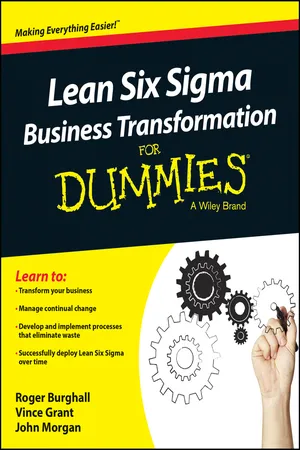
eBook - ePub
Lean Six Sigma Business Transformation For Dummies
This is a test
- English
- ePUB (mobile friendly)
- Available on iOS & Android
eBook - ePub
Lean Six Sigma Business Transformation For Dummies
Book details
Book preview
Table of contents
Citations
About This Book
Use Lean Six Sigma to transform your business.
Lean Six Sigma is a powerful method for improving both the efficiency and quality of projects and operations. In this new book, the team that bought you Lean Six Sigma For Dummies shows you how to take Lean Six Sigma to the next level and manage continual change in your organization. You'll learn to design a roadmap for transformation that's tailored to your business objectives; develop and implement processes that eliminate waste and variation across the company; synchronize your supply chain; and successfully deploy Lean Six Sigma over time.
Lean Six Sigma Business Transformation For Dummies shows you how to:
- Define your transformation objectives and create a bespoke 'Transformation Charter' for your organization.
- Assess your company's readiness for transformation.
- Establish a 'Transformation Governance System' to help you manage the transformation programme effectively.
- Bring your people with you! Plan and achieve the cultural change needed to make the transformation process successful.
- Join up the dots between planning and effective execution with Strategy Deployment.
- Deploy a 'Continuous Improvement' toolkit to achieve everyday operational excellence.
- Sustain the transformation programme and widen the scope across the organization (including deploying to the supply chain).
- Adopt a 'Capability Maturity Approach' to drive business improvement â recognizing that change is a continuous transformational journey, just as pioneers like Toyota have done.
- Use a range of Lean Six Sigma Tools â using the right tools, at the right time (and in the right order!) enables continuous improvement by eliminating waste and process variation.
Frequently asked questions
At the moment all of our mobile-responsive ePub books are available to download via the app. Most of our PDFs are also available to download and we're working on making the final remaining ones downloadable now. Learn more here.
Both plans give you full access to the library and all of Perlegoâs features. The only differences are the price and subscription period: With the annual plan youâll save around 30% compared to 12 months on the monthly plan.
We are an online textbook subscription service, where you can get access to an entire online library for less than the price of a single book per month. With over 1 million books across 1000+ topics, weâve got you covered! Learn more here.
Look out for the read-aloud symbol on your next book to see if you can listen to it. The read-aloud tool reads text aloud for you, highlighting the text as it is being read. You can pause it, speed it up and slow it down. Learn more here.
Yes, you can access Lean Six Sigma Business Transformation For Dummies by Roger Burghall, Vince Grant, John Morgan in PDF and/or ePUB format, as well as other popular books in Commerce & Gestion de projet. We have over one million books available in our catalogue for you to explore.
Information
Part I
Getting Started with Lean Six Sigma

For Dummies can help you get started with lots of subjects. Visit www.dummies.com to learn more and do more with For Dummies.
In this part âŚ
- Find out more about Lean Six Sigma and âtransformationâ and why itâs needed.
- Learn about transformation and the link to Strategy deployment.
- Get to know the DRIVE Model and how to apply it.
Chapter 1
Introducing Lean Six Sigma
In This Chapter



As well as an overview of the broad content of this book, this chapter provides an introduction to what we mean by transforming an organisation and why your organisation may need it. We take a brief look at the DRIVE and Plan, Do, Check, Act models that provide the framework for deploying the strategy that leads to transformation. The chapter also provides a reminder of the key principles of Lean Six Sigma and the DMAIC and DMADV methods used to improve existing processes or design and create new ones.
Defining Transformation
The Oxford English Dictionary describes transformation as âa marked change in form, nature or appearanceâ. And in the context of business transformation that definition is a pretty accurate fit.
You may need to address organisational problems such as high error rates in dealing with customer orders, which in turn lead to increased complaints and ultimately loss of market share. But a burning platform situation may not exist at all. The organisation may be targeting growth in some way, perhaps through an entirely new market or product range, for example. It might even be seeking to change its identity and with it the perceptions of the marketplace.
One way or another, though, your organisation is seeking a marked change, be it in performance, appearance or both. And almost certainly, the change is likely to require a change of thinking and behaviour on the part of the people in the organisation, especially the leaders and managers.
Whatever the rationale thatâs driving the need for transformation, a crystal clear link to the organisationâs strategy and its deployment is essential. The PlanâDoâCheckâAct (PDCA) cycle comes into play here in terms of the planning for and support of the transformation and the deployment of strategy.
A business transformation takes time to achieve and requires the organisation to utilise an effective implementation methodology â the DRIVE model (Define, Review, Improve, Verify and Establish) â and to create a capability maturity roadmap to support the changes. The capability maturity roadmap provides a phased approach to deploying Lean Six Sigma capability in the organisation. Chapter 3 covers the DRIVE model and the capability maturity roadmap in more detail.
This book focuses on Lean Six Sigma as the vehicle to support and drive the changes needed in thinking and behaviour, and that also provides a framework for the improvement projects that emerge through the journey ahead. We provide only a relatively brief summary of the ins and outs of Lean Six Sigma, however, as it is described in detail in Lean Six Sigma For Dummies (Wiley).
Before we look at Lean Six Sigma in a little more detail, however, we need to take a look at the PDCA cycle.
Introducing the PlanâDoâCheckâAct Cycle
The PlanâDoâCheckâAct (PDCA) cycle, as illustrated in Figure 1-1, provides a foundation for strategy deployment.

Figure 1-1: The PlanâDoâCheckâAct (PDCA) cycle.
Although not overtly referred to in the Lean Six Sigma methodology, the PDCA cycle is very much at the heart of the DMAIC improvement method described in Chapter 2. The PDCA cycle breaks down as follows:
- Plan: This element refers to your theory or hypothesis. If you do this, you expect that to happen.
- Do: Here you put your theory to the test. Ideally, you undertake pilot activities or tests.
- Check: Here you look to see whether the outcomes of your actions in the Do phase are producing the results your Plan led you to expect. To do that properly, you need to ensure you gather the right data and also that youâre viewing things from the correct perspective, something you will have determined in the Plan phase. Lean Six Sigma helps you get the measures right, but you need to recognise the importance of going to see actual results in the workplace â the âgembaâ, as the Japanese call it.
- Act: Depending on your findings in the Check phase, you may need to make adjustments to the theory you developed in the Plan phase and then run through another PDCA cycle. If things have gone according to plan, however, you can act to put your theory formally in place, or run a larger test depending on the scale of the pilot.
We return to the PDCA cycle throughout the book.
Showing the Way with Lean Six Sigma
To apply the Lean Six Sigma approach successfully, you need to recognise the need for different thinking. To paraphrase Albert Einstein:
âThe significant problems we face cannot be solved at the same level of thinking we were at when we created them.â
You want to change outcomes but you also need to realise that they are themselves the outcomes from your systems. Not the computer systems, but the way in which people work together and interact. And these systems are the product of how people think and behave. So, if you want to transform and change the outcomes you have to change your systems, and to do that, you have to change your thinking.
You need to adopt thinking that focuses on improving value for the customer by improving and smoothing the process flow and eliminating waste. Since the establishment of Henry Fordâs first production line, lean thinking has evolved over many years and in the hands of many people and organisations, but much of the development has been led by Toyota through the creation of the Toyota Production System. Toyota was able to build on Fordâs production ideas to move from âhigh volume, low varietyâ to âhigh variety, low volumeâ.
Six Sigma thinking complements the lean approach through a systematic and robust approach to improvement that is based on management by fact. In particular, it looks to get the right data, in order to understand and reduce the variation in performance being experienced in the organisationâs products, services and processes.
Identifying the key principles of Lean Six Sigma
Lean is not about cutting things to the bone. Rather, itâs about providing value for your customers. Taiichi Ohno, the architect of the Toyota Production System, sums up the approach in a nutshell:
âAll we are doing is looking at a time line from the moment the customer gives us an order to the point when we collect the cash. And we are reducing that time line by removing the non-value-added wastes.â
And value is what customers are looking for. They want the right products and services, at the right place, at the right time and at the right quality. Value is what the customer is willing to pay for.
Explaining Lean thinking
Weâre sure youâre aware of the half-full, half-empty glass analogy applied to whether someone looks on the positive or negative side. A Lean practitioner might well respond by saying âitâs the wrong sized glass!â Either way, you first need to understand the customer and their perception of value. You have to know how the value stream operates and enable it to flow, perhaps by removing waste and non-value-added activities.
Lean thinking also means looking for ways of smoothing and levelling the way the work flows through the process and, where possible, working at the customerâs pace â in other words, itâs a pull rather than a push process. And, of course, in the pursuit of perfection, youâre always looking to improve things through the concept of continuous improvement.
Linking up with Six Sigma thinking
Six Sigma thinking is very similar to Lean thinking. Six Sigma also focuses on the customer. A key principle of Six Sigma is understanding customer requirements and trying to meet them. If you donât understand those requirements, how can you expect to provide the customer with value?
Again, as with Lean thinking, to understand your processes you need to understand how the work gets done. Data comes into play more so with Six Sigma thinking than with Lean thinking. If youâre to manage by fact, you need to have the right measures in place and the data presented in the most appropriate way.
An appreciation and understanding of the variation in your process results enables you to more effectively interpret your data and helps you know when, and when not, to take action.
Six Sigma thinking also means equipping the people in the process so that theyâre fully involved and engaged in the drive for improvement.
Accessing the best of both worlds
Similarity and synergy exist between Lean thinking and Six Sigma and combining the two approaches creates a âmagnificent sevenâ of Lean Six Sigma key principles:
- Focus on the customer.
- Identify and understand how the work gets done â the value stream.
- Manage, improve and smooth the process flow.
- Remove non-value-adding steps and waste.
- Manage by fact and reduce variation.
- Involve and equip the people in the process.
- Undertake improvement activity in a systematic way.
In L...
Table of contents
- Cover
- Title Page
- Table of Contents
- Introduction
- Part I: Getting Started with Lean Six Sigma
- Part II: Scoping the LSS Transformation Journey
- Part III: Planning the Transformation Journey
- Part IV: Starting out on the Transformation Journey
- Part V: Sustaining the Transformation
- Part VI: The Part of Tens
- About the Authors
- Cheat Sheet
- End User License Agreement