature strength, and resistance to high-pressure hydrogen.
- Molybdenum (Mo) improves strength at elevated temperature, creep resistance, and resistance to pitting.
- Vanadium (V) improves wear resistance, high-temperature strength, and resistance to high-pressure hydrogen.
- Nickel (Ni) improves toughness, low temperature properties, and corrosion resistance.
2.2.3 Stainless Steel (SS)
There are three varieties of SS: austenitic, martensitic, and ferritic.
- Austenitic is corrosion resistant, tough, ductile, and easy to form and weld. These steels are suitable for low service temperature in the range of â 80 to 250°C as well as high service temperature in the range of 400 to 500°C. Some special grades such as 304H, 316H, and 321H are suitable for very high service temperatures in the range of 500 to 816°C.
- Martensitic contains 1 to 14% chromium. Type 409, 410, and 410S are commonly used for noncooled and nonpressure parts (PPs) required for high-temperature service.
- Ferritic contains 14 to 20% chromium. Type 429, 430, and 439 belong to this category. These grades are corrosion-resistant and suitable for higher service temperatures up to 650°C and up to 800°C for noncooled and non-PPs.
2.2.4 Nonferrous Alloys
Inconel and incoloy are used for very high temperature services above 800°C, for noncooled and non-PPs such as coil supports, tube supports in high temperature radiation zones, and furnace components.
- Inconel: Different grades of inconel contain nickel in the range of 50 to 75% and chromium in the range of 15 to 25% and are suitable for high temperature above 800°C. SB-168 Alloy Nos. 6600, 6601, 6617, and 6690 belong to this group.
- Incoloy: Different grades of incoloy contain nickel in the range of 30 to 40% and chromium around 20% and are suitable for high temperature above 800°C. SB-409 Alloy No.8120, 8800, 8810, and 8811 belong to this group.
2.2.5 Nonmetallic Materials
- Insulation
- Refractory
2.3 Material Selection
Generally, codes for pressure vessels do not contain material selection. Codes stipulate only the manufacturing process, chemical composition, mechanical properties (mandatory and optional), inspection, heat treatment and testing requirements, certification, marking etc., for the general or listed materials. Most of the nations have their own material standards to suit various processes and functional requirements. Material selection out of the available specifica...
Table of contents
- Cover
- Half Title
- Title Page
- Copyright
- Contents
- Preface
- Author
- Chapter 1 Introduction
- Chapter 2 Material
- Chapter 3 Mechanical Design Basics
- Chapter 4 Pressure Vessel Design Basics
- Chapter 5 Internal Pressure
- Chapter 6 External Pressure
- Chapter 7 Discontinuity Stresses
- Chapter 8 Local Stresses
- Chapter 9 Thermal Stresses and Piping Flexibility
- Chapter 10 Flat-Plate Components
- Chapter 11 Supports
- Chapter 12 Wind and Seismic
- Chapter 13 Flanges
- Chapter 14 Vibration
- Chapter 15 Expansion Joints
- Index