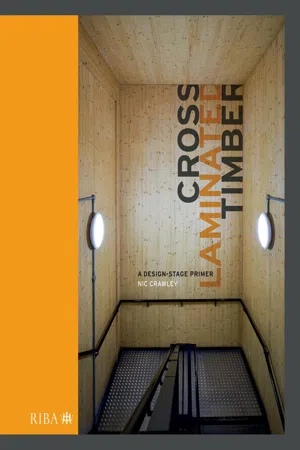
This is a test
- 192 pages
- English
- ePUB (mobile friendly)
- Available on iOS & Android
eBook - ePub
Book details
Book preview
Table of contents
Citations
About This Book
Cross-laminated timber (CLT) has long been heralded as a wonder material, with a light environmental footprint, high strength, quick installation times and reduced waste â so why isn't everyone using it? Delving into the key considerations including fire safety, cost and value, visual aspects, planning, feasibility and engineering, this book is an essential companion to designing and delivering exemplar CLT buildings. Abundantly illustrated with over 130 colour images and in-depth case studies from around the world, it will help the entire project team - whether design team, constructor or clients - to better understand and build using a truly modern method of construction.
- Outlines key challenges as well as benefits of CLT, including quality, cost and environmental benefits, risk reduction and health and safety benefits
- Presents lessons learnt to aid the development process, from the earliest stages of design to production and assembly
- Accessible, easy-to-read handbook format allows you to dip in and out, investigating issues as necessary
- Multidisciplinary in approach with contributions from a range of practitioners
Frequently asked questions
At the moment all of our mobile-responsive ePub books are available to download via the app. Most of our PDFs are also available to download and we're working on making the final remaining ones downloadable now. Learn more here.
Both plans give you full access to the library and all of Perlegoâs features. The only differences are the price and subscription period: With the annual plan youâll save around 30% compared to 12 months on the monthly plan.
We are an online textbook subscription service, where you can get access to an entire online library for less than the price of a single book per month. With over 1 million books across 1000+ topics, weâve got you covered! Learn more here.
Look out for the read-aloud symbol on your next book to see if you can listen to it. The read-aloud tool reads text aloud for you, highlighting the text as it is being read. You can pause it, speed it up and slow it down. Learn more here.
Yes, you can access Cross Laminated Timber by Nic Crawley in PDF and/or ePUB format, as well as other popular books in Architecture & Architecture General. We have over one million books available in our catalogue for you to explore.
Information
CHAPTER 1
MANUFACTURING AND PROCESSING

FIG 1.0 (chapter opener) Automated finger jointing machine processing lamella boards.
CLT was developed to add value to a plentiful supply of relatively low grade, fast-growing commercially farmed whitewood in Central Europe, predominantly Norway Spruce (Picea abies) as Figure 1.1. Other coniferous softwoods are utilised as available. North American species include the more durable Douglas Fir/Oregon Pine (Pseudotsuga menziesii) and in Australia, Radiata (or Monterey) Pine (Pinus radiata).
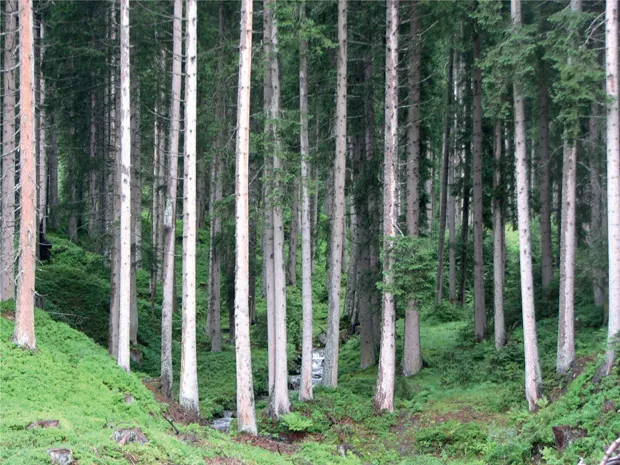
FIG 1.1 An Austrian spruce forest. Large, medium-to-fast-growing trees reach 35â60m in height over 20â50 years.
CLT factories are typically located close to sawmills. Turning trees into dimensioned and usable boards results in some fibre loss c. 40%, as sawdust and chippings, most of which is used locally for other processes. Timber used is typically PEFC or FSC certified so specifiers may be assured that sources and the supply chain are well managed (Figure 1.2).
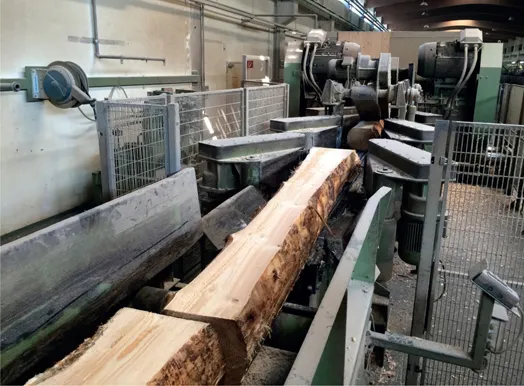
FIG 1.2 Harvesting is heavily mechanised with trunks stripped and cut to length before being transported to a mill as âroundwoodâ.
Boards are sawn, graded and selected depending upon their position within the log section, for resultant strength, stability and surface quality. Figure 1.3 illustrates sawn boards being presented for grading.
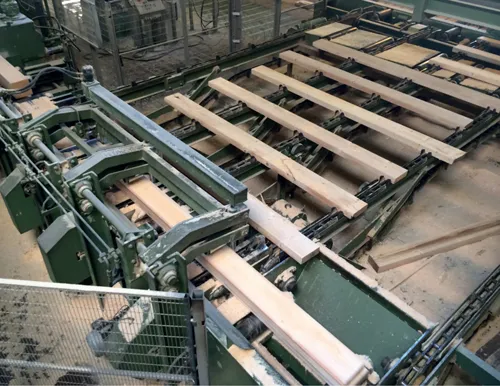
FIG 1.3 Dimensioned boards sorted by grade.
Timber is hygroscopic so the reduction and control of bound moisture to around 12% moisture content (MC)1 is critical to ensure dimensional stability and tight tolerances (see Figure 1.4). Fungal growth and degradation is a risk in use above 20% MC but not below.2 Dry timber is also stronger, lighter, easier to handle, transport and work, a better substrate for adhesives and at lower risk from pest or insect degradation.
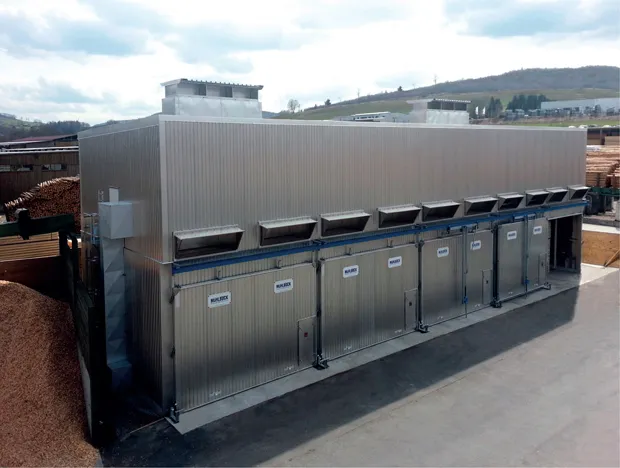
FIG 1.4 A commercial convective kiln for artificially drying timber boards.
PANEL MANUFACTURING
Controlled factory environments
Off-site manufacturing can often be a little underwhelming, with workers in wellington boots using old fashioned processes in draughty sheds. CLT production is more akin to modern vehicle assembly with the flow of materials along a high-speed production line finely tuned with tightly integrated processes (Figure 1.5). Factories are typically described in terms of annual output (m3 per annum) and manufacturers typically offer tours with videos online showing various processes in further detail.

FIG 1.5 XLamâs 70,000m3 pa capacity Australian production facility in Wodonga, Victoria was commissioned in 2018 and is typical of recent medium/large-sized plants.
Finger jointing, cutting and planing
Defects such as splits or larger knots are cut from sorted boards. The resultant cut ends are finger jointed: spliced, adhered and cured. Such sawtoothed joints may be visible on a finished panel. Boards are then finely planed to ensure dimensional tolerances are acceptable and to optimise surface bonding potential.
Layup: outer layer
This first layer (lamella) will form the outer surface of any panel. Board orientation may be longitudinal (for longer spanning floor slabs or vertical shafts, as Figure 1.6) or latitudinal (for shorter or cross-direction storey height wall panels). Cut boards are positioned on a movable flatbed by automated chain belts or vacuum lifts.
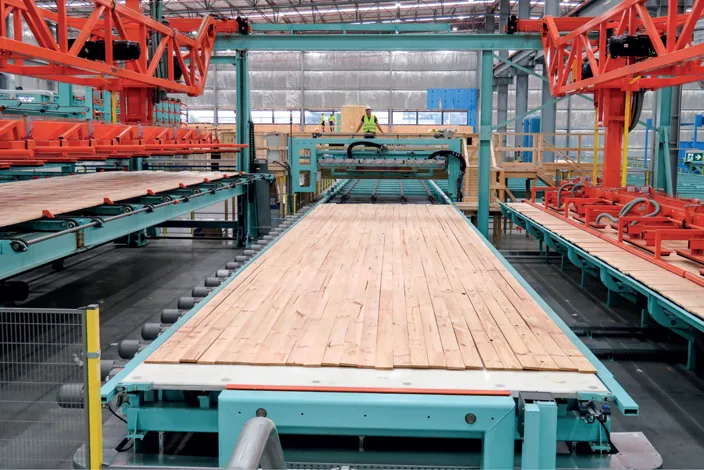
FIG 1.6 Billet layup (the billet is the CLT âblankâ, pressed and cured before processing).
Layup: adhesive application
Adhesive is applied over the entire surface at approx. 0.1mm thick (typically comprising around 0.6% of panel weight) as Figure 1.7. The most common adhesive is an environmentally friendly single component polyurethane (PUR) adhesive that is free of solvents, VOCs and formaldehyde (no off-gassing) that cures quickly in air when activated by the moisture in dried timber (termed cold setting).3 Alternatives such as melamine urea formaldehyde (MUF) offer differing fire performance and may be set using microwaves when pressing.
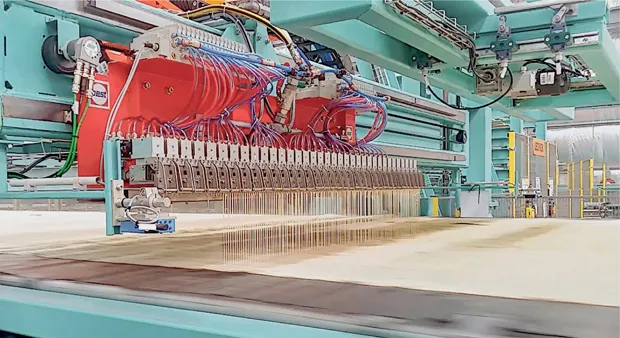
FIG 1.7 CNC controlled adhesive application to lamella surface. Some manufacturers may side bond boards for additional stability.
Layup: subsequent layers
Subsequent layers are positioned promptly using vacuum lifting devices, as Figure 1.8. Board direction alternates 90 degrees so the timber grain dir...
Table of contents
- Cover
- Title Page
- Copyright Page
- Contents
- About the author
- Acknowledgements
- Introduction
- 1 Manufacturing and processing
- 2 Applications and use
- 3 Context
- 4 Feasibility and initial considerations
- 5 Visual aspects
- 6 Cost and value
- 7 Planning and social issues
- 8 Design and procurement
- 9 Engineering aspects
- 10 Refurbished structures
- 11 Safety
- 12 Buildability and assembly
- 13 The international outlook
- 14 Flexibility, use and life cycle issues
- 15 Client issues
- Case Studies
- Conclusion: The way ahead
- Appendices
- Notes
- Index
- Image credits