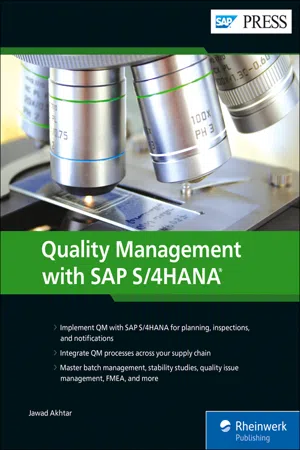
This is a test
- 950 pages
- English
- ePUB (mobile friendly)
- Available on iOS & Android
eBook - ePub
Quality Management with SAP S/4HANA
Book details
Book preview
Table of contents
Citations
Frequently asked questions
At the moment all of our mobile-responsive ePub books are available to download via the app. Most of our PDFs are also available to download and we're working on making the final remaining ones downloadable now. Learn more here.
Both plans give you full access to the library and all of Perlegoâs features. The only differences are the price and subscription period: With the annual plan youâll save around 30% compared to 12 months on the monthly plan.
We are an online textbook subscription service, where you can get access to an entire online library for less than the price of a single book per month. With over 1 million books across 1000+ topics, weâve got you covered! Learn more here.
Look out for the read-aloud symbol on your next book to see if you can listen to it. The read-aloud tool reads text aloud for you, highlighting the text as it is being read. You can pause it, speed it up and slow it down. Learn more here.
Yes, you can access Quality Management with SAP S/4HANA by Jawad Akhtar in PDF and/or ePUB format, as well as other popular books in Computer Science & Computer Science General. We have over one million books available in our catalogue for you to explore.
Information
Part I
Quality Management Core Concepts
1 Quality Management in SAP S/4HANA
The quality management area in SAP S/4HANA enables a company to improve the quality of its products by continuously assessing them at any given step of the logistics and supply chain. By doing so, the company can ensure that its products conform to relevant product regulations, industry standards, and/or company quality standards.
Companies that want to maintain, retain, and continuously improve the quality of their products find quality management (QM) in SAP S/4HANA to be their trusted and steadfast companion in the logistics and supply chain management functions. From prequalifying potential vendors for supplying raw and packing materials, conducting preliminary inspections before goods reach the company premises, and conducting quality tests when vendors deliver the materials to ensuring quality inspection during and after production finds, QM integrates into all-important business processes. QM also ensures that companies can conduct another, customer-specific round of quality checks and, before dispatching goods to customers, extensively evaluate defects in their own returned products, with the aim of eliminating those defects.
QM covers it all: new products developed with a stability study, continuous product and process improvements with failure mode and effects analysis (FMEA), and internal and external audits using audit management. Quality control ensures that companies frequently evaluate vendors to maintain business relationships with them, as well as monitor critical statistical process control for products that are produced in house. The optimization in QM allows added functionality like digital signatures that eliminate manual approval processes, manage incoming and outgoing quality certificates, and integrate the Document Management System (DMS) into important business functions.
QM integrates completely with several key logistics and supply chain areas, including procurement, production, and sales. It can check the quality compliance of raw materials when they're first delivered by vendors and later during production and postproduction. The QM area can also check for compliance with customersâ quality specifications before the finished goods are shipped out.
QM is a wide-ranging solution that supports the company throughout the product lifecycle and along the supply chain. In particular, the QM solution offers the following benefits:
- Provides a single quality management solution for all company processes, giving you a single source of truth and access to the most current quality information at any time
- Serves as a complete laboratory information management system (LIMS)
- Helps recognize risks and defects at an early stage and helps to avoid them
- Enables your employees to perform a variety of tasks quickly and efficiently to support their central roles
- Provides a consistent, transparent, closed-loop quality management solution for all company processes in which you can automate the information flow and process steps by using workflow
- Serves as a tightly integrated area in the supply chain that can be used and started during execution of processes such as production and procurement
- Supports assignment to objects from other components, such as customer masters, vendor masters, batches, purchase orders, and production orders
- Ensures compliance with industry standards and legal requirements (e.g., the VDA, FDA, and GMP)
- Reduces operating costs and increases efficiency by improving asset and maintenance management, improving the procurement process, lowering communications expenses, redeploying labor to higher value-added activities, reducing costs of goods sold (COGS), and reducing product returns
- Improves customer service and customer satisfaction by providing better service levels, using complaint management and tracking, improving product and service quality, improving quality and accuracy, and strengthening market competitiveness
- Includes comprehensive quality management functions, such as tools for planning support (e.g., inspection plans), process improvements (e.g., monitoring processes and implementing corrective tasks in notifications), and systematic root-cause analysis
- Provides a central role for employees, with the ability to perform a variety of tasks quickly and efficiently
In this chapter, youâll learn the importance of QM in the SAP S/4HANA landscape, as well as the business processes that companies can manage using QM. First, however, we will give you a good starting point: SAPâs organizational structures, which you need to understand to know how various areas of SAP work together.
1.1 Organizational Structure in SAP
At the start of an SAP implementation project, one of the first and most intensive activities undertaken is the finalization of the organizational structure. This involves having intermodular and intramodular discussions and deliberations to ensure that the SAP system can both cover the legal aspects of the companyâs organizational structure and attend to area-specific reporting needs. In other words, the business process owners, business analysts, and SAP consultants review the existing organizational structure of the company and then simultaneously begin mapping it in the SAP system.
A practical approach to adopt while finalizing the organizational structure in SAP is to ensure that the organizational structure isnât so generic that it loses its significance and prevents the business process owner from extracting the required information from the system, nor is it so minute or detailed that it becomes cumbersome to collate and consolidate the information. You should also keep a forward-thinking view of your organizational structure. If you foresee that ...
Table of contents
- Dear Reader
- Notes on Usage
- Table of Contents
- Â Acknowledgments
- Â Introduction
- Part I Â Quality Management Core Concepts
- 1 Â Quality Management in SAP S/4HANA
- 2 Â Quality Planning
- 3 Â Quality Inspection
- Part II Â Quality Management Integration with Logistics
- 4 Â Integrating with Materials Management
- 5 Â Integrating with Production Planning
- 6 Â Integrating with SAP S/4HANA Sales
- 7 Â Integrating with Plant Maintenance
- 8 Â Integrating with Embedded Extended Warehouse Management
- Part III Â Quality Management Workflow Tools
- 9 Â Batch Management
- 10 Â Sample Management
- 11 Â Quality Certificates
- 12 Â Quality Notification
- 13 Â Engineering Change Management
- 14 Â Audit Management
- 15 Â Stability Study
- 16 Â Failure Mode and Effects Analysis and Control Plan
- Part IV Â Monitoring, Evaluation, and Control in Quality Management
- 17 Â Early Warning System
- 18 Â Reporting in SAP
- 19 Â Quality Control
- A Â Movement Type Mapping
- B Â The Author
- Index
- Service Pages
- Legal Notes