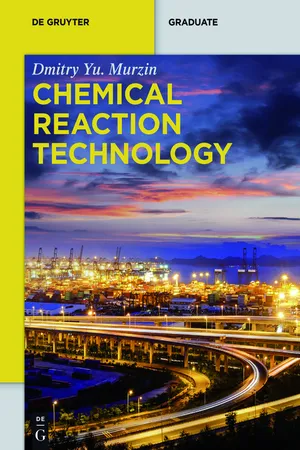
This is a test
- 440 pages
- English
- ePUB (mobile friendly)
- Available on iOS & Android
eBook - ePub
Chemical Reaction Technology
Book details
Book preview
Table of contents
Citations
Frequently asked questions
At the moment all of our mobile-responsive ePub books are available to download via the app. Most of our PDFs are also available to download and we're working on making the final remaining ones downloadable now. Learn more here.
Both plans give you full access to the library and all of Perlego’s features. The only differences are the price and subscription period: With the annual plan you’ll save around 30% compared to 12 months on the monthly plan.
We are an online textbook subscription service, where you can get access to an entire online library for less than the price of a single book per month. With over 1 million books across 1000+ topics, we’ve got you covered! Learn more here.
Look out for the read-aloud symbol on your next book to see if you can listen to it. The read-aloud tool reads text aloud for you, highlighting the text as it is being read. You can pause it, speed it up and slow it down. Learn more here.
Yes, you can access Chemical Reaction Technology by Dmitry Yu. Murzin in PDF and/or ePUB format, as well as other popular books in Ciencias físicas & Química industrial y técnica. We have over one million books available in our catalogue for you to explore.
Information
Chapter 1
Chemical technology as science
1.1 Basic principles
Chemical technology can be defined as a science of converting natural resources or other raw materials into the desired products at the industrial scale using chemical transformations in a technically and economically feasible and socially acceptable way. Besides being based on sound economical considerations, chemical production should nowadays take into account ecological aspects, safety requirements, and labor conditions.
Chemical technology investigates chemical processes (whose structures had been given in Fig. 1.1), which comprise feed purification, reactions per se, separation, and product purification.
Chemical technology is not limited only to chemical transformations per se, as there are other various physical, physico-chemical, and mechanical processes in the production of chemicals.
Criteria of a process quality are technological parameters (productivity, conversion, yield, product purity) as well as economical (costs, profitability, etc.) and ecological ones.
Success in implementation of a novel technology requires its robustness, reliability, safety, environmental compliance as well as significant gains over existing processes.
Methods of chemical technology are used also in non-chemical industries, such as transport, metallurgy, building construction, electronic industry.
Chemical technology as a discipline is based on the following:
- – Physical chemistry and chemical reaction engineering, covering stoichiometry, thermodynamics, mass transfer, kinetics, and various types of catalysis Fig. 1.1: General structure of chemical processes.
- – Unit operations, which include besides reactors also various separation processes, such as absorption, adsorption, distillation, extraction
- – General process considerations, viewing chemical production as a chemical technological system and applying principles of conceptual process design, process intensification, and green chemical engineering
Let us consider as an example hydrogenation of benzene. For a physical chemist, the reaction will look like C6H6 + 3H2 = C6H12 – ΔH, leading to a conclusion that the reaction is reversible and exothermal and that the parameters that could be used to alter equilibrium are temperature and concentrations (pressures) of reagents. When developing a process technology of benzene hydrogenation, other parameters aside from the issues mentioned above should be considered such as availability of the feedstock and energy, reactor type, other pieces of equipment needed, the phase in which the reaction should take place (gas or liquid), the optimal conditions from the viewpoint of economics, and minimization of the negative impact on the environment.
This simple example illustrates that chemical technology is different from organic (inorganic) and physical or other branches of chemistry.
1.1.1 Continuous or batch?
Chemical processes in oil refining and production of basic chemicals are mainly continuous, while in production of specialty and fine chemicals, they could be continuous and periodical. The latter mode of operation can be also used in the secondary processes (i.e., separation, catalyst regeneration) even for large-scale production in chemical process industries (sometimes abbreviated as CPIs).
Continuous processes typically require constant technological parameters (pressure, flows, temperature). Such processes are mainly aimed at production of a single product. In periodical (batch) processes, several products could be made under somewhat similar conditions.
Semi-periodical processes can be also applied in continuously operating units, with, however, a change of a product after a certain period of time.
Continuous mode of operation allows constant quality of products, very efficient utilization of the equipment, high degree of process automation and control, and finally, much more efficient and safe processes.
In order to organize a continuous process, the following conditions should be fulfilled:
- – separation of inlet and outlet in a reactor space
- – continuous and substantially stationary flows of reactants and products (even if there are several successful examples of non-stationary operation)
- – the products should be the same during the operation
- – continuous flow of products inside reactors and other equipment and between them
These conditions can be well maintained when liquid and gaseous products are processed, while transport and handling of solids can be much more complicated.
The majority of process units can be utilized in a continuous mode. If, by some reason, a reactor dedicated for continuous operation cannot be used, reactors designed for discontinuous (batch) operations can be combined together in a cascade (Fig. 1.2).
There are operations that are inherently periodic, such as adsorption or absorption requiring regular regenerations of liquid or solid sorbents. To circumvent apparent difficulties in organizing such operations, two units can be coupled subsequently (absorption or extraction columns followed by regeneration).
For adsorption, a cascade of adsorbers (Fig. 1.3) having different operations at a particular moment in time (adsorption, drying and cooling of adsorbent, desorption) could be used. Alternatively, moving or fluidized beds of adsorbents can be arranged. In the first case, there is a need for a fast switch of large flows, while the drawback of the second case is attrition.

Fig. 1.2: Reactors in a cascade.
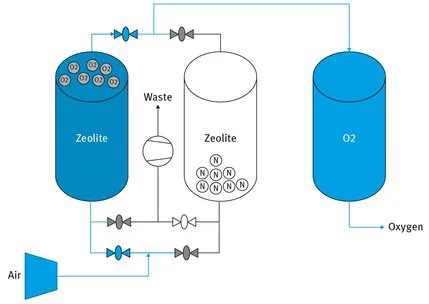
Fig. 1.3: Vacuum pressure swing adsorption in two absorbers. http://www.ranacaregroup.com/on-site-gas-systems/about-gas-generation.
Same difficulties could arise for continuous processes involving handling of solids, such as filtration or crystallization. Even in such cases, continuous processes are beneficial.
1.1.2 Multilevel chemical processing
The cornerstones of chemical technology will be considered in Chapters 1–3 of this textbook, but not in the level of detail available in the specialized literature. At the same time, the most essential features will be presented, targeting chemists as potential readers, who might be less familiar with chemical engineering.
Processing of chemicals is very complex with several levels to be considered:
- – Molecular level or level of a mechanism of chemical reactions. Such microlevel includes description of kinetics, molecular level catalysis, surface chemistry, processing of solids.
- – Macrokinetics level, which addresses interactions and processes at a level of a catalyst granule, gas bubbles, etc., describing various heat and mass transfer processes.
- – The level of a moving fluid (gas or liquid), which addresses the flow type (laminar or turbulent) and its characteristics (concentration and temperature gradients in axial and radial directions).
- – Level of a reactor and other units, when reactor technology, unit operations, and scaling up are considered.
- – Process technology level, which also includes process design and control.
A famous French chemical engineer, J. Villermaux, placed chemical technology in a broader context of space and time scale (Fig. 1.4). The commercially attractive range of reactivity is rather limited, since reactions should occur within a reasonable time (or space time) in a reasonably sized reactor. The reactor dimensions might vary depending on the production capacity, in some cases having large volumes (100 m3) or height (40–70 m). In the case of catalytic processes, higher activity and selectivity of a particular catalyst result in a decrease in equipment size and substantia...
Table of contents
- De Gruyter Graduate - Murzin • Chemical Reaction Technology
- Also of interest
- Titel
- Impressum
- Preface
- About the author
- Inhaltsverzeichnis
- Chapter 1 - Chemical technology as science
- Chapter 2 - Physico-chemical foundations of chemical processes
- Chapter 3 - Chemical processes and unit operations
- Chapter 4 - Chemical process industry
- Chapter 5 - Hydrogen and syngas generation
- Chapter 6 - Cracking
- Chapter 7 - Catalytic reforming of gasoline fractions: combining isomerization and dehydrogenation
- Chapter 8 - Halogenation
- Chapter 9 - Oxidation
- Chapter 10 - Hydrogenation and dehydrogenation
- Chapter 11 - Reactions involving water: hydration, dehydration, etherification, hydrolysis, and esterification
- Chapter 12 - Alkylation
- Chapter 13 - Reactions with CO, CO2, and synthesis gas
- Chapter 14 - Key reactions in the synthesis of intermediates: nitration, sulfation, sulfonation, alkali fusion, ketone, and aldehyde condensation
- Chapter 15 - Polymerization
- Final words
- Index