
Sandwich Composites
Fabrication and Characterization
- 388 pages
- English
- ePUB (mobile friendly)
- Available on iOS & Android
Sandwich Composites
Fabrication and Characterization
About This Book
A composite sandwich panel is a hybrid material made up of constituents such as a face sheet, a core, and adhesive film for bonding the face sheet and core together. Advances in materials have provided designers with several choices for developing sandwich structures with advanced functionalities. The selection of a material in the sandwich construction is based on the cost, availability, strength requirements, ease of manufacturing, machinability, and post-manufacturing process requirements. Sandwich Composites: Fabrication and Characterization provides insights into composite sandwich panels based on the material aspects, mechanical properties, defect characterization, and secondary processes after the fabrication, such as drilling and repair.
FEATURES
-
- Outlines existing fabrication methods and various materials aspects
-
- Examines composite sandwich panels made of different face sheets and core materials
-
- Covers the response of composite sandwich panels to static and dynamic loads
-
- Describes parameters governing the drilling process and repair procedures
-
- Discusses the applications of composite sandwich panels in various fields
-
- Explores the role of 3D printing in the fabrication of composite sandwich panels
Due to the wide scope of the topics covered, this book is suitable for researchers and scholars in the research and development of composite sandwich panels. This book can also be used as a reference by professionals and engineers interested in understanding the factors governing the material properties, material response, and the failure behavior under various mechanical loads.
Frequently asked questions
Information
1 Introduction to Sandwich Composite Panels and Their Fabrication Methods
Contents
- 1.1 What Are Sandwich Composite Structures?
- 1.2 Brief History of Sandwich Composite Structures
- 1.3 Common Materials Used in Composite Sandwich Structures and Their Properties
- 1.3.1 Face Materials
- 1.3.2 Core Materials
- 1.3.2.1 Foams or Solid Cores
- 1.3.2.2 Corrugated or Truss Cores
- 1.3.2.3 Honeycomb Structures
- 1.3.3 Adhesive Materials
- 1.3.3.1 Epoxy Resins and Toughened Epoxies
- 1.3.3.2 Phenolics
- 1.3.3.3 Polyurethanes
- 1.3.3.4 Urethane Acrylates
- 1.3.3.5 Polyester and Vinyl Ester Resins
- 1.4 Fabrication Methods for Composite Sandwich Laminates
- 1.4.1 Hand Layup Process
- 1.4.2 Compression Moulding Process
- 1.4.3 Filament Winding Process
- 1.4.4 Vacuum Bagging and Autoclave Moulding Process
- 1.4.5 Pultrusion Process
- 1.4.6 Resin Transfer Moulding (RTM)
- 1.4.7 Additive Manufacturing Processes
- 1.5 Conclusions
- References
1.1 What Are Sandwich Composite Structures?
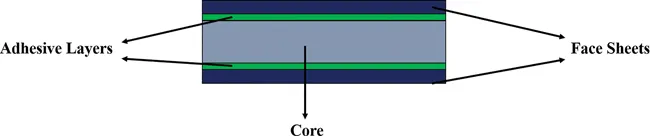
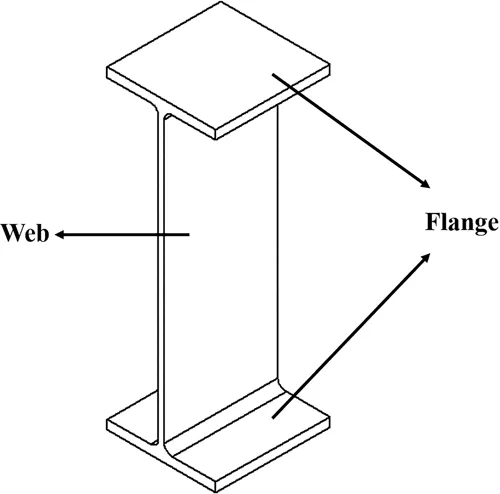
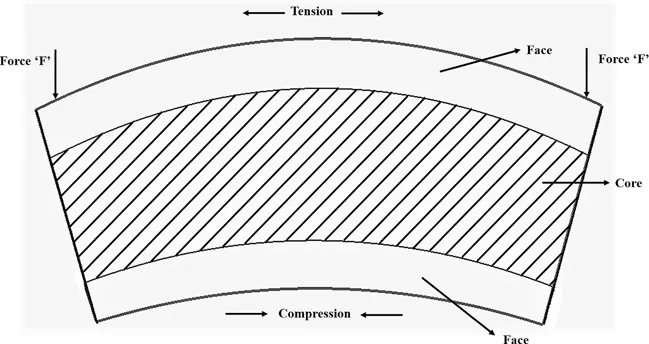
1.2 Brief History of Sandwich Composite Structures
1.3 Common Materials Used in Composite Sandwich Structures and Their Properties
1.3.1 Face Materials
1.3.2 Core Materials
Table of contents
- Cover
- Half Title
- Title Page
- Copyright Page
- Table of Contents
- Preface
- Editors
- Contributors
- Chapter 1 Introduction to Sandwich Composite Panels and Their Fabrication Methods
- Chapter 2 Corrugated Core- and Fold Core-Based Sandwich Panels
- Chapter 3 Metallic Core- and Truss Core-Based Composite Sandwich Panels
- Chapter 4 Composite Sandwich Panels with the Metallic Facesheets
- Chapter 5 Failure Behavior and Residual Strength of the Composite Sandwich Panels Subjected to Compression after Impact Testing
- Chapter 6 Low-Velocity Impact Response of the Composite Sandwich Panels
- Chapter 7 High-Velocity Impact Properties of the Composite Sandwich Panels
- Chapter 8 Investigation of Blast Loading Response of the Composite Sandwich Panels
- Chapter 9 Flexural Behavior of Reinforced Concrete Sandwich Wall Panels Enabled by Fiber-Reinforced Polymer (FRP) Connectors
- Chapter 10 Axial Behavior of Reinforced Concrete Sandwich Wall Panels Enabled by Fiber-Reinforced Polymer (FRP) Connectors
- Chapter 11 Enhanced Failure Behavior for Sandwiches with Hybrid Wire Mesh/FRP Face Sheets
- Chapter 12 Low-Velocity Impact Behaviour of Textile-Reinforced Composite Sandwich Panels
- Chapter 13 Drilling and Repair of the Composite Sandwich Panels
- Chapter 14 Composite Sandwich Structures in the Marine Applications
- Chapter 15 Composite Sandwich Structures in Aerospace Applications
- Chapter 16 Crashworthiness Applications of the Composite Sandwich Structures
- Chapter 17 Role of 3D Printing in the Fabrication of Composite Sandwich Structures
- Index