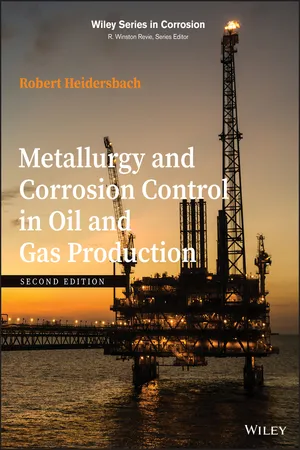
- English
- ePUB (mobile friendly)
- Available on iOS & Android
Metallurgy and Corrosion Control in Oil and Gas Production
About This Book
Details the proper methods to assess, prevent, and reduce corrosion in the oil industry using today's most advanced technologies
This book discusses upstream operations, with an emphasis on production, and pipelines, which are closely tied to upstream operations. It also examines protective coatings, alloy selection, chemical treatments, and cathodic protectionâthe main means of corrosion control. The strength and hardness levels of metals is also discussed, as this affects the resistance of metals to hydrogen embrittlement, a major concern for high-strength steels and some other alloys. It is intended for use by personnel with limited backgrounds in chemistry, metallurgy, and corrosion and will give them a general understanding of how and why corrosion occurs and the practical approaches to how the effects of corrosion can be mitigated.
Metallurgy and Corrosion Control in Oil and Gas Production, Second Edition updates the original chapters while including a new case studies chapter. Beginning with an introduction to oilfield metallurgy and corrosion control, the book provides in-depth coverage of the field with chapters on: chemistry of corrosion; corrosive environments; materials; forms of corrosion; corrosion control; inspection, monitoring, and testing; and oilfield equipment.
- Covers all aspects of upstream oil and gas production from downhole drilling to pipelines and tanker terminal operations
- Offers an introduction to corrosion for entry-level corrosion control specialists
- Contains detailed photographs to illustrate descriptions in the text
Metallurgy and Corrosion Control in Oil and Gas Production, Second Edition is an excellent book for engineers and related professionals in the oil and gas production industries. It will also be an asset to the entry-level corrosion control professional who may have a theoretical background in metallurgy, chemistry, or a related field, but who needs to understand the practical limitations of large-scale industrial operations associated with oil and gas production.
Frequently asked questions
Information
1
INTRODUCTION TO OILFIELD METALLURGY AND CORROSION CONTROL
- Upstream
- Downstream
- Pipelines
COSTS
SAFETY
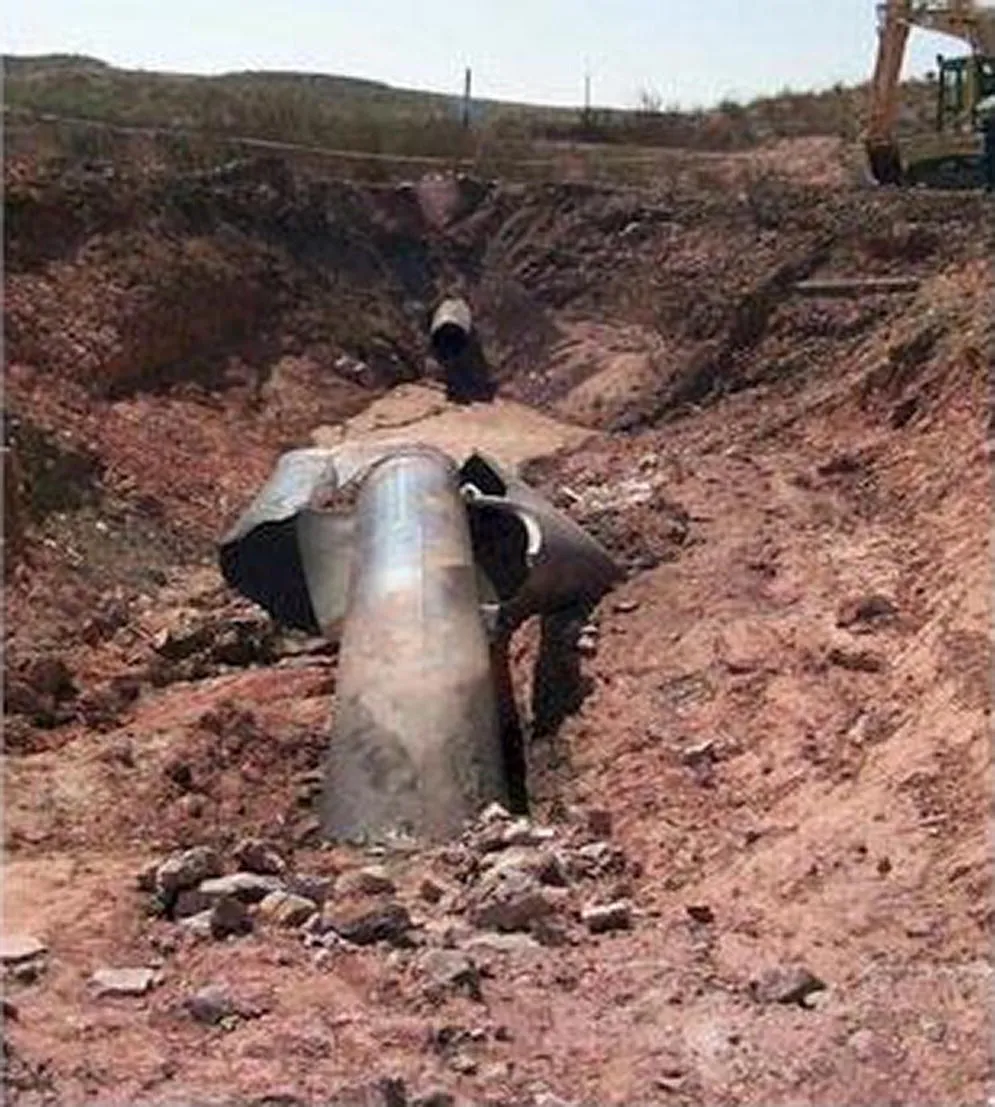
ENVIRONMENTAL DAMAGE


Table of contents
- COVER
- TABLE OF CONTENTS
- PREFACE
- 1 INTRODUCTION TO OILFIELD METALLURGY AND CORROSION CONTROL
- 2 CHEMISTRY OF CORROSION
- 3 CORROSIVE ENVIRONMENTS
- 4 MATERIALS
- 5 FORMS OF CORROSION
- 6 CORROSION CONTROL
- 7 INSPECTION, MONITORING, AND TESTING
- 8 OILFIELD EQUIPMENT
- INDEX
- END USER LICENSE AGREEMENT